工場の見える化とは?メリットや具体的な進め方を事例交え解説
近年、製造業を取り巻く環境は大きく変化しています。多品種少量生産や短納期化が求められる一方、国内では少子高齢化による人手不足が深刻化しています。こうした中、製造業が競争力を維持・強化していくためには、デジタルトランスフォーメーション(DX)の推進が不可欠と言えるでしょう。
経済産業省が2018年に公表した「DXレポート」では、2025年までに日本企業の40%がDXへの対応に遅れると、年間最大12兆円の経済損失が生じる可能性があると試算されています。製造業においても例外ではなく、業務プロセスや組織、ビジネスモデルをデジタル技術によって革新していくことが急務となっています。
その鍵を握るのが、工場の「見える化」です。テクノロジーを活用して生産現場のデータを収集・可視化し、それを基に改善を図ることで、品質向上や納期短縮、コスト削減を実現できます。また、属人化したノウハウやプロセスのデジタル化は、熟練工の引退などによる技術流出リスクの回避にもつながります。
しかし、「何から着手すべきかわからない」「費用対効果が見えない」など、見える化の取り組みに二の足を踏む企業や製造現場も少なくありません。そこでこの記事では、工場の見える化の進め方やポイントについて、先進企業の事例も交えて詳しく解説します。
また、弊社では製造現場の見える化の取り組みを低コスト・短期間で始められるクラウドシステム「Smart Craft」を提供しています。詳しくは資料で紹介しています。⇒資料のダウンロードはこちら
工場の見える化とは何か
「見える化」の定義
工場の「見える化」とは、生産現場で日々発生する設備の稼働状況や品質データ、作業工数などをデジタル化し、リアルタイムに可視化・共有することを指します。IoTセンサーやカメラ、スマートフォン・タブレットなどを活用して、現場の状況を「見える」状態にするのが特徴です。
具体的には、次のような情報を把握できるようにする取り組みです。
- 設備の稼働状況(稼働率、故障頻度、メンテナンス履歴など)
- 品質データ(不良率、検査結果、トレーサビリティ情報など)
- 作業工数(作業時間、手待ち時間、アイドルタイムなど)
- 進捗状況(計画に対する実績、納期遅延リスクなど)
- 在庫状況(原材料、仕掛品、完成品の在庫量、在庫回転率など)
これらの情報を可視化し、関係者で共有することで、現場の実態を俯瞰的に把握し、問題点を特定して改善につなげることができるようになります。
工場の見える化の目的
見える化の目的は、大きく以下の3点に集約できます。
①生産プロセスの問題点や非効率な箇所(ムダ)を特定し、迅速に対策を打つ
見える化によって、設備の予期せぬ停止や品質のバラつき、作業の属人化など、現場の問題点が浮き彫りになります。それらを定量的に把握し、改善のPDCAサイクルを素早く回すことが可能となります。
②属人化された作業手順やノウハウを「見える」状態にし、効率的な引き継ぎや改善を促す
ベテラン作業者の経験と勘に依存した属人的な業務は、ノウハウの流出リスクがあるうえ、カイゼンの足かせにもなります。一方、作業を可視化・データ化することで、属人化やブラックボックス化を防ぐことができます。
③経営層から現場オペレーターまで、全社一丸となって目標達成に取り組む風土を醸成する
リアルタイムの稼働データや進捗状況を、社内で広く共有することは、組織の連帯感を高める効果もあります。トップの意思や顧客の声を現場レベルで実感でき、改善への当事者意識が醸成されます。
見える化がもたらすメリット
工場の見える化は、製造業に多くのメリットをもたらします。
①ムダの削減と生産性の向上
設備や品質、工程のムダが見える化されれば、ボトルネックを特定し、素早く手を打つことができます。不良品の削減とリードタイムの短縮は、生産性を大きく引き上げるでしょう。
②リードタイムの短縮と在庫の最適化
受発注から調達、生産、出荷までの各プロセスをデータ連携させることで、需給のズレを防ぎ、同期の取れたオペレーションが可能になります。その結果、リードタイムの短縮と在庫の最適化が進み、キャッシュフローの改善にもつながります。
③高品質なものづくりと顧客満足度の向上
データに基づく品質管理の徹底は、不良品の流出を防ぐだけでなく、品質のバラつきを抑え、顧客の信頼を高めることにつながります。また、見える化されたデータを営業活動にも活かせば、提案力の向上も見込めるでしょう。
以上のように、工場の見える化には、経営面でも品質面でも大きなメリットがあります。
ただし、自社の目的や課題を踏まえ、適切な範囲・レベルで行うことが重要です。闇雲に手を広げるのではなく、費用対効果を見極めながら、段階的に取り組んでいくことが大切と言えるでしょう。
工場の見える化を進める方法は?具体的な6つのステップを紹介
工場の見える化を成功させるためには、まず全社的な理解と合意形成が不可欠です。トップ自らがDXの必要性を発信し、現場を巻き込んで推進体制を整備しましょう。そのうえで、以下の6つのステップを踏んでいくことが重要です。
ステップ1:見える化の目的と対象範囲の明確化
まずは、自社が見える化に取り組む目的を明文化します。前述の3つの視点(ムダの削減、属人化防止、全社最適)を参考に、経営課題や事業戦略と紐付けて具体的なゴールを設定しましょう。あわせて、工場のどの製造プロセス・設備を見える化するのか、対象範囲を明確にします。
ステップ2:現状分析と課題抽出(ヒアリング・現場観察)
次に、対象となる製造プロセスの業務フローや作業手順、使用帳票などの現状を詳しく分析します。現場リーダーへのヒアリングと併せ、実際の作業風景を動画で撮影するなどして、属人的なノウハウや非定型業務の実態を可視化していきます。問題点や改善機会を抽出し、見える化による効果をシミュレーションするのもポイントです。
ステップ3:収集すべきデータの洗い出しと収集方法の検討
見える化のゴールと現状分析を踏まえ、どのようなデータが必要かを整理します。設備の状態や品質情報など、自動収集できるものはIoTやセンサー技術の活用を検討しましょう。一方、作業者の動きや判断といった目に見えにくいプロセスは、スマートフォン・タブレットなどによる手入力の仕組みづくりが欠かせません。
ステップ4:データ収集・分析基盤の構築
収集したデータを一元管理・可視化し、分析につなげるためには、それに適したシステム基盤の構築が重要です。工場の特性や利用者の習熟度を考慮しつつ、直感的に操作でき、リアルタイムな情報把握が可能なツールを選定します。クラウドの活用で導入コストを抑えつつ、拡張性の高い基盤づくりを目指しましょう。
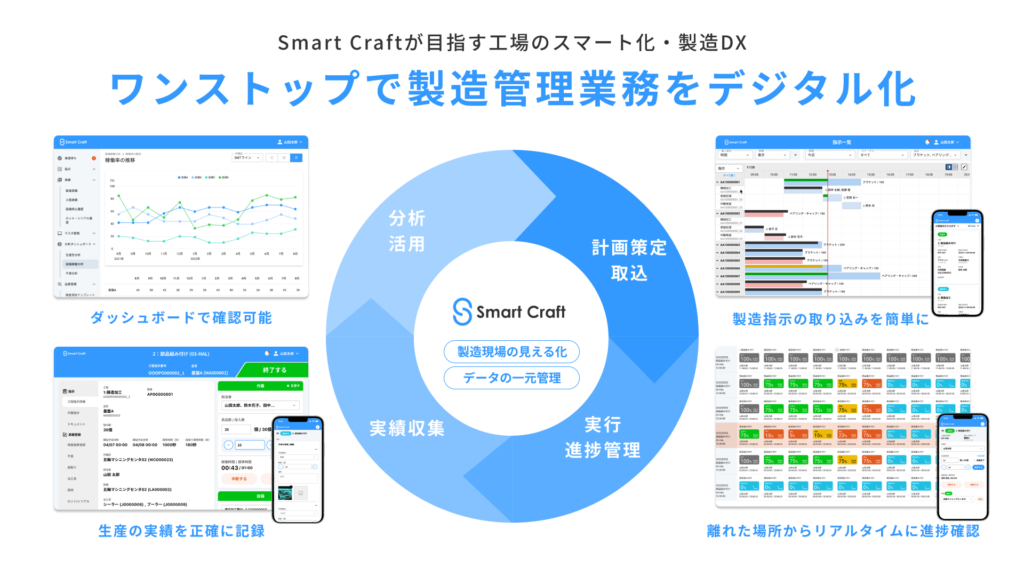
Smart Craftのような製造業特化型のクラウドサービスを活用することで、導入コストを抑えつつ、より効果的に工場の見える化を進めることができます。詳しくは資料で紹介しています。
Smart Craftで製造現場のDXを
始めよう!
「Smart Craft」は、これひとつで工場内のすべての業務プロセスをデジタル化できます。
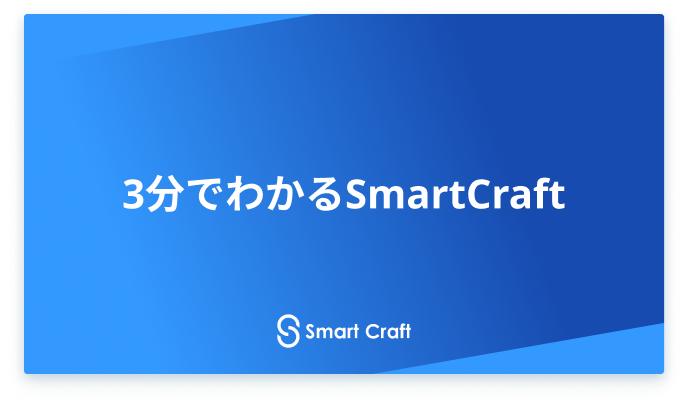
- Smart Craft でできること
- 導入企業の活用事例
- ご利用料金
- 導入の流れ
ステップ5:現場へのシステム導入と従業員の教育・習熟
いよいよ、見える化システムの現場導入です。トップダウンではなく、キーマンを中心に実証実験から始め、早期の成功体験を積み上げながら、段階的に展開していくのがコツです。作業手順の変更点や、新しいツールの使い方をマニュアル化し、対話型の研修を重ねることで、従業員の納得と習熟を促進しましょう。
ステップ6:PDCAサイクルによる継続的改善
見える化はゴールではなく、スタート地点に過ぎません。可視化されたデータを活用し、日々の改善サイクルを回すことが重要です。KPI(重要業績評価指標)を設定し、進捗を定期的にモニタリングする仕組みをつくりましょう。現場の知恵を結集しながら、より高いレベルの見える化を目指し、PDCAを回し続けることが、工場の見える化の成否を分けると言っても過言ではありません。
以上のステップを着実に踏んでいくことで、製造業でも工場の見える化を実現できるはずです。とはいえ、一朝一夕にはいきません。トライ&エラーを恐れず、小さな成功を積み重ねながら、工場の見える化を進めていきましょう。
関連記事
製造業DXとは? 成功させるための6つのステップを徹底解説
デジタル技術を活用した工場の見える化事例
ここからは、工場の見える化に取り組み、大きな成果を上げている先進企業の事例を見ていきましょう。業種や規模は異なりますが、いずれもデジタル技術を活用した見える化によって、現場の改善を加速させています。
事例1:A社(電子部品メーカー)
グローバルに展開するA社は、スマートフォンや自動車向けの電子部品を生産しています。同社は、世界各地の工場にIoTセンサーを導入し、設備の稼働状況や品質データをリアルタイムに可視化するシステムを構築しました。システムによる異常検知や原因分析により、不良率を50%削減。センシング技術と自動化の進展により、リードタイムも30%短縮しました。また、需要予測と在庫情報を同期させることで、サプライチェーン全体の最適化も実現しています。
事例2:B社(食品メーカー)
業務用食材を製造するB社では、需要変動が大きく、欠品と過剰在庫が頻発していました。そこで同社は、受注・生産・出荷の全プロセスをデジタル化し、需給バランスを可視化するシステムを導入しました。機械学習による需要予測の高度化と、最適な生産・配送計画の自動立案により、平均在庫量を20%削減しつつ、機会損失をゼロにすることに成功。リードタイムの短縮により、顧客満足度も大幅に向上しています。
事例3:C社(自動車部品メーカー)
エンジン部品を手掛けるC社は、多品種少量生産に対応するため、混流ラインを導入していましたが、設備故障によるライン停止が頻発し、タクトタイムのロスが課題となっていました。そこで、設備の状態をリアルタイムに監視し、異常の兆候を検知して保全を最適化する「予知保全システム」を構築。さらに、作業者の動線や手順をデジタルツールで分析し、ボトルネックとなっていた工程を自動化したことで、ラインの稼働率が15%向上。品質と生産性の両立を実現しました。
これらの事例に共通するのは、見える化の対象を「設備」「品質」「需給」「作業者」など、多角的に捉えている点です。さまざまな角度からデータを収集・分析し、ボトルネックを特定して改善することで、工場のDXを加速させているのです。
ツールやシステムの導入にとどまらず、現場の知恵を引き出し、継続的な改善を実践する風土づくりまで取り組むことが重要だと言えます。
工場の見える化の導入・推進における4つのポイント
ここまで見てきたように、工場の見える化は製造業のDXを大きく前進させる有効なアプローチです。しかし、単にシステムを導入すれば成果が上がるわけではありません。以下の4つのポイントを押さえることが、見える化の成否を分けると言っても過言ではないでしょう。
ポイント1:トップのリーダーシップとデジタル投資
見える化の推進には、現場の習慣や文化を変える覚悟が必要です。トップ自らがDXの必要性を語り、「データに基づく経営」への転換を宣言することが何より重要。また、システムや人材への投資を惜しまず、企業のDNA(体質)そのものを変えていくリーダーシップが問われます。
ポイント2:部門横断でのデジタル人材育成と変革マネジメント
見える化は、特定の部門だけでなく、販売・調達・物流など、バリューチェーン全体での取り組みが欠かせません。組織の垣根を越え、データサイエンティストやプロセスエンジニアなどの人材を育成・獲得する必要があります。変化を恐れず、挑戦を称賛する組織文化への変革も重要なテーマと言えるでしょう。
ポイント3:PoC(概念実証)からスモールスタートで効果を実感
DXの壁は「目的を見失うこと」と言われます。壮大なビジョンを掲げるのは重要ですが、一気に全社展開を目指すのは得策ではありません。まずは特定の製造プロセス・ラインで小規模なPoC(概念実証)を行い、早期の成果を実感しながら、段階的に範囲を広げていく。小さな成功体験を積み重ねる地道な歩みが、DXを加速させる近道です。
ポイント4:外部リソース(パートナー、システムなど)の有効活用
製造業のデジタル化は、もはや自前主義では限界があります。戦略立案や人材育成、システム構築などは、外部の力も借りながら、オープンイノベーションを進めることが肝要です。その際、自社の強みと弱みを冷静に見極め、中長期を見据えたパートナー・システム選びを心掛けましょう。
まとめ
この記事では、工場の見える化について、具体的な進め方や先進事例、押さえるべきポイントを解説してきました。グローバル競争が激化し、ニーズの多様化・個別化が進む現在、大量生産による画一的な製品づくりはもはや通用しません。変化に俊敏に適応し、付加価値を生み出し続けるスマートファクトリーへの変革が急務と言えるでしょう。
工場をデータドリブンな「デジタルの世界」へと昇華させる。それは一朝一夕には実現しません。トップのコミットメントを起点に、現場の一人ひとりの意識改革を促し、失敗を恐れず改善を積み重ねる。それこそが、製造業のDXを成功に導く王道と言えます。
最後になりますが、弊社が提供する「Smart Craft(スマートクラフト)」は、工場の見える化に必要な機能を網羅したクラウド型のソリューションです。ペーパーレス化や情報共有、リアルタイム監視、簡単なグラフ作成、データ分析まで、現場のDXをワンストップでサポート。すでに製造現場への導入実績もあります。⇒年10%相当の工数削減を実現したSmart Craftの導入事例を見る
ぜひこの記事を参考に、自社に合ったDXのアプローチを探ってみてください。製造業の競争力を維持・強化していくためにも、工場の見える化を通じて、業務効率化や生産性向上を目指しましょう。まずは資料請求からSmart Craftの導入を検討してみてください。
Smart Craftで製造現場のDXを
始めよう!
「Smart Craft」は、これひとつで工場内のすべての業務プロセスをデジタル化できます。
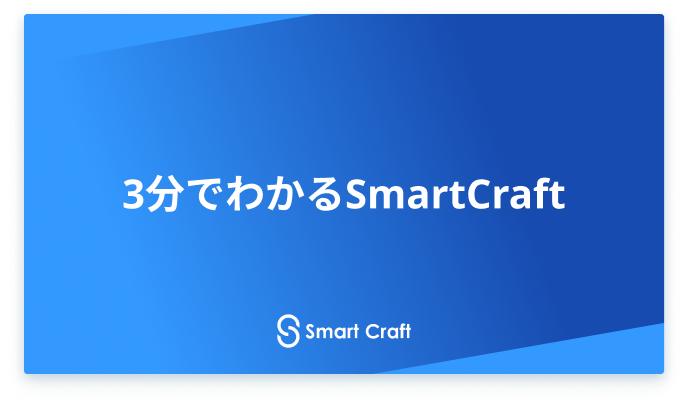
- Smart Craft でできること
- 導入企業の活用事例
- ご利用料金
- 導入の流れ