2024年版ものづくり白書から読み解く製造現場DX成功への鍵とは? ~340ページの白書から最重要ポイントを要約~
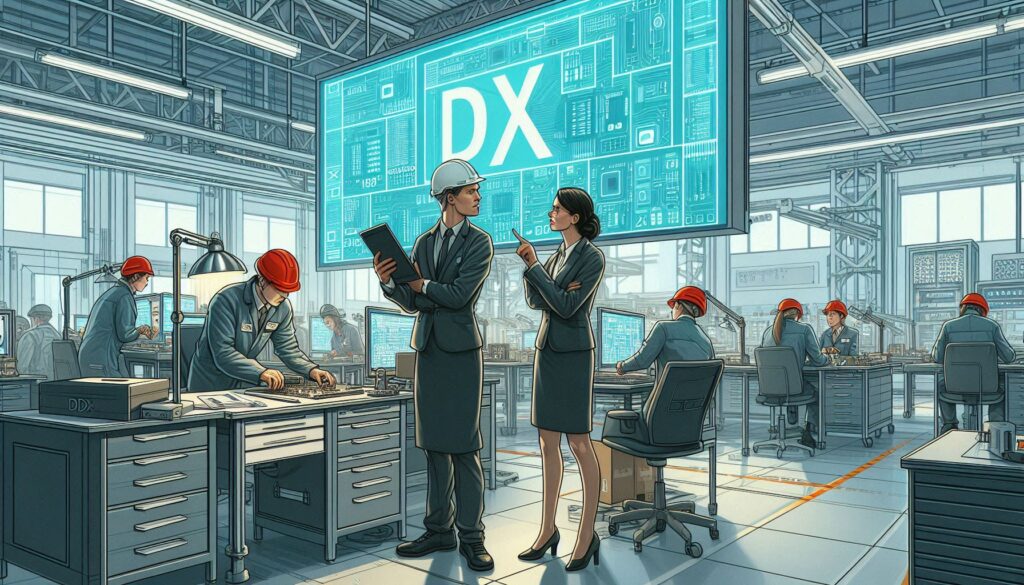
製造業またはその関連業務に従事する方であれば、「ものづくり白書」という言葉を一度は耳にしたことがあるでしょう。
「ものづくり白書」は、経済産業省・厚生労働省・文部科学省の3省が共同で作成し、国会に報告される法定白書です。その内容は、ものづくりに関する基礎データ、日本の製造業が直面する課題、政府の取り組みなどが含まれ、日本の製造業に携わる人にとって必読の文献と言えるでしょう。
しかし、2024年版ものづくり白書は340ページにも及ぶため、すべてを読むのは容易ではありませんし、自社や担当業務に関する箇所を探すだけでも多大な手間がかかります。
本記事では、膨大な文献の中から「製造現場DX」に焦点を当て、調査データ・課題・事例などを抜粋・要約しており、ものづくり白書をじっくり読む時間がない方でも重要なポイントを把握できる内容になっています。本記事を通じ、製造現場DXの要点を理解する一助となれば幸いです。
なお、本記事で出典が特に記されていないものは「2024年版ものづくり白書」に基づいています。記事内の画像についても、「2024年版ものづくり白書」の調査データを本記事に適した形にして掲載しています。
目次
ものづくり白書とは
ものづくり白書は、「ものづくり基盤技術振興基本法」第8条に基づく法定白書で、政府が毎年国会に報告する年次報告書です。経済産業省・厚生労働省・文部科学省の3省が共同で作成し、今回の2024年版で24回目となります。
この白書の主な目的は、ものづくり基盤技術の振興に関して政府が講じた施策を国会に報告することです。内容は2部構成で、第1部は「ものづくり基盤技術の現状と課題」の見出しのとおり、ものづくりに関する基礎的なデータや、それらデータも踏まえた上での課題、政府の取り組みを掲載しています。第2部は「令和5年度においてものづくり基盤技術の振興に関して講じた施策」という見出しのとおり、政府が実施したものづくり関連の施策を詳細に報告しています。
第1部は更に5章に分かれており、経済産業省が製造業の業況や企業の投資動向や製造業を取り巻く環境の変化、厚生労働省がものづくり人材を巡る動向、文部科学省が教育・研究開発に関する内容を担当しています。第2部も同様に5章立てで、具体的な施策や取り組み事例、政府がものづくり産業の振興のために行っている取り組みが記載されています。
白書は製造業の現状分析や課題提示、政府の施策紹介だけでなく、企業へのアンケート結果なども含まれており、ものづくり産業の包括的な状況を把握することができます。また、毎年のテーマに沿って、製造業の「稼ぐ力」向上のための方策なども提言されています。
以上の案内からも、ものづくり白書は日本の製造業に携わる人にとって非常に価値のある文献と言えるでしょう。
次章からは、2024年版ものづくり白書に基づき、「製造現場の担当者視点」での「製造現場のDX」について考察と解説をしていきます。なお、本記事で「ものづくり白書」とあるものは「2024年版ものづくり白書」を指しています。
製造現場DXは進んでいない
経済産業省「デジタル化の取組領域別推進状況」に関する調査データ(図1)によると、「個別工程のカイゼン」の実施は半数以下、「製造機能の全体最適」はおよそ4社に1社となっています。
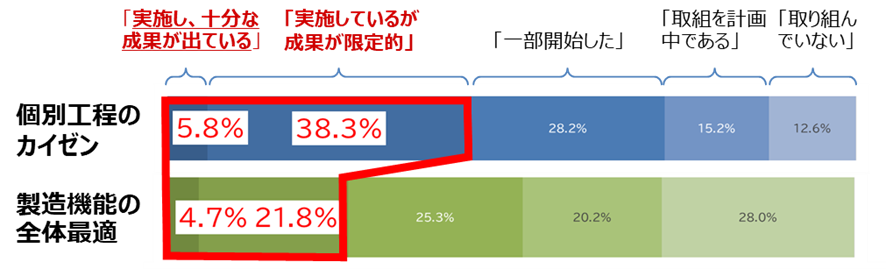
製造業企業にも多様な部門が存在しますが、例えば本社部門でDXの取り組みが50%を下回ることは考えにくく、製造現場はDXが進んでいないと言えます。
その背景として、製造業の製造品目や工程が企業ごとに多様で、他部門に比べDXが容易ではないということが挙げられるでしょう。しかし、紙やホワイトボードを用いたアナログ管理や勘・コツ・経験に頼った属人的業務を続けていては付加価値の向上は見込めず、競争力の低下や売上の減少に繋がりかねません。
では、どのようにすれば、製造現場DXを推進できるのでしょうか。次章以降では、ものづくり白書の調査データを深掘りし、製造現場DXの課題を明らかにするとともに、解決策や事例を紹介していきます。
弊社では製造現場DX推進に特化したSaaS型のMES(Manufacturing Execution System、製造実行システム)「Smart Craft」を提供しています。製造現場の工程管理、品質管理、集計・分析をまとめてデジタル化し、ペーパレス化による生産性改善を実現します。詳しくは資料で紹介しています。⇒資料のダウンロードはこちら
課題1: DXの目的が限定的
「DXの取組目的及び成果」に関する調査データ(図2)によると、目的別では、「業務効率化・生産性向上」が69.6%と最も高い一方で、「新商品・サービス・事業の開発」は19.4%、「既存の商品・サービス・事業の高付加価値化」は19.2%と低くなっています。
成果別では、「コストの削減」が49.1%である一方で、「売上の向上」は21.3%、「新規事業への展開・新規顧客の開拓」は12.5%と低くなっています。
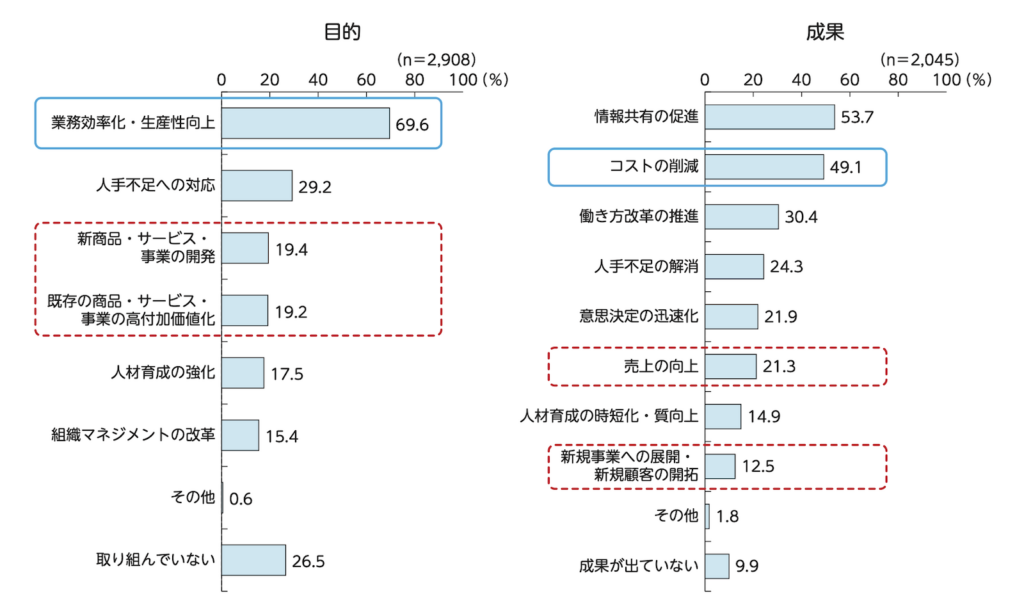
この調査データから、DXの目的がコスト削減など限定的なものにとどまり、「稼ぐ力の強化」にまで至っていないことがうかがえます。特に製造現場では、DXを通じて業務効率化という成果を出しやすい傾向にあり、読者の皆さまにおかれても、業務効率化を中心とした取り組みを進めている場合が多いかもしれません。しかし、DXはそれだけにとどまるべきではありません。売上向上や新規事業展開といった中長期的な成長を見据えた推進が重要です。
参考: 「稼ぐ力」の強化に向けたコーポレートガバナンス研究会(経済産業省)
https://www.meti.go.jp/shingikai/economy/earning_power/index.html
事例: 土屋合成
DX推進にあたって経営層がコミット、うまくくいかない場合も責任を押し付けずに積極的にアイデアを発信できる風土を醸成。また投資の目的を単なるQCD向上にとどめず、従業員が便利さや楽しさを享受できる環境づくりに注力し、そこから生まれる従業員同士や顧客とのコミュニケーション強化が付加価値の源泉となっている。収益は再投資に加え、従業員への還元によって好循環を生んでいる。
事例: 中村留精密工業
社員の力を結集して最大化するためには情報共有が特に重要と考え、情報共有ツールの自社開発と活用に注力。月次決算などの経営情報の公開や、さまざまな業務の見える化にも取り組み、社員のやる気とアイデアを引き出している。IT・デジタル技術はあくまでも手段に過ぎず、「人の行動や意識をどう変えるか?」というアウトカム(成果)に重点を置いている。
課題2: スマートマニュファクチャリングができていない
前章で稼ぐ力の強化にはコスト削減だけでなく売上向上も重要であることが明らかになりましたが、日本の製造事業者が得意としている現場起点の改善だけで売上向上を達成することは難しいと考えられます。
「DXの取組領域別推進状況」に関する調査データ(図3)によると、領域別では「個別工程のカイゼン」が44.1%と最も多く、個社最適化を目指す「製造機能の全体最適」は25.6%、新たな製品・サービスの創出により新市場を獲得する「事業機会の拡大」は19.1%と更に少ないのが実情となっています。
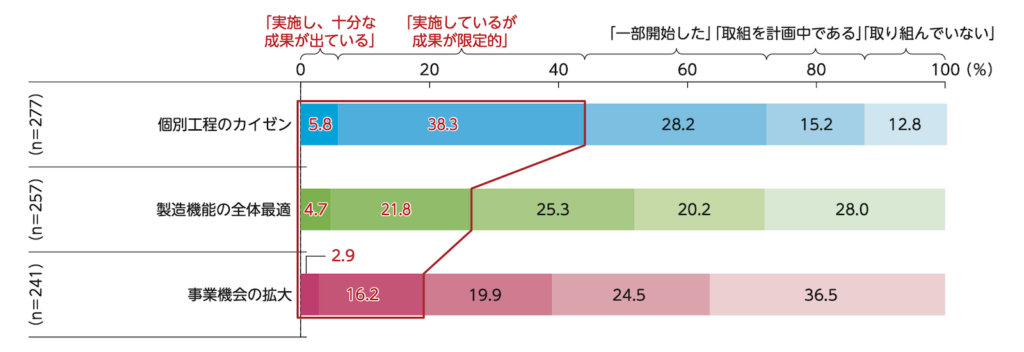
製造現場DXにおいては、自社内のマニュファクチャリングに関するチェーン・プロセス単位といった個別工程の最適化にとどまってしまうケースが少なくないですが、チェーン・プロセス間の連携強化による個社最適化を目指し、多種多量のデータを迅速に正しく容易に連鎖させる取り組みが求められます。
つまり、IT・デジタル技術を活用する「スマートマニュファクチャリング」の推進が重要になります。
スマートマニュファクチャリングとは
「スマートマニュファクチャリング構築ガイドライン」によると、スマートマニュファクチャリングは以下のように定義されています。
データとデジタル技術を活用して、自社内のマニュファクチャリングに関する各チェーンを横断して最適化を図ること。すなわち、デジタル技術を媒介としたデータを活用し、マニュファクチャリングチェーンの様々な意思決定と制御を加速させる取組み
本記事にあわせて簡潔に表現すると「デジタル技術を活用し、部分最適ではなく、全体最適を目的としたDX」と捉えることができます。個別の工程や部門でのDXは進みつつあるものの、全社的な取り組みには至っていないため、個社最適化を推進すること、つまり「スマートマニュファクチャリング」が重要となります。
参考: スマートマニュファクチャリング構築ガイドライン(国立研究開発法人新エネルギー・産業技術総合開発機構)
https://www.nedo.go.jp/library/smart_manufacturing_guideline.html
一方、製造現場の責任は製品のQCDをコントロールしながら製造することであり、会社全体の方向性を決めるといった経営視点での判断は求められていません。しかし、経営者も製造現場の詳細をすべて把握しているわけではないため、製造現場の担当者も個別工程の最適化に加え、個社最適化につながるかを意識する必要があると考えます。
また、個社最適化を進めるための経営判断にはデータが必要不可欠です。したがって製造現場の担当者は、経営陣が迅速かつ詳細なデータにアクセスできるよう準備しておくことが重要です。
事例: ブリジストン
航空機、鉱山車両用タイヤにおいて、車両とタイヤのデータを基にAI活用など独自のアルゴリズムで高精度なタイヤ摩耗予測を実現している。これにより、タイヤをより安全に、長く、上手く、効率的に使用するためのソリューションを提供している。顧客のオペレーションにおける生産性・経済価値の最大化及びサステナビリティへ貢献し、タイヤを「創って・売る」だけでなく、「使う」全体で、社会価値・顧客価値の創造を進めている。
課題3: リソース不足
前々章に紹介した「DXの取組目的及び成果」に関する調査で「取り組んでいない」と回答した事業者を対象とした「DXに取り組んでいない又は成果が出ていない理由」の調査データ(図4)によると、「DXに取り組むためのリソースが不足している」が68.3%と最多であり、次いで「DXに取り組むための情報が不足している」が44.0%と多くなっています。
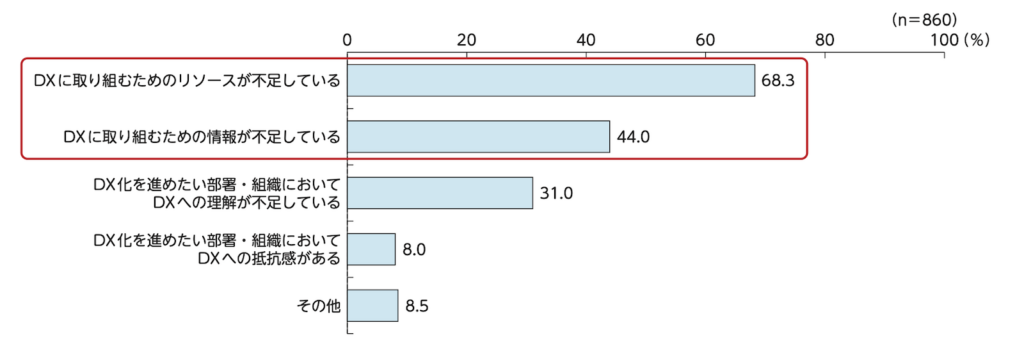
リソース不足
一般的に「リソース」には、ヒト・モノ・カネ・時間・情報、などが含まれますが、中長期的な観点ではヒト、つまりDX人材の不足が課題として挙げられるでしょう。しかし昨今はDX人材の獲得難易度は非常に高く、自社人材の育成こそが喫緊の課題といえます。
情報不足
「組織・部門間におけるコミュニケーションの実態」に関する調査データ(図5)によると、「連携ができている/壁がない」は34.4%であることから、それ以外の65.6%は何らかの壁があると感じていることになります。
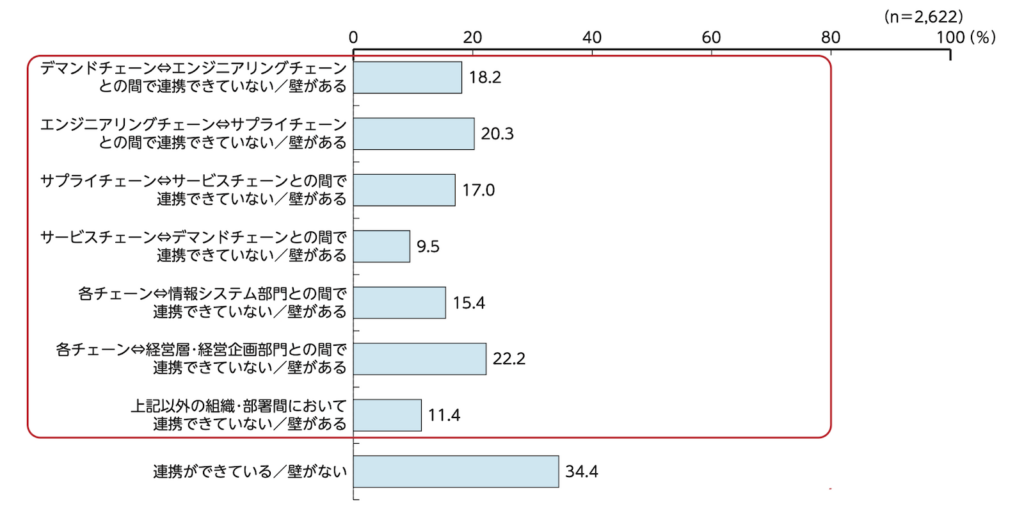
そして「壁がない」に関する追加調査「組織・部門間において「連携ができている/壁がない」と感じている理由」(図6)によれば、「対面でのコミュニケーションにより情報共有が図られている」が71.3%、「デジタル技術の活用により情報共有が図られている」は24.5%となっており、部門間の情報連携に「壁がない」場合でも、デジタル技術の活用は進んでいないことがわかります。
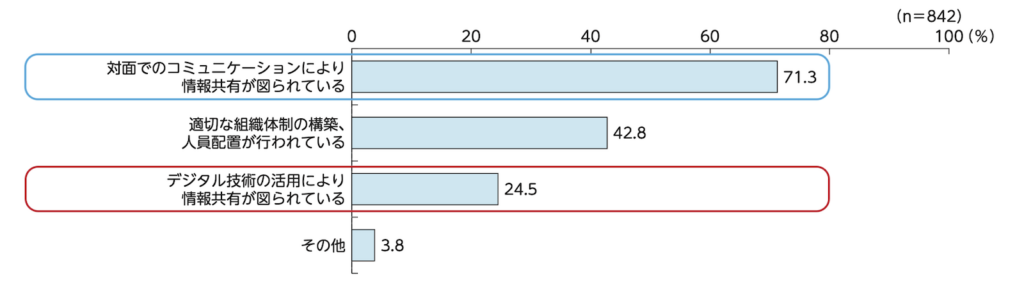
情報不足に対してもデジタル技術の活用が有効であることは疑いようがありませんので、やはりDX人材の獲得が必要不可欠となります。
そして、製造現場の担当者が意識すべきは、現場の詳細な情報にアクセスできる環境を構築することです。DX人材の獲得や育成は経営課題ですが、その経営判断には現場の情報が欠かせないからです。
製造現場のDX人材育成には以下の2点が重要です。
- 製造現場を深く理解し、製造現場の詳細情報にアクセスできる環境を構築できる
- 他部門と連携し、部門間で情報共有できる仕組みを構築する
図7は部門間連携における業務システム間のデータ連携のイメージですが、赤枠部分が製造現場の担当者が責任を持つ領域となります。

個社最適化には、各マニュファクチャリングチェーンでの迅速かつ正確な情報共有が求められるため、業務システム間のデータ連携が不可欠です。特に製造現場には膨大な情報がありますので、すべてをデジタル化するのではなく、効率的なデジタル化を進めることがポイントになります。
事例: ダイキン工業
顧客ごとに異なるニーズに応えるため、エネルギーマネジメントや設備監視といった単なる機器販売にとどまらず、データ活用を通じた価値提供が欠かせない。社内にソフトウェア開発者は一定数いたが、さらにビジネス企画できる人材や、データ活用で課題解決できる人材はほぼ皆無であった。このような高度IT人材を採用することは難しく、その危機感から自社内で人材育成に取り組むことを経営層のトップダウンで決定、社内講座「ダイキン情報技術大学」を開講し、選抜社員がデジタル技術とデータ活用スキルを徹底的に学べる場を提供している。
課題4: 製造ソリューションの活用が進んでいない
課題1の考察にあるとおり、日本の製造事業者のDXの目的としては業務効率化・生産性向上が多いが、稼ぐ力の強化に向けては、売上の向上や新規事業への展開及び新規顧客の開拓につながるような、新商品・サービス・事業の開発も重要になります。そのためには、製造現場DXが必要不可欠になります。
しかし、「製造ソリューションの活用状況」に関する調査データ(図8・図9)によると、主要ソフトウェアの活用率は、大企業では「ERP」は71.2%、「MOM(MES)」は56.1%と半数を超えていますが、中小企業では「ERP」ですら48.1%と半数に満たず、さらに「MOM(MES)」は21.4%と活用率が低く、製造現場でのソリューション活用が進んでいないことがわかります。
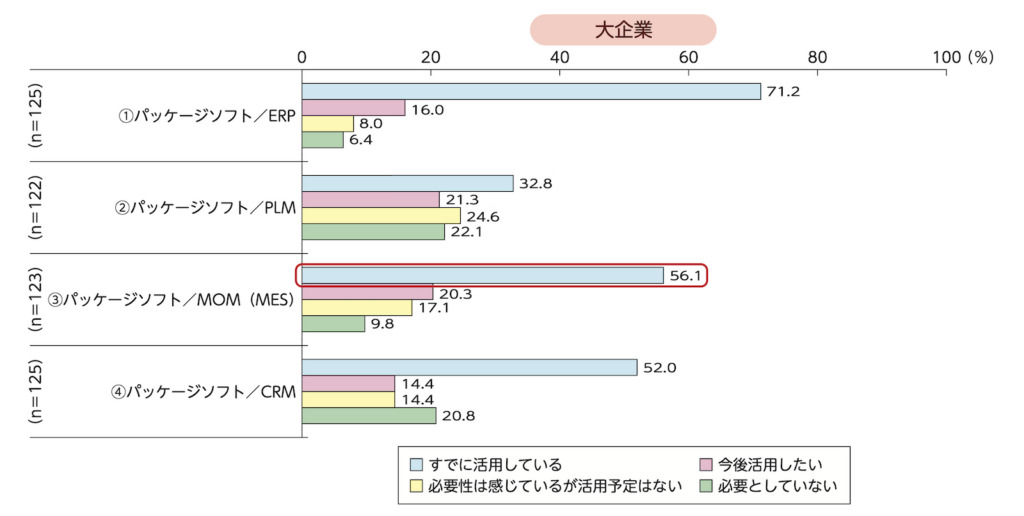
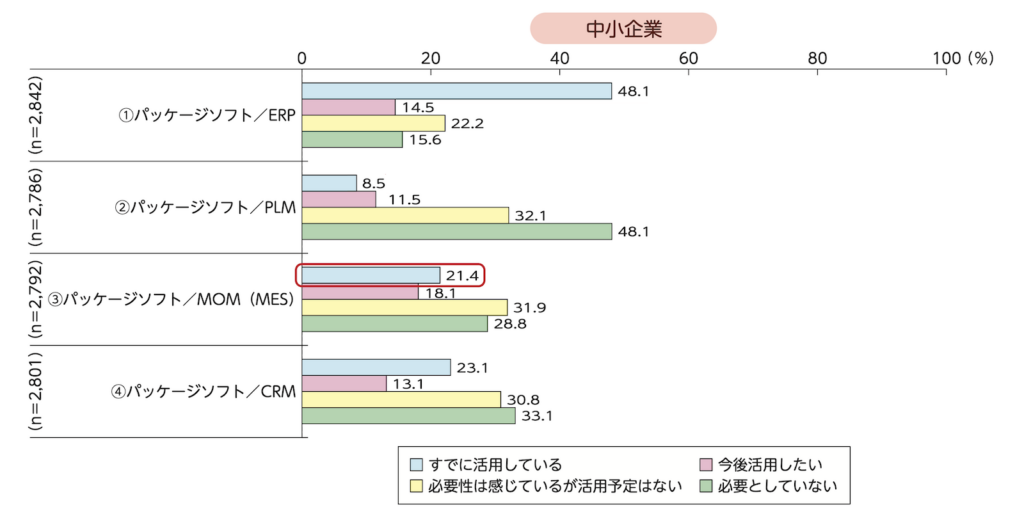
大企業でのMES活用率が56.1%と比較的高い理由は、MESの活用が稼ぐ力の強化に直結しているためと考えられます。よって、中小企業においてもMESを活用した製造現場DXの推進が稼ぐ力の強化につながるでしょう。さらに、中小企業でのMES活用率は約20%、つまり5社に1社の割合にとどまっていることは、MESの活用による製造の効率化だけでなく、顧客に対する大きな差別化要因にもなります。
製造現場DXは、単なる現場のデジタル化にとどまるものではありません。その先には、自社の製造プロセスをデジタル化し、様々な機器・ソフトウェア・サービスへと展開することで、新たな事業機会を創出する可能性が広がっています。個社最適化を実現するためにも、MESの活用は欠かせないものと言えるでしょう。
事例: 三浦工業
予防保全を最重要視する考えのもと、業界で初めてサブスクリプション型有償保守契約を導入するなどメンテナンス事業に力を入れている。また、IoT導入のパイオニアでもあり、業界に先駆けてリモートセンシングによるオンラインメンテナンスを開始、顧客設備を24時間365日監視し、データに基づく保守管理を実現させた。さらに、他社製品を含むさまざまなユーティリティ設備の稼動データを自社で一元的に管理できるプラットフォームを提供することで、顧客に大きな付加価値をもたらしている。
製造現場DXに向けて
前章まで4つの課題に言及してきました。本章では、その課題を踏まえた上で、製造現場DXを推進するための解決策としてものづくり白書に掲載されている情報を紹介していきます。
スマート工場実現のためのMES機能標準化活動
海外のスマート工場では、MESの導入が前提となるケースが多い一方で、日本ではMES導入があまり進んでいないのが現状です。その主な理由として、日本の製造現場に適したMES導入を検討する際の標準的な方法やノウハウが未確立であり、専門知識を持つ知見者や有識者が限られていることが挙げられます。
1990年代に米国のMESA Internationalが制定した「MESの標準11機能」は、これまで頻繁に参照されてきました。しかし、これはMESをERPの補完システムとして捉えた管理カテゴリを前提としており、日本の製造現場でなじみのある業務分担とは一部で乖離があります。
この課題を解決するため、本プロジェクトでは工場業務を典型的な12の主要業務に分類し、標準的なモデルを定義しました。このモデルは、MES導入構想の策定や提案依頼書(RFP)における記載方法の指針としてまとめられています。この標準モデルの普及により、日本におけるMES導入の加速とスマート工場化のさらなる促進が期待されています。
本プロジェクトの特徴は、内資・外資・スタートアップを含む民間企業で働くMES技術者の有志による標準化活動である点です。また、弊社Smart Craftも本プロジェクトの一員として参加しており、成果物の提供も可能です。詳細についてはお気軽にお問い合わせください。⇒お問い合わせ
国産初のSaaS型MESで製造現場DXのスモールスタートを実現
これまで、製造現場の工程全体を一元的にデジタル化するには、「MES」と呼ばれる高額なシステムの導入が必要であり、さらにその導入には長い時間がかかるのが一般的でした。この課題を解決すべく、汎用的な機能を持たせ、従来のオンプレミス型ではなくSaaS型として開発・提供することで、短期間での導入を可能にしたのが「Smart Craft」です。
クラウドベースでの提供のため、製造現場の情報をリアルタイムで可視化し、生産進捗や実績の管理を容易にします。タブレットやスマートフォンを活用した直感的な操作性とともに、生産計画の作成や変更、生産記録や工数の正確な測定、進捗管理、品質管理、さらにはロットトレースまで、幅広い機能を提供しています。
さらに、API連携により生産管理システムをはじめとする他のシステムとのデータ同期が可能となり、リアルタイムでの情報共有や製造現場のモニタリングを実現します。
まとめ
ここまでものづくり白書の調査データを基に、製造現場DXを推進する際の課題、解決策、事例を紹介してきました。製造現場の視点からシンプルに要点をまとめると、以下の3つに集約されます。
- 製造現場DXの目的を「稼ぐ力の強化」とし、経営と現場が一体となって推進する
- 個社最適化である「スマートマニュファクチャリング」を目的として製造現場DXに投資する (DX人材育成も含む)
- 得られた成果を基にさらなる再投資や従業員への還元を行い、稼ぐ力をより一層強化する
本記事で紹介した事例の多くは大企業や業界トップの優良企業の取り組みで、自社では難しいと感じたかもしれません。しかし、これらの企業も最初から成功が見えていたわけではなく、経営と現場が一体となって地道に取り組みを積み上げた結果であると考えられます。
もちろん、投資が失敗するリスクもありますが、失敗は次の成功への土台です。目的を見失わず、経営と現場が一体となって成功を目指して推進し続けることが何よりも重要です。
本記事がみなさまの製造現場DX推進の一助となれば幸いです。
なお、本記事で紹介した事例については、さらに詳しい内容がものづくり白書にございますのでぜひ参考にしてください。
https://www.meti.go.jp/report/whitepaper/mono/2024/index.html
製造現場DXを支援する「Smart Craft」のご紹介
製造現場DXは、製造現場の課題を可視化し、生産性向上のみならず、稼ぐ力の向上にに寄与します。効率的な製造現場の実績収集に向けては、各種ソリューションが多くの企業で活用されています。
その中でも、Smart Craftは、製造現場DX推進に特化した国産初のSaaS型MESであり、クラウドベースであるため、導入の際には初期費用を抑えることができ、段階的なシステム導入も可能です。製造現場の工程管理、品質管理、集計・分析をまとめてデジタル化し、ペーパレス化による生産性改善を実現します。詳しくは資料で紹介しています。
タブレットやスマホで直感的に操作が可能なため、ITが苦手という従業員でも容易に使用できます。まずは資料請求からSmart Craftの導入を検討してみてください。

直感的なインターフェースにより、デジタルスキルの高くない従業員でも容易に使用できるため、人材育成の課題解決にも貢献します。まずはお気軽に資料請求ください。
Smart Craftで製造現場のDXを
始めよう!
「Smart Craft」は、これひとつで工場内のすべての業務プロセスをデジタル化できます。
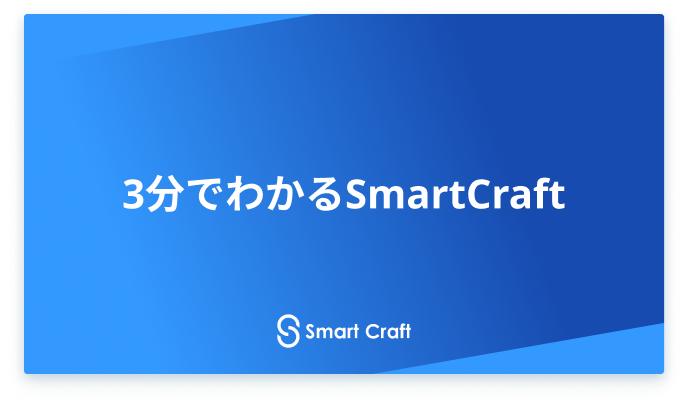
- Smart Craft でできること
- 導入企業の活用事例
- ご利用料金
- 導入の流れ