スマートファクトリーとは? 導入メリットから実践手順、成功事例まで徹底解説
製造業は今、大きな転換点を迎えています。少子高齢化に伴う深刻な人手不足、グローバル競争の激化、顧客ニーズの多様化、そして環境負荷低減への要求など、様々な課題に直面しています。これらの課題に対応しつつ、競争力を維持・向上させるためには、従来の製造方法からの脱却が不可欠です。
そこで注目を集めているのが「スマートファクトリー」です。IoT(Internet of Things)、AI(人工知能)、ビッグデータ分析などの先端技術を活用し、工場全体をデジタル化・ネットワーク化することで、生産性の飛躍的な向上を実現する次世代の工場のことです。
この記事では、スマートファクトリーの概念や特徴、導入のメリットと課題、実践的な構築手順、さらには具体的な成功事例まで、幅広く解説します。製造業に携わる方々が、自社の競争力強化と持続可能な成長を実現するための指針となれば幸いです。
また、弊社では製造現場のDX推進に特化したクラウドサービス「Smart Craft」を提供しています。製造現場の工程管理、品質管理、集計・分析をまとめてデジタル化し、ペーパレス化による生産性改善を実現します。詳しくは資料で紹介しています。⇒資料のダウンロードはこちら
目次
スマートファクトリーとは
スマートファクトリーとは、AIやIoTなど最新のデジタル技術を活用して、工場内の設備や生産ラインをネットワークで接続し、生産性の向上や品質の改善を図る次世代の工場のことを指します。単なる自動化や効率化にとどまらず、工場全体をデジタル空間上で再現し、リアルタイムでの監視・制御・最適化を可能にする点が特徴です。
従来の工場との違い
スマートファクトリーは、従来の工場と比較して、いくつかの重要な点で大きく異なります。
まず、データの管理方法が変わります。従来の個別管理から、工場全体のデータをリアルタイムで収集し一元管理する方式へと進化しました。これにより、生産ライン、設備稼働、品質などの情報を統合的に把握し、迅速な意思決定が可能になります。
次に、生産体制の柔軟性が向上します。固定的な生産ラインから、需要変化に応じて迅速に調整可能なシステムへと変わり、多品種少量生産にも対応できるようになりました。設備保全も、定期的なメンテナンスから、常時モニタリングによる予知保全へと進化しています。これにより、不要なメンテナンスを減らし、突発的な設備停止を防ぐことができます。
これらの特徴により、スマートファクトリーは従来の工場と比べて、より効率的で柔軟、そして予測可能な生産システムを実現しています。
インダストリー4.0とスマートファクトリーの関係
インダストリー4.0は、2011年にドイツが提唱した製造業の未来像を示す概念で、第4次産業革命とも呼ばれます。スマートファクトリーは、このインダストリー4.0の理念を具現化した工場の形態です。
インダストリー4.0の核心は、物理的な製造プロセスとデジタル技術の融合にあります。スマートファクトリーでは、この理念に基づき、IoTを活用して工場内のあらゆる設備や工程をネットワークで接続し、データを収集・分析します。これにより、以下のような取り組みが可能になります。
- 生産設備のネットワーク化と相互連携
- 生産状況のリアルタイムモニタリング
- 設備の予知保全
- 需要変化に応じた柔軟な生産体制
- サプライチェーンの最適化
これらの取り組みは、インダストリー4.0が目指す「スマートな製造」の具体的な実践例です。スマートファクトリーは、データとデジタル技術を活用して生産性向上、品質改善、コスト削減を実現し、製造業の競争力強化に貢献します。
日本でも、経済産業省が「コネクテッドインダストリーズ」を提唱し、多くの企業がスマートファクトリー化を進めています。スマートファクトリーは、インダストリー4.0を製造現場で実現する手段として、今後ますます重要性を増していくでしょう。
<出典:経済産業省>
また、弊社では製造現場のDX推進に特化したクラウドサービス「Smart Craft」(スマートクラフト)を提供しています。製造現場の工程管理、品質管理、集計・分析をまとめてデジタル化し、ペーパレス化による生産性改善を実現します。詳しくは資料で紹介しています。
Smart Craftで製造現場のDXを
始めよう!
「Smart Craft」は、これひとつで工場内のすべての業務プロセスをデジタル化できます。
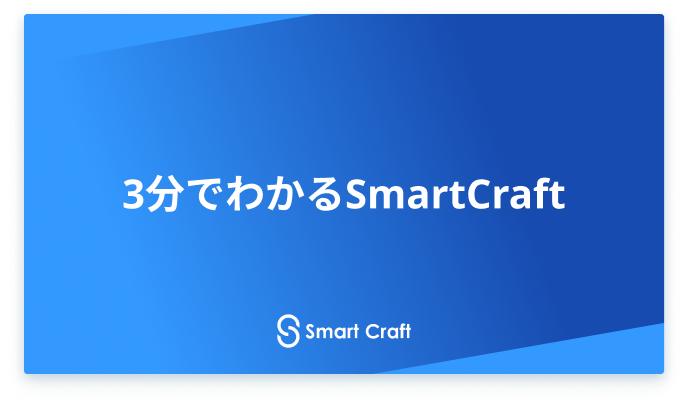
- Smart Craft でできること
- 導入企業の活用事例
- ご利用料金
- 導入の流れ
スマートファクトリーのメリット
スマートファクトリーの導入には様々なメリットがあります。主なものを以下に挙げます。
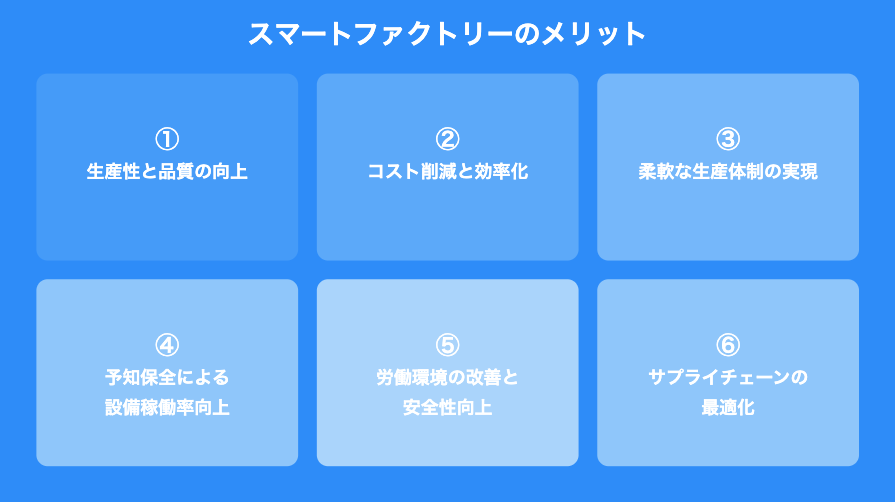
①生産性と品質の向上
データの一元管理とリアルタイム分析により、生産プロセスを常に最適化できます。センサーから収集された大量のデータを分析することで、生産ラインの微調整がリアルタイムで可能となり、生産効率が大幅に向上します。
同時に、品質管理においても、データ駆動型の分析により、不良品の早期発見や製造条件の最適化が実現し、品質の安定化と向上につながります。例えば、製造パラメータのわずかな変動が製品品質に与える影響を即座に検出し、自動的に調整することで、不良率を大幅に低減できます。
②コスト削減と効率化
設備稼働率の向上、エネルギー使用の最適化、在庫管理の効率化などにより、全体的なコスト削減が可能になります。例えば、設備の稼働状況をリアルタイムでモニタリングし、遊休時間を最小限に抑えることで、生産能力を最大限に活用できます。
また、エネルギー使用量のデータ分析により、ピーク時の電力使用を分散させたり、無駄な電力消費を削減したりすることが可能です。在庫管理においては、需要予測の精度向上により適正在庫を維持し、過剰在庫や欠品によるコストを削減できます。これらの総合的な効果により、製造コストの大幅な削減が実現します。
③柔軟な生産体制の実現
需要変動に迅速に対応できる生産システムにより、多品種少量生産や短納期対応が可能になります。また、新製品の生産ラインへの導入も迅速化されます。従来の固定的な生産ラインと異なり、スマートファクトリーでは生産設備のネットワーク化により、製品の切り替えや生産量の調整をシステム上で簡単に行えます。
これにより、市場ニーズの変化に迅速に対応し、顧客の要求に柔軟に応えることができます。さらに、シミュレーション技術を活用することで、新製品の生産ライン構築を仮想空間で検証し、実際の導入時間を大幅に短縮することも可能です。
④予知保全による設備稼働率の向上
設備の状態を常時監視することで、故障を事前に予測し、計画的なメンテナンスが可能になります。これにより、突発的な設備停止を減少させ、稼働率を向上させることができます。従来の定期メンテナンスに比べ、各設備の実際の使用状況や劣化状態に基づいた最適なタイミングでのメンテナンスが可能となり、不要なメンテナンスコストを削減しつつ、設備の寿命を延ばすことができます。
また、故障の予兆を早期に検知することで、大規模な故障を未然に防ぎ、修理コストの削減と生産ラインの安定稼働を実現します。
⑤労働環境の改善と安全性の向上
危険作業の自動化や作業負荷の最適化により、作業者の安全性が向上します。また、データ活用により、熟練技能のデジタル化と効果的な技術伝承が可能になります。例えば、重労働や危険を伴う作業をロボットに任せることで、作業者の負担を軽減し、労働災害のリスクを大幅に低減できます。
さらに、ウェアラブルデバイスなどを活用して作業者の動作や疲労度をモニタリングし、最適な作業配分を行うことで、作業効率の向上と同時に労働環境の改善が図れます。熟練技能者の作業をデータ化し、AIによる解析をすることで、暗黙知を形式知化し、若手作業者への効果的な技能伝承も可能になります。
⑥サプライチェーンの最適化
取引先とのリアルタイムな情報共有により、在庫の適正化、納期の短縮、トレーサビリティの向上が図れます。例えば、原材料の調達から製品の出荷まで、サプライチェーン全体をデジタル化することで、需要予測の精度向上、リードタイムの短縮、在庫の最適化が可能になります。
また、ブロックチェーン技術などを活用することで、製品の製造履歴を詳細に記録し、万が一の品質問題発生時にも迅速な原因特定と対応が可能になります。これにより、顧客満足度の向上と同時に、リコールなどのリスク低減にもつながります。
スマートファクトリーの課題
スマートファクトリー化の必要性は広く認識されているものの、その実現と普及には依然として多くの障壁が存在します。製造業が直面する主な課題は以下の通りです。
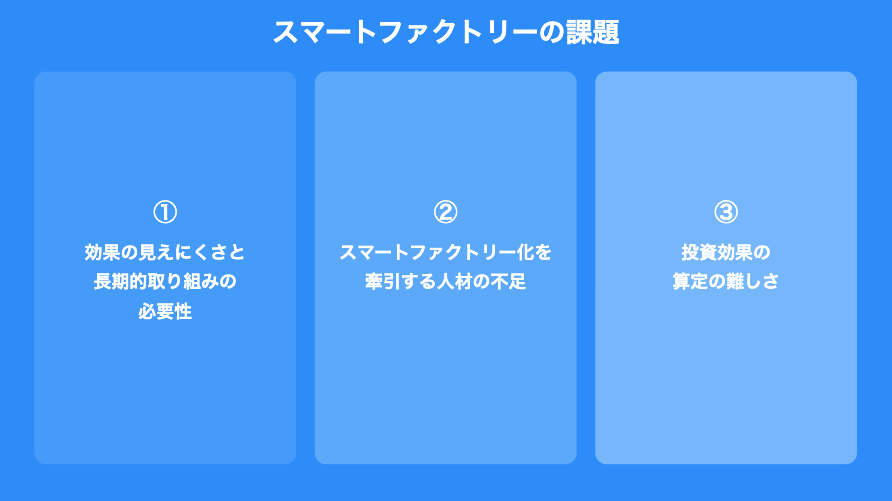
効果の見えにくさと長期的取り組みの必要性
スマートファクトリー化は、作業員の負荷軽減や生産体制の安定化など、多くの利点をもたらす可能性があります。しかし、その効果が即座に目に見える形で現れないことが大きな課題となっています。「デジタル技術導入の効果がわからない」という声が多く聞かれる背景には、この効果の見えにくさがあります。
多くの企業が「原材料費や経費の増大」「価格競争の激化」といった喫緊の経営課題に直面しており、長期的な視点で取り組むべきスマートファクトリー化に十分なリソースを割くことが困難な状況にあります。IoTはスマートファクトリー化を実現する「手段」であって「目的」ではありません。データの収集から分析、改善策の実施、成果の検証まで、一連のプロセスには一定の時間が必要です。
この課題に対処するためには、明確な目的設定と段階的なアプローチが効果的です。小規模なパイロットプロジェクトから始め、効果を検証しながら徐々に規模を拡大していくことで、投資リスクを抑えつつ、具体的な成果を示すことができます。
経営層には長期的な競争力強化のための投資として捉える視点が、現場レベルではデジタル技術導入の具体的なイメージを持てるよう継続的な教育が必要です。このように、効果の見えにくさと長期的取り組みの必要性は大きな課題ですが、適切な戦略と粘り強い取り組みによって克服することが可能です。
スマートファクトリー化を牽引する人材の不足
デジタル技術導入に必要なノウハウと、その活用を先導できる人材の不足は、製造業にとって大きな課題となっています。スマートファクトリー化の推進には、製造技術と情報技術の両方を理解し、さらに組織横断的なリーダーシップを発揮できる人材が求められます。
しかし、このような人材の育成には時間がかかり、即効性のある解決策とはなりにくいのが現状です。
この課題に対しては、外部の専門家やITベンダーのサポートを活用しながら、社内人材の段階的な育成を進めることが有効です。また、製造現場とIT部門の連携を強化し、相互理解を深めることで、組織全体のデジタルリテラシー向上を図ることも重要です。
投資効果の算定の難しさ
スマートファクトリー化には多額の投資が必要となる一方で、その効果を正確に算定することが困難です。工場内の様々なシステムや設備の見直し、継続的なメンテナンス、セキュリティ対策など、幅広い投資が必要となります。
投資効果を測る指標が不明確なまま推進すると、予想以上のコストが発生し、予算を圧迫するリスクがあります。これがスマートファクトリー化の進展を妨げる要因の一つとなっています。
この課題に対しては、投資効果を測定するKPIを事前に明確に設定し、段階的な導入と効果検証を繰り返すことが重要です。また、業界団体や政府機関が提供する支援制度や成功事例を参考にすることで、より正確な投資計画を立てることができます。
これらの課題を克服するためには、経営層の強いコミットメントと、全社的な取り組みが不可欠です。スマートファクトリー化を単なる技術導入ではなく、企業の競争力強化のための戦略的な取り組みとして位置づけ、長期的な視点で推進していくことが重要です。
スマートファクトリー構築の進め方
スマートファクトリーの構築は、一朝一夕には実現できません。長期的なビジョンと段階的なアプローチが必要です。以下に、効果的な構築の進め方を説明します。
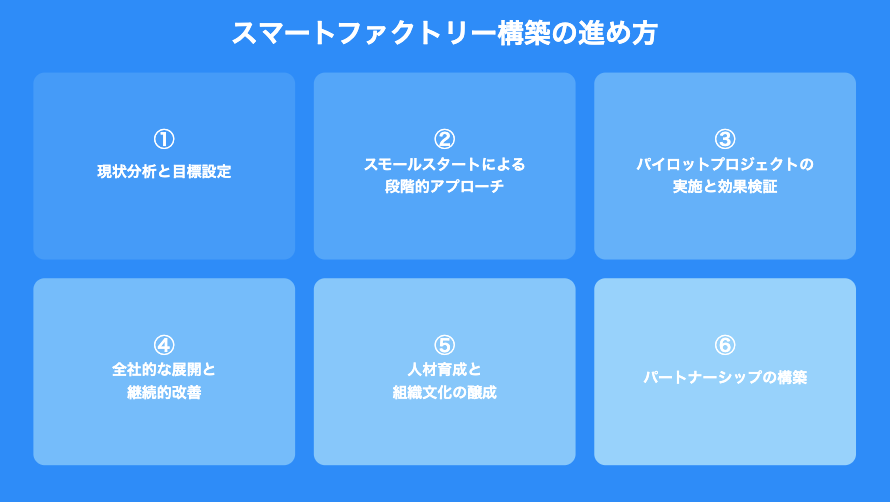
現状分析と目標設定
まず、自社の現状を正確に把握し、明確な目標を設定することから始めます。現在の生産プロセス、設備の状況、データの流れ、人材のスキルなどを詳細に分析します。その上で、スマートファクトリー化によって達成したい具体的な目標(例:生産性向上率、品質改善率、コスト削減率など)を設定します。
この段階では、経営層の関与が極めて重要です。スマートファクトリー化を単なる技術導入ではなく、企業の競争力強化のための戦略的取り組みとして位置づけ、全社的な推進体制を構築することが成功の鍵となります。
スモールスタートによる段階的アプローチ
大規模な投資を一度に行うのではなく、小規模なパイロットプロジェクトから始めることが重要です。例えば、特定の生産ラインや工程に絞ってIoTセンサーを導入し、データ収集と分析を開始するなど、比較的小さな範囲から着手します。
このアプローチにより、初期投資を抑えつつ、スマートファクトリーの効果を実感し、課題を早期に発見することができます。また、従業員の理解と協力を得やすくなり、組織全体の学習曲線も緩やかになります。
パイロットプロジェクトの実施と効果検証
選定したパイロットプロジェクトを実施し、綿密な効果検証を行います。この段階では、定量的な指標(生産性、品質、コストなど)と定性的な指標(従業員の反応、作業の容易さなど)の両面から評価を行います。
効果検証の結果は、次のステップへの重要な指針となります。成功事例は社内で広く共有し、失敗から得られた教訓は今後の改善に活かします。この過程で、自社に最適なスマートファクトリーの形を徐々に明確化していきます。
全社的な展開と継続的改善
パイロットプロジェクトの成果を基に、スマートファクトリー化の範囲を徐々に拡大していきます。この段階では、技術面だけでなく、組織体制や業務プロセスの変革も並行して進める必要があります。
重要なのは、導入後も継続的な改善を行うことです。PDCA (Plan-Do-Check-Act) サイクルを回し、常に新しい技術や手法の導入を検討し、スマートファクトリーの進化を図ります。
人材育成と組織文化の醸成
スマートファクトリーの成功には、それを運用する人材の育成が不可欠です。デジタルスキルの向上を図る研修プログラムの実施や、外部専門家の登用などを計画的に行います。
同時に、データ駆動型の意思決定や、部門を超えた協働を促進する組織文化の醸成も重要です。従業員の意識改革や、新しい働き方への適応を支援するための取り組みも並行して進めます。
パートナーシップの構築
スマートファクトリーの構築には、多岐にわたる専門知識と技術が必要です。自社だけでなく、ITベンダー、設備メーカー、コンサルティング会社などとの戦略的パートナーシップの構築も検討します。
特に中小企業では、産学連携や政府の支援プログラムの活用も有効な選択肢となります。外部の知見を積極的に取り入れることで、より効果的かつ効率的なスマートファクトリー化が可能になります。
このように、スマートファクトリーの構築は長期的かつ全社的な取り組みとなります。段階的なアプローチと継続的な改善を通じて、自社の強みを活かした独自のスマートファクトリーを実現することが、自社の競争力を高めます。
また、弊社では製造現場のDX推進に特化したクラウドサービス「Smart Craft」(スマートクラフト)を提供しています。製造現場の工程管理、品質管理、集計・分析をまとめてデジタル化し、ペーパレス化による生産性改善を実現します。詳しくは資料で紹介しています。
Smart Craftで製造現場のDXを
始めよう!
「Smart Craft」は、これひとつで工場内のすべての業務プロセスをデジタル化できます。
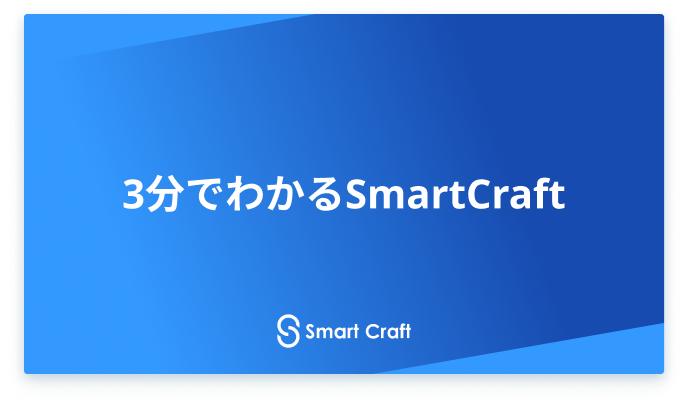
- Smart Craft でできること
- 導入企業の活用事例
- ご利用料金
- 導入の流れ
スマートファクトリーの成功事例
スマートファクトリーの導入は、様々な業種や規模の企業で進められています。ここでは、具体的な成功事例を紹介し、その特徴と導入ポイントを解説します。
事例1:旭鉄工株式会社(自動車部品メーカー)
旭鉄工は、自社の生産性向上の課題に対して、独自の「製造ラインモニタリングサービス」を開発しました。トヨタ自動車向けの受注増加に伴い、設備増設か生産性向上による増産が求められる中、各設備の稼働状況や生産時間を正確に把握する必要がありました。
同社は、米国のソフト開発大手レッドハットと協力し、処理能力や拡張性、信頼性の高いシステムを構築しました。既存設備に安価な汎用センサーを外付けし、設備の稼働状況をリアルタイムで把握できるようにしました。このシステムにより、正常に動いた時間の割合を表す「可動率」や、製品を1つ作るのに必要な時間を表す「サイクルタイム」などの重要指標を可視化しました。
結果として、1時間あたりの生産個数が7割上昇し、当初計画していた生産ライン2本の増設が不要になり、1億4千万円分の設備投資費用を削減することができました。さらに、この成功を基に外販準備に着手し、新たなビジネス展開にもつながっています。
事例2:久野金属工業株式会社(金型加工業)
久野金属工業は、工作機械にIoTを導入して加工状況を把握し、加工条件を最適化する取り組みを行いました。金型部品の複雑形状化や大型化に対するニーズが強まる中、より高い精度と短納期が求められていました。
同社は、工作機械をネットワークにつなぎ、現場作業員がスマートフォンを使って工作機械の加工状況を監視したり、加工終了時間を知らせたりすることができる仕組みを構築しました。さらに、工作機械の主軸にあるモーターの電流値を収集し、加工データや稼働実績と照合することで、最適な加工条件を分析しています。
この取り組みにより、金型部品の高精度化に貢献し、15分を要していた加工時間を8分に短縮することを目指しています。また、「人を機械の番人にしない」ことを前提とした改善を進めており、製造部分はソフトやシステムを駆使して自動化を原則とし、人が考える仕事と区別しています。
事例3:株式会社山本金属製作所(切削加工業)
山本金属製作所は、加工現象の「見える化」と工具の知能化に取り組みました。既存の計測機器では加工現象を正確に計測できないという課題に直面し、製品品質に影響を与える加工中の回転工具刃先の加工現象を正確に計測する手法の開発に着手しました。
同社は、切削工具の先端付近に温度センサ(熱電対)を内蔵することで、刃先の温度を測定可能にしました。これにより、切削加工のIoT化や最適加工条件の選定に利用できるようになりました。工具そのものを「知能化」し、加工現象を「見える化」することで、温度データを見ながら切削条件の良し悪しを判断できるツールを開発しました。
この取り組みにより、切削時の冷却効果・クーラント供給方法の最適化、難削材部品・複雑形状部品の加工改善、切削熱影響におけるドリル・タップ・エンドミルの摩耗進行の折損・寿命予知、工具使用限界温度設定による条件改善など、多岐にわたる効果が得られています。
これらの事例は、スマートファクトリー化において、各企業が直面する具体的な課題に対して、独自の創意工夫でソリューションを開発し、実際の生産性向上や品質改善につなげていることを示しています。また、データ活用やIoT導入が、中小企業においても十分に実現可能であり、大きな効果を生み出せることを実証しています。
スマートファクトリーと人材育成
スマートファクトリーの実現において、人材育成は最も重要な要素の一つです。前章で触れた課題、特に「スマートファクトリー化を牽引する人材の不足」に対応するためには、計画的かつ継続的な人材育成が不可欠です。
スマートファクトリー時代に求められる新たなスキルセット
まず、スマートファクトリー時代に必要となるスキルセットの変化について考えてみましょう。データ分析スキルは、今や製造現場においても重要な能力となっています。膨大な生産データから意味のある情報を抽出し、的確な意思決定に活用する能力が求められます。同時に、情報技術(IT)と製造現場の運用技術(OT)の両方を理解し、連携させる能力も重要です。これらのスキルを持つ人材は、デジタル技術を活用して製造プロセスを最適化し、生産性向上や品質改善を実現することができます。
さらに、基本的なプログラミング知識やAI/IoTツールの活用能力も、今後ますます重要になってくるでしょう。製造現場の従業員が自らデータ分析ツールを操作したり、簡単な自動化スクリプトを作成したりできれば、日々の業務改善により柔軟に対応できるようになります。
一方で、従来の製造ノウハウの重要性が失われるわけではありません。むしろ、長年培ってきた現場の知識とデジタルスキルを融合させることが、スマートファクトリーの成功の鍵となります。例えば、ベテラン技術者の持つ暗黙知をデータ化し、AIやIoTと組み合わせて活用することで、より高度な生産システムを構築することができます。また、デジタル技術に精通した若手社員と現場経験豊富なベテラン社員のコラボレーションを促進することで、新たな価値創造につながる可能性があります。
人材育成の具体的方法
このような人材育成を実現するためには、継続的な学習と能力開発の仕組み作りが重要です。社内外の研修プログラムの活用、オンライン学習プラットフォームの導入、実践的なプロジェクト参加を通じたOJTなど、様々な手法を組み合わせることが効果的です。また、部門横断的な知識共有セッションを定期的に開催することで、組織全体のデジタルリテラシー向上を図ることができます。
成功事例に学ぶ人材育成戦略
経済産業省の「スマートファクトリーロードマップ」でも、「ものづくりとIoTを理解した人材へと育成・意識改革を図る」ことの重要性が強調されています。例えば、株式会社デンソーの事例では、IoTツールを積極的に活用するよう意識改革を行い、ものづくりとIoTの両方を理解した人材の育成に注力しています。また、株式会社エクセディでは、熟練者の組立ノウハウをアニメーションで見せる教育ツールを用いることで、組立作業のスピードを34%向上させるなど、デジタル技術を活用した効果的な技能伝承も実現しています。
スマートファクトリー時代の人材育成は、単にデジタルスキルを教育するだけでなく、製造業の根幹である「ものづくりの心」とデジタル技術を融合させる新たな文化を醸成することが求められます。この変革を成功させるためには、経営層のコミットメントと長期的な視点が不可欠です。従業員一人ひとりがデジタル化の必要性を理解し、自ら学び続ける姿勢を持つことが、スマートファクトリーの持続的な発展につながります。
まとめ:スマートファクトリーが拓く製造業の新時代
この記事では、スマートファクトリーの概念から導入のメリット、課題、そして具体的な構築手順まで幅広く解説してきました。製造業が直面する様々な課題に対し、スマートファクトリー化は有効な解決策となり得ます。
しかし、スマートファクトリー化の道のりは決して平坦ではありません。多くの企業が投資対効果の不確実性や人材不足といった課題に直面しています。これらの課題に対しては、小規模なパイロットプロジェクトから始めること、外部の専門家や先進事例を積極的に活用すること、そして組織全体でデジタル変革への理解を深めることが有効です。
製造業の未来に向けて、今こそアクションを起こすときです。まずは自社の現状を分析し、スマートファクトリー化のロードマップを描いてみましょう。そして、できるところから一歩ずつ、デジタル技術の導入と人材育成を進めていくことが重要です。
弊社が提供する初期費用を抑えたスモールスタートが可能な「Smart Craft」(スマートクラフト)は、このようなスマートファクトリー化の取り組みをサポートします。製造現場の工程管理、品質管理、集計・分析をまとめてデジタル化し、ペーパレス化による生産性改善を実現します。特に、効果の見えにくさや初期投資の課題に対して、段階的な導入と早期の効果創出を支援します。
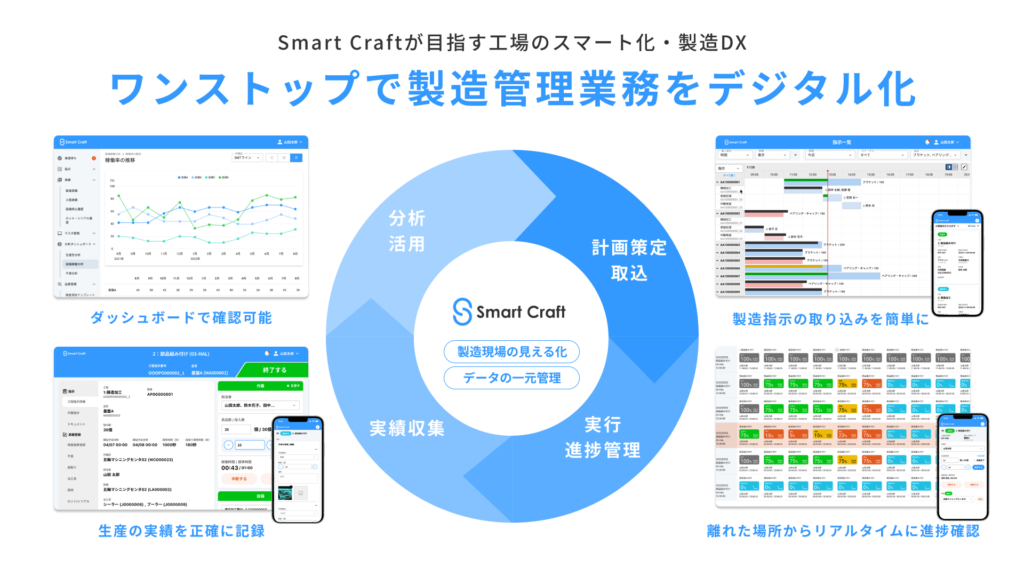
また、直感的なインターフェースにより、デジタルスキルの高くない従業員でも容易に使用できるため、人材育成の課題解決にも貢献します。まずは資料請求からSmart Craftの導入を検討してみてください。
Smart Craftで製造現場のDXを
始めよう!
「Smart Craft」は、これひとつで工場内のすべての業務プロセスをデジタル化できます。
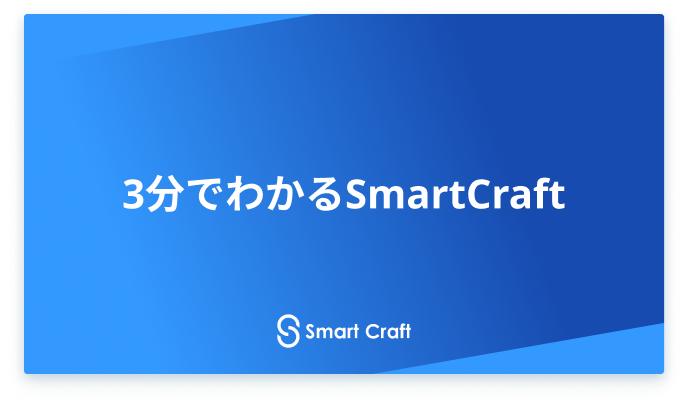
- Smart Craft でできること
- 導入企業の活用事例
- ご利用料金
- 導入の流れ