製造業DXの鍵はBOP!システムによる工程データの一元管理とBOP活用法
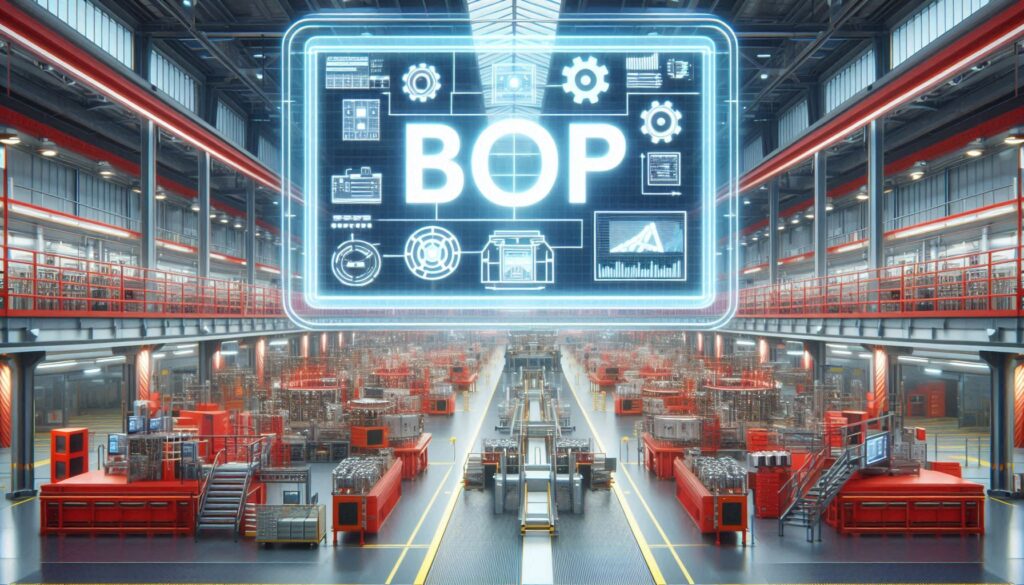
製造業の現場では、工程が属人化していたり、設計と製造の間で情報が分断されていたりと、非効率な業務がいまだに多く残っています。そうした中で注目されているのが、BOP(Bill of Process)という概念です。
「製品をどう作るか」という情報を体系的に管理するBOPは、製造業DXの基盤となる仕組みとして導入が進みつつあります。しかしながら、BOPは単体で活用するものではなく、ERPやMES、PLMなどのシステムと連携することで、その真価を発揮します。
この記事では、BOPの基本から、各システムとの関係、活用の実例、そして運用上の注意点まで、幅広く解説します。BOPの導入によって実現できる、工程情報の一元管理と製造業DXの未来像を一緒に探っていきましょう。
目次
BOPとは?製造業における役割と注目される背景
BOPとは何か?工程情報を体系的に管理する仕組み
BOP(Bill of Process)とは、製品を「どう作るか」に関する工程情報を体系的に定義・管理する仕組みです。作業手順、設備、投入タイミング、加工条件、作業時間など、製造工程に必要な情報を一元化します。
BOPを整備することで、工程の標準化、情報の共有、製造準備の効率化が進みます。属人化の排除や変更管理の強化にもつながり、製造業におけるデジタル化と全体最適を支える重要な情報基盤となります。
製造業で工程情報が重要視される理由
近年、製造現場では多品種少量生産や短納期対応などが求められており、現場での判断やノウハウの属人化を解消することが課題となっています。
そこで注目されているのが、工程情報の標準化と共有化です。BOPを活用することで、工程情報を一元的に整備・管理し、製造品質や効率を安定化させることが可能になります。
BOPが製造業DXで果たす役割とは?
情報の断絶・属人化からの脱却
従来、製造現場では、工程に関する情報が紙ベースや個人のノウハウに依存しており、部門間での情報断絶や属人化が大きな課題でした。BOPを整備することで、こうした断絶を埋め、全体の工程情報を見える化・標準化できます。
工程情報を軸にしたデジタル化の効果
BOPの導入により、設計部門から製造部門、さらには調達や品質管理まで、工程を軸とした情報の一貫性が生まれます。これにより、製品の仕様変更に伴う製造工程の再構成や、品質問題の原因追跡などにもスムーズに対応できるようになります。
BOPを活用できる代表的なシステムとその役割
BOPは単独で活用するものではなく、さまざまな業務システムと連携することで、その価値を最大限に発揮します。ここでは、製造業で特に関係の深い4つのシステム、ERP、MES、PLM、生産スケジューラー、について、それぞれの役割とBOPとの関係を具体例を交えて解説します。
ERP:生産指示・原価計算への展開
ERP(Enterprise Resource Planning)は、生産・在庫・調達・会計など、企業の基幹業務を統合的に管理するシステムです。ERPにBOPの工程情報を活用することで、製品ごとの工程情報が正確に反映された製造指示が可能となり、部門間での情報の一貫性が向上します。
たとえば、ある自動車部品メーカーでは、BOPに基づいてERPで製造指示を作成することで、各工程で必要な作業時間やリソースを事前に把握できるようになり、工程別のコスト積算や原価管理が飛躍的に精緻化しました。また、実際の生産計画に応じて、材料手配や外注工程のタイミング調整も自動化され、納期遵守率の向上にも寄与しています。
MES:現場作業指示と実績収集の標準化
MES(Manufacturing Execution System)は、製造現場における作業指示、実績収集、品質管理などを担うシステムです。MESにBOPで定義された作業手順を反映することで、現場に対して工程ごとの標準化された作業指示を自動で配信することができます。
たとえば、電子機器を製造する企業では、設計段階で定義したBOPの工程情報をもとに、MESが作業手順や設備、材料投入順を展開し、現場にリアルタイムで指示を出しています。また、各工程の実績や不良情報もBOPと紐づけて記録され、後工程でのトラブル発生時には原因を遡って特定できます。これにより、作業のばらつきを抑え、標準化された工程の安定運用を実現するとともに、改善サイクルが回りやすくなり、品質向上やトレーサビリティ強化にもつながっています。
PLM:設計データと工程の一貫管理
PLM(Product Lifecycle Management)は、製品の企画から設計・開発、製造、廃棄までの全ライフサイクルを管理するためのシステムです。PLMでBOP情報を一元管理することで、設計段階で定義された仕様や変更情報が、スムーズに製造工程へ反映されるようになります。
たとえば、産業機械メーカーでは、PLM上で設計データとともにBOPも管理し、製造部門に工程情報を自動連携しています。これにより、設計変更時に影響を受ける工程が即座に特定でき、製造準備にかかるリードタイムを短縮することに成功しました。さらに、設計者と製造現場のコミュニケーションの質も向上し、手戻りの発生率も大幅に低下しています。
生産スケジューラー:工程時間・順序情報による負荷調整
生産スケジューラーは、生産計画の立案や設備・人員の負荷調整を行うためのツールです。BOPに定義された工程順序や作業時間の情報を生産スケジューラーに取り込むことで、現実に即したスケジューリングが可能になります。
たとえば、精密部品を多品種少量で製造する企業では、BOPを活用することで、各製品に必要な工程時間や段取り時間を正確にスケジューラーに取り込み、現場の設備負荷に応じた計画が立てられるようになりました。その結果、ピーク時の工程詰まりや納期遅延が解消され、生産計画の実行率が改善しています。
BOPは、これらのシステムそれぞれに対して異なる角度から価値を提供します。ERPでは全体計画やコスト管理、MESでは作業実行の標準化、PLMでは設計情報との一貫性、スケジューラーでは実行性の高い生産計画立案というように、各システムがBOPという共通の工程情報を基盤とすることで、製造業全体の連携精度と柔軟性が高まるのです。
このように、BOPは単なる工程データの集まりではなく、企業全体のシステムと情報をつなぐ中核的な存在であるといえます。
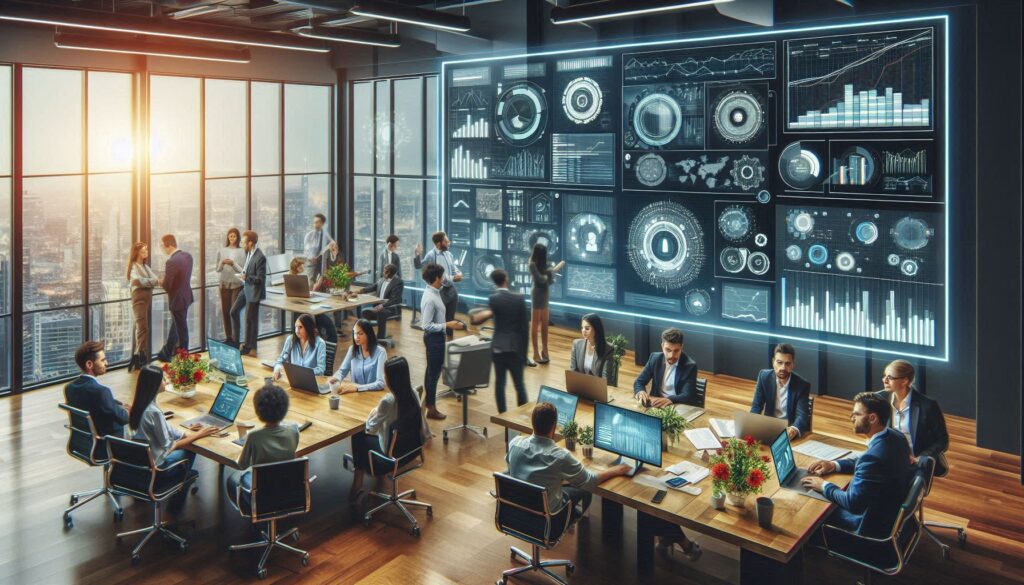
システムによる工程データの一元管理とは?
各システム間での工程情報の整合性確保
BOPを軸とした情報構造を整えることで、ERP、MES、PLM、生産スケジューラーなど、複数の業務システム間で工程情報の整合性を保つことが可能になります。各システムごとに工程データがバラバラに存在している状態では、同じ製品でもシステム間で工程順序や設備名、加工条件が異なってしまうことがあり、情報の不一致による手戻りや誤作業が発生しやすくなります。
たとえば、ある精密機器メーカーでは、PLMとMESで管理している工程名にばらつきがあり、設計変更後に製造現場への反映が遅れる事例が繰り返されていました。そこで、BOPを基準とした統一マスタを整備し、各システムで共通の工程IDと命名規則を使用するようにした結果、設計変更が即座に製造工程へ反映されるようになり、手戻りの工数が約30%削減されました。
マスタ統合と工程の再利用性向上
BOPを整備することは、単なる工程の整理にとどまらず、工程マスタの統合と、過去の工程データを活用して効率的に新しい製品の製造準備を進めることにもつながります。従来、製品ごとに個別の工程が定義されていた場合、同じ作業内容が重複して登録され、無駄な管理や修正作業が発生してしまいます。
たとえば、ある電子部品メーカーでは、製品ごとに工程をバラバラに定義していたため、共通作業が多数存在しているにもかかわらず、名称や手順の違いにより作業標準が統一されていない状態でした。そこでBOPを用いて作業単位で工程パーツを標準化し、製品ごとの工程定義に過去の工程データを組み合わせて再利用できる仕組みに変更したところ、工程設計の工数が大幅に削減されました。
そして、BOPのメリットを最大限に活かすためには、BOPに対応したシステムの導入が欠かせません。「Smart Craft」はBOPに対応したMESであり、SaaSでの提供のため従来のオンプレミス型に比べ、初期コストが低く、スムーズな導入と迅速な運用が可能です。
設計から製造まで、BOPの活用フェーズ別の実例
設計時の工程定義と設計変更対応
設計段階でBOPを意識して工程情報を定義することで、加工や組立のしやすさ、コストや品質、作業性などを考慮し、製造現場で無理なく効率的に作れるようにする設計、つまり、製造性を考慮した設計(DfM)が実現します。また、設計変更が発生した場合にも、工程への影響が明確になり、迅速な反映が可能です。
設計段階でBOPを意識して工程情報を定義することで、が可能になります。また、設計変更が発生した場合にも、工程への影響が明確になり、迅速な反映が可能です。
生産計画への展開
工程情報に基づいた正確な計画立案が可能になることで、設備や人員の負荷調整、納期シミュレーション、工程間のボトルネック解消にも貢献します。
製造現場での作業指示・実績収集との連携
BOPをもとにした作業指示は、標準作業書の自動生成や、作業手順の統一化につながります。また、MESと連携すれば、作業実績や不良情報を工程単位で記録し、トレーサビリティの強化も実現します。
BOP活用における課題と運用上の注意点
工程情報整備の難しさと属人化の壁
BOPを整備するには、各工程の詳細情報を現場から正確にヒアリングし、構造化する必要があります。ここで壁になるのが、属人化されたノウハウの形式知化です。現場の協力を得ながら、段階的に整理していくことが求められます。
情報更新と現場運用のバランス
工程変更や設計変更に対して、BOPを常に最新に保つには、情報更新の体制とルール作りが欠かせません。また、システム上で定義されたBOPが、現場の実態と乖離しないよう、双方向のコミュニケーションも重要です。
導入を成功に導くための社内体制と段階的アプローチ
BOPの導入は一度に完結できるものではありません。まずは特定製品や一部工程から始め、段階的に拡大していくアプローチが現実的です。また、設計・生産・システム部門を横断するプロジェクト体制の整備も、成功には欠かせません。
BOPをシステムで活かすための運用と導入のポイント
マスタ整備・標準化・属人化排除の手順
BOPを活用するためには、まず既存の工程情報を整理・統合し、標準マスタとして再構成することが重要です。その際、現場ごとのバリエーションを把握しつつ、汎用化と例外管理のバランスを取る必要があります。
現場との整合性を保つ運用体制の構築
BOPが「システム上の理想」にとどまらず、現場の実態に即した内容であることが求められます。そのためには、現場との定期的なフィードバックの場を設け、BOPの維持・改善を継続的に行う体制づくりが不可欠です。
まとめ:BOPを中核に据えた製造業DXの進め方
ここまで、BOPの基本からシステムでの活用、BOPの導入・運用の課題まで幅広くお伝えしました。
BOPは、単なる「工程情報の整理」ではなく、製造業の全体最適を実現するための情報基盤です。設計から製造、計画、実行に至るまで、BOPを中心に据えることで、属人化を防ぎ、情報の一貫性を保ちながら、持続的な改善活動が可能になります。
DXを進める上で、現場とシステムの両方をつなぐ「共通言語」としてのBOPを、ぜひ活用してみてはいかがでしょうか。
製造現場のデジタル化を支援する「Smart Craft」のご紹介
製造現場のデジタル化は、製造現場の課題を可視化し、生産性向上のみならず、稼ぐ力の向上にに寄与します。効率的な製造現場の実績収集に向けては、各種ソリューションが多くの企業で活用されています。
その中でも、Smart Craftは、国産初のSaaS型MESであり、クラウドベースであるため、導入の際には初期費用を抑えることができ、段階的なシステム導入も可能です。
タブレットやスマホで直感的に操作が可能なため、ITが苦手という従業員でも容易に使用できます。製造現場の工程管理、品質管理、集計・分析をまとめてデジタル化し、ペーパレス化による生産性改善を実現します。まずは資料請求からSmart Craftの導入を検討してみてください。
