MESの要「データ収集」を徹底解説!収集対象・手段・導入効果まで詳しく解説
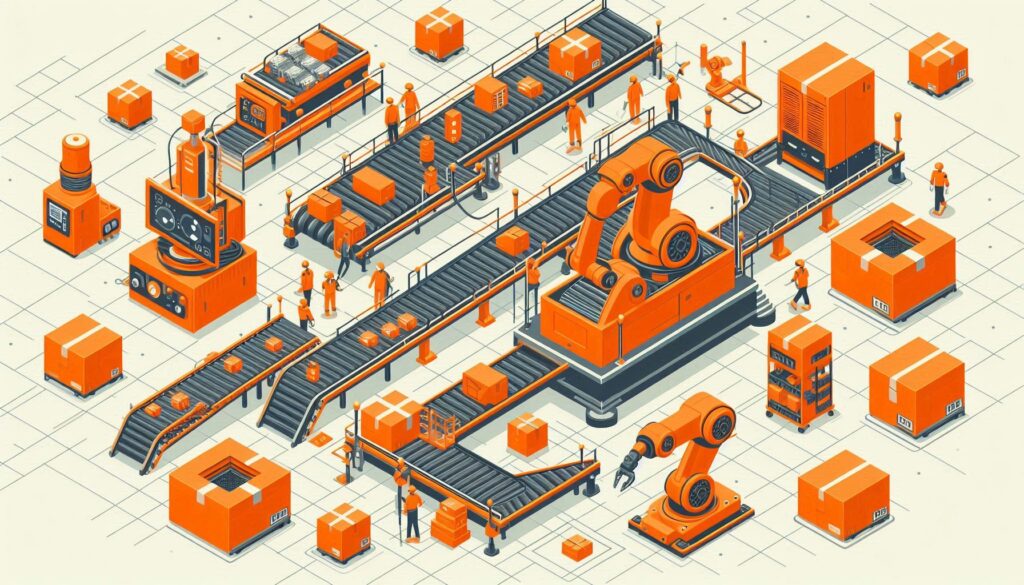
製造現場のデジタル化が進む中で、真っ先に取り組むべきことは何でしょうか。IoTやAIといった華やかなキーワードに目を奪われがちですが、最も重要なのは、データを正しく集めることです。現場で何が起きているのかを、正確かつリアルタイムに把握する仕組みがなければ、改善活動も、効率化も、再現性のあるPDCAサイクルも成り立ちません。
その基盤を担うのが、製造実行システム(MES)における「データ収集」機能です。MESには11の標準機能が定義されていますが、そのすべての土台となるのがこの機能と言っても過言ではありません。この記事では、MESの中でも中核をなす「データ収集」にフォーカスし、収集対象となるデータの種類や手段、導入の効果について詳しく解説します。
目次
なぜデータ収集が製造DXの起点となるのか
製造現場における改善活動やDX(デジタルトランスフォーメーション)推進の第一歩は、「現場の見える化」にあります。そのためには、現場で何が起きているのかを正確かつタイムリーに把握する必要があり、それを支えるのが「データ収集」です。
作業実績や設備の稼働状況、不良品の発生情報など、日々の製造活動で生まれる情報は膨大です。これらを定量的に把握できなければ、改善の打ち手は勘や経験に頼らざるを得ず、再現性あるPDCAサイクルを回すことは困難です。逆に言えば、データ収集こそが改善の出発点であり、製造DXの土台となるのです。
MESとは?11機能における「データ収集」の立ち位置
MES(Manufacturing Execution System)は、現場の作業・設備・品質といった製造プロセス全体をリアルタイムで管理・統制するためのシステムです。国際的には、MESの標準機能として「11機能(MESA-11)」が定義されています。
MESの11機能については以下の記事で詳しく説明していますので参考にしていただければと思います。
その中でも「データ収集(Data Collection)」は、他の10機能を支える基盤機能です。適切なデータをタイムリーに収集できなければ、MESの他の機能も十分に機能しません。
たとえば、進捗把握は実績データがなければできず、品質分析も不良の発生タイミングや作業条件の記録がなければ成り立ちません。まさに「データ収集」はMESの要と言えるでしょう。
データ収集の対象と手段:MESで集めるべき情報とは
MESが現場から収集対象とするデータとその手段には、さまざまな種類があります。本章ではそれらを列挙した上で、それぞれの利点や注意点を詳しく見ていきます。
データ収集の対象
MESが現場から収集対象とするデータとしては、次のようなものが挙げられます。
データの種類 | 内容例(収集項目) | 活用される機能・目的例 |
---|---|---|
作業実績 | 作業開始・終了時間、作業者ID、作業手順、投入数、完成数、など | 工程進捗管理、作業負荷分析、教育・標準化 |
設備稼働情報 | 稼働/停止状態、アラーム発生、停止理由、サイクルタイム | 稼働率分析、保全計画、停止要因分析 |
品質データ | 検査結果、不良品数、不良理由、測定値 | 品質トレース、不良分析、是正措置 |
材料・部品の投入履歴 | ロット番号、使用タイミング、投入量、作業者 | トレーサビリティ、材料歩留まりの分析 |
環境データ | 温湿度、振動、圧力、など | 異常検知、環境変化と品質の相関分析 |
生産指示情報との紐付け | 指示番号、品目コード、数量、納期、など | 実績と計画の差異分析、遅延予測 |
作業者関連情報 | スキルレベル、担当工程、作業履歴 | 教育効果測定、適正配置、人件費配分 |
データ収集の手段
続いて、データ収集の手段としては次のようなものが挙げられます。
データ収集手段 | 特徴・利点 | 留意点・制約 |
---|---|---|
手入力(PC、タブレット等) | 導入が容易で柔軟に対応可能。現場の声を直接反映しやすい。 | 入力ミス・記入漏れのリスクあり。作業者の手間も増える。 |
バーコード読み取り | スピーディに正確な情報を取得でき、誤入力を防止。 | 読み取り機器の設置や運用ルールの徹底が必要。 |
IoTセンサー | 自動的にデータを取得でき、リアルタイム性・精度が高い。 | 初期コストやネットワーク整備が必要な場合がある。 |
PLC・機器連携 | 設備の稼働状態を正確かつ即時に取得可能。工程と連動しやすい。 | 初期コストに加えて、設備側の対応や通信設定など専門知識を要する場合がある。 |
データ収集手段は、安価でスピーディーに開始できるものから、初期投資やインフラ整備が必要なものまで様々です。現場の状況に応じて、適切な手段を組み合わせることが求められます。
スピーディーにデータ収集を開始する方法として、クラウド型のMESが有効です。「Smart Craft」は国産初となるSaaS型のMESであり、従来のオンプレミス型に比べ、初期投資を抑えて、スムーズな導入と迅速な運用が可能です。
データ収集がもたらす3つの効果
製造工程を管理・改善していくうえで、データ収集は次のような具体的な効果をもたらします。
実績と計画のギャップ把握
収集した実績データをもとに、計画通りに作業が進んでいるかを可視化できます。遅れやボトルネックを早期に把握し、工程改善に役立てることができます。
品質トレースの基盤
不良が発生した際、その原因を追跡するためには、どの作業者が・どの設備で・どの条件下で生産したかという情報が必要です。これを可能にするのが、正確な実績データの蓄積です。
作業者のパフォーマンス見える化
作業時間や工程ごとの負荷状況を分析することで、作業者ごとの特性を把握し、適切な人員配置や教育支援にも活用できます。
データ収集から始まるMES活用ステップ
データ収集を起点に、MESは段階的に活用の幅を広げていくことができます。
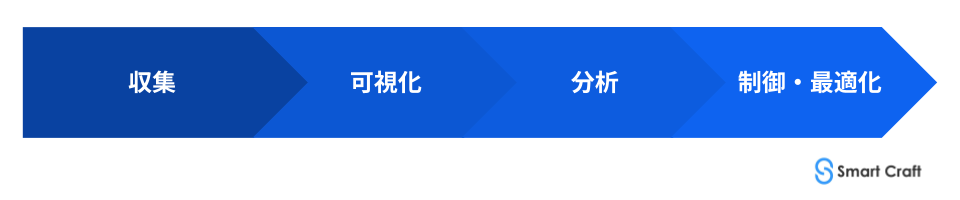
収集 | まずは現場の実績を記録する体制を整える |
可視化 | 収集したデータをもとに、現場の状態をリアルタイムに把握 |
分析 | トラブル傾向や改善余地を見出す |
制御・最適化 | 分析結果をもとに、作業指示やスケジューリングへ反映 |
このように、正確なデータ収集は、MESのほかの機能と連携しながら、改善のサイクルを加速させていく役割を担います。
データ収集が導いた現場改善:MES活用の成功事例
データ収集を起点に現場課題を解決し、生産性向上や稼働率改善につなげた3つの事例をご紹介します。それぞれの目的に必要なデータ収集の対象と、現場に応じたデータ収集手段を活用し、最適な形で成果を生み出した取り組みです。
事例1:製造管理基盤の構築で10%の工数削減を実現
データ収集の手段:タブレットによる手入力、ハンディターミナルによるバーコード読み取り
データ収集の対象:作業実績、品質データ、材料・部品の投入履歴、生産指示情報との紐付け、作業者関連情報
電子部品メーカー様では、紙ベースで運用されていた作業日報やピッキングリストの管理に多くの手間がかかり、記録ミスや情報反映の遅れが課題となっていました。Smart Craftの導入後、作業実績はタブレット入力で記録し、部品ピッキングにはハンディターミナルを活用したバーコード読み取りを導入。これにより、記録の正確性と反映スピードが向上し、完全ペーパーレスな運用を実現しました。情報の一元化と標準化が進んだことで、現場の工数は全体で約10%削減。製造管理基盤の整備が、生産性向上に直結する結果となりました。
事例2:人と設備の実績データを統合し、ライン稼働率を改善
データ収集の手段:タブレットによる手入力、PLCによる設備データ収集
データ収集の対象:作業実績、設備稼働情報、材料・部品の投入履歴、生産指示情報との紐付け、作業者関連情報
Tier1自動車部品メーカーでは、加工ラインの生産性向上を目指し、作業実績と設備稼働データを一元的に把握する仕組みを構築しました。Smart Craft導入により、人が関与する工程はタブレットで手入力、設備はPLCから稼働・停止情報を自動収集し、両者をSmart Craft上で統合。これまで個別管理されていた実績をまとめて分析できるようになったことで、トラブル時の全体把握と迅速対応が可能になり、ライン稼働率の向上を実現しました。また、リアルタイムな情報共有による現場判断のスピードアップも成果の一つです。
事例3:紙と属人化を脱し、改善スピードを加速
データ収集の手段:タブレットによる手入力
データ収集の対象:作業実績、設備稼働情報、材料・部品の投入履歴、生産指示情報との紐付け、作業者関連情報
Tier1の自動車部品メーカーでは、紙による記録と属人化した運用により、実績の正確な把握が難しく、改善の遅れが課題となっていました。Smart Craftの導入後は、現場でのタブレット入力により、作業実績や設備稼働状況がリアルタイムかつ高精度に把握できるようになりました。これにより、従来は把握が難しかった工程進捗が可視化され、工程負荷の分析や平準化の取り組みが加速。作業者の改善意識も高まり、自律的に工夫する文化が根づき始めています。さらに、紙の日報も廃止され、生産性が着実に向上しています。
まとめ:MES導入の最初の一歩は「データ収集」から
MESは多機能なシステムですが、すべてを一度に導入するのは現実的ではありません。その中で「データ収集」は、小さく始めて、大きな効果を得やすい領域です。
まずは、簡単な手段で実績を記録する仕組みを構築し、現場の見える化を実現する。そこから可視化・分析・改善へとつなげていくことで、MESの効果を着実に実感できるはずです。
製造DXの第一歩として、「データ収集」にフォーカスするアプローチは、多くの現場にとって現実的で、効果的な導入戦略となるでしょう。
製造現場のデジタル化を支援する「Smart Craft」のご紹介
製造現場のデジタル化は、製造現場の課題を可視化し、生産性向上のみならず、稼ぐ力の向上に寄与します。効率的な製造現場の実績収集に向けては、各種ソリューションが多くの企業で活用されています。
その中でもSmart Craftは、国産初のSaaS型MESであり、クラウドベースであるため、導入の際には初期費用を抑えることができ、段階的なシステム導入も可能です。
実績データ収集だけでなく、ダッシュボード機能により可視化や分析が簡単にでき、製造現場の改善を加速します。まずは資料請求からSmart Craftの導入を検討してみてください。
