製造業DXとは? 成功させるための6つのステップを徹底解説
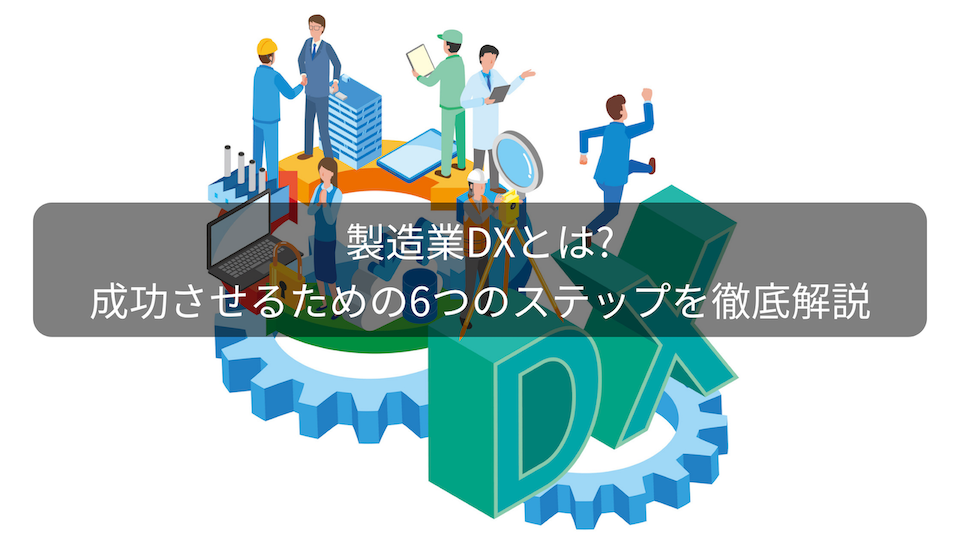
製造業は日本の雇用の約20%、GDPにおいても約20%を占める一大産業である一方で、近年、新型コロナウイルスの感染拡大、ロシアによるウクライナ侵攻等による原材料価格やエネルギー価格の高騰、物流の混乱というように、製造業にとってのリスク要因が非常に複雑化しています。
このように製造業を取り巻く環境に大きな変化が生じている中で、DX(デジタルトランスフォーメーション)によって、事業活動の効率化や、ビジネスモデルの変革を実現し、企業の競争力を高めることが必要不可欠となっています。
この記事では、前半部分で製造業におけるDXの定義や課題を整理し、後半部分で製造業DXを成功させるためのステップを詳しく解説します。
Smart Craftで製造現場のDXを
始めよう!
「Smart Craft」は、これひとつで工場内のすべての業務プロセスをデジタル化できます。
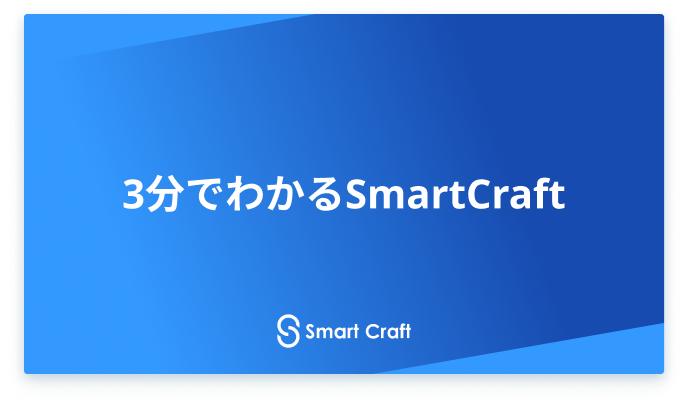
- Smart Craft でできること
- 導入企業の活用事例
- ご利用料金
- 導入の流れ
目次
製造業におけるDXとは
DXの定義について、経済産業省「デジタルガバナンスコード 実践の手引き 2.0」によると、以下2点が挙げられています。
- デジタル技術やツールを導入すること自体ではなく、データやデジタル技術を使って、顧客目線で新たな価値を創出していくこと
- そのためにビジネスモデルや企業文化等の変革に取り組むこと
(出典: 経済産業省「デジタルガバナンスコード 実践の手引き 2.0」)
キーワードを抜粋して要約すると「データ活用」「デジタル技術活用」という手段を用いて、「新たな価値の創出」「ビジネスモデル変革」「企業文化変革」に取り組むこと、となっています。製造業に限らず全ての業種に向けてDXとは何かが定義されています。
出典画像の最下部にも記載があるように、「AIで何かできないか」は手段が目的になってしまっており、これはDXではありません。DXにおいて、データ活用やデジタル技術活用といったITはあくまで手段なのです。
製造業においても同様で、このDXの定義こそが重要です。後半の6つのステップでも紹介しますが、DXによって何を変革したいのかが成功の鍵になります。
製造業における3つの課題
同じく経済産業省「製造業を巡る動向と今後の課題」によると、日本の製造業においては以下の3点が課題として挙げられています。
それぞれ詳しく解説していきます。
課題① 人手不足、属人的改善による部分最適
日本は従来「現場が強い」と言われてきましたが、いま「サプライチェーン」と「エンジニアリングチェーン」は人手不足、属人的改善による部分最適、設備の老朽化等、様々な問題を抱えています。
(出典: 経済産業省「製造業を巡る動向と今後の課題」)
一方で海外では、ITを駆使した製造プロセスのサービス産業化が進んでいます。具体的には、製造プロセスを標準化・デジタル化し、クラウド技術も活用した上で、サービスとして他社展開する企業(製造業系サービス事業者)が出現しています。日本においても、スタートアップで製造業系サービス事業者が出つつあります。
現場力だけで勝てる時代は終焉を迎えつつあり、現場力という強みを進化させた「現場力 x DX」が日本の製造事業者が目指すべき方向性です。
課題② デジタル化やデータ活用が進んでいない
製造工程のデータ収集に取り組んでいる企業の減少や、データを実際に役立てている企業の割合も伸びていないなど、デジタル化やデータ活用が進んでいません。
(出典: 経済産業省「製造業を巡る動向と今後の課題」)
工場内で紙やホワイトボードを使って作業実績を記録し、あとで手作業でExcelに入力しデータ集計している企業がほとんどでしょう。これが非常に手間のかかる作業であることは、製造業に従事する人であれば誰もが知っており、このような効率の悪い業務が存在することが、データ収集の取り組みを妨げている要因です。
最近になって、工場内でもタブレットやスマホを活用して作業実績を記録する企業も出てきています。導入時は慣れるまで大変ですが、現場に馴染んでしまえば、その後のメリットは計り知れません。デジタルツールの活用こそが課題解決の第一歩となります。
課題③ 攻めのIT投資ができていない
旧来型システムの更新・維持を目的にIT投資がなされており、ビジネスモデル変革や人材育成といった、ダイナミック・ケイパビリティ※ を重視したIT投資ができていません。
※「ダイナミック・ケイパビリティ」とは、戦略経営論における学術用語であり、経済産業省「ものづくり白書2020」によれば「環境や状況が激しく変化する中で、企業がその変化に対応して自己を変革する能力」である。カリフォルニア大学バークレー校ハース・ビジネススクール教授のデイヴィッド・J・ティース氏によって提唱され、近年、注目を浴びている戦略経営論である。
(出典: 経済産業省「製造業を巡る動向と今後の課題」)
製造業特有の課題として、大型の機械や設備を所有する、つまり、BS(貸借対照表)上の固定資産の割合が高くなるため、それらのメンテナンスのために守りの投資が必要になります。結果として、攻めのIT投資に余裕がなくなってしまいます。
また、日本の製造業においては、ロボットによる自動化など設備投資は潤沢に行われていますが、ソフトウェアに対する投資が少ないのも現状です。
昨今は製造業向けシステムもクラウドなど安価なものも増えており、スモールスタートでの投資も可能です。攻めのIT投資をしなければ企業の存続が危うくなることは必至であり、攻めのIT投資こそが解決策となるでしょう。
以上3つの課題を紹介しましたが、1つ目と2つ目は製造業特有の課題であり、これらに対してはDXが最も効果的な解決策であることは疑いようがありません。3つ目については製造業に限定されない課題ですが、業種に関わらず、やはりDXこそが有効な解決策となります。
製造業DXを成功させる6つのステップ
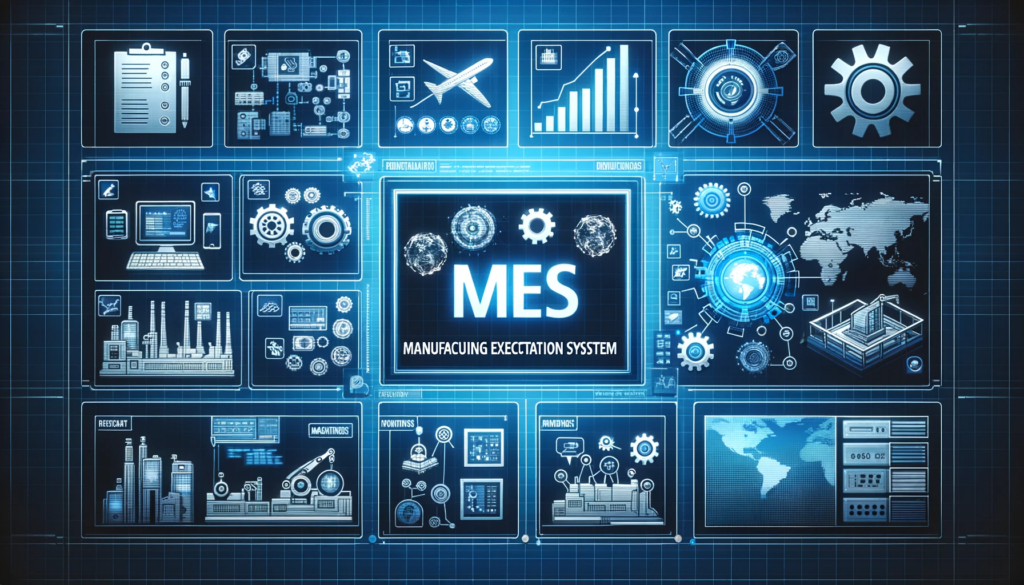
前の章では製造業DXにおける課題を見てきましたが、この章では、それらの課題をどのように克服するのか、どのようなアプローチで製造業DXを成功に導いて行けば良いのかを紹介していきます。
- ステップ① 目的を明確にする
- ステップ② 責任者を決める
- ステップ③ 適切なシステムを選定し、導入する
- ステップ④ データを正しく取得する
- ステップ⑤ データを正しく分析する
- ステップ⑥ 改善策を検討し、改善活動を実施する
ステップ① 目的を明確にする
製造業DXの最終的な目的は「生産性向上」ということになると思いますが、単に生産性向上だけだと粗く、より具体的な目的にする必要があります。例としては、以下のようなものが挙げられます。
- 現場の省力化、省人化:最近人が採用できない、または、コロナ禍で外国人労働者が減ってしまったため、少ない人数で効率的に現場を回せるようにしたい。
- 設備の稼働率改善:稼働状況をデータ化することで稼働率を可視化し、稼働率を上げたい。
- 歩留まり率改善:不良理由や不良率等をデータ化することで原因や傾向を把握し、歩留まり率を改善したい。
- トレーサビリティ:出荷済み製品に不良があった際に紙の日報を遡るのは時間がかかる。データを遡ることで時間短縮したい。
- 納期予測の精度向上:営業担当が工場長や現場リーダーに納期を確認しても、経験ベースで精度が低い。DXによって納期予測の精度を高めたい。
- 部署間の情報共有:製造⇔営業、製造⇔品質管理、製造⇔本社、といった、異なる部署間での情報共有・情報連携を強化したい。
- 情報の一元管理:進捗状況、工程管理といった現場ごとで個別に管理している情報を一元管理したい。
- 情報の入力の二度手間をなくしたい:紙、Excel、ホワイトボードといった情報を人力で集約してデジタルデータにしているが、現場の入力からデジタルでのデータ管理にしたい。
- 技能伝承:熟練者の優れた技を、勘やコツ、経験による伝承ではなく、DXによってデータを用いて分かりやすく伝承できるようにしたい。
- 多言語対応:外国人労働者を増やしたので、紙でのやり取りだと伝達に時間がかかる。瞬時に他の言語に翻訳して指示を出せるようにしたい。
これら目的例全てに共通していることとして、デジタル化は必須であり、データの活用によって生産性改善を進めていくことになります。
ステップ② 責任者を決める
責任者には、以下の3つのパターンがあります。
- 工場長もしくは製造部長:やはり現場を知らないとDXを推進できないため、責任者に最も適していると言えます。実際、このケースが最も多いです。
- 情報システム部門の組織長:次に多いのはこのケースです。DX推進においてはITの知識が求められることや、社内システムに精通していることが求められるためです。
- DX専門の横断的な組織の長:最近では、DXを行う横断的な部門が設置されるケースや、DXを目的としたプロジェクトチームが立ち上がるケースもあります。
責任者は、以下の3点を推進できる人物を選定します。
経営層を巻き込む
経営層の理解も非常に重要な要素です。というのも、製造現場のDXは多くの人を巻き込むことになりますし、場合によっては大きな費用が発生するためです。経営層という後ろ盾がなければ、スピード感が急激に落ちたり、プロジェクトが頓挫してしまう可能性すらあります。経営陣が製造現場DXの重要性を理解し、実現にもコミットすることで、DXの成功に大きく近づきます。
現場を巻き込む
DXといっても、データ入力や業務オペレーション変更など、実働は現場が担います。よって、現場の理解が得られてないと、絵に描いた餅になってしまいます。
経営層や本社部門が決めたことを一方的に現場に押し付けるようなやり方は、現場の理解が得られず失敗するケースが多いので注意が必要です。現場への丁寧な説明が欠かせません。
専任担当者を設ける
責任者は役職者であるためフルコミットは難しく、責任者の下にDX推進の専任担当者(=フルコミットできる人)を設けます。また、責任者も最低20%、できれば50%はDX推進業務に工数を割きたいところです。
以上の通り、責任者だけでなく、経営層・現場という三者の協力が必要不可欠になります。
ステップ③ 適切なシステムを選定し、導入する
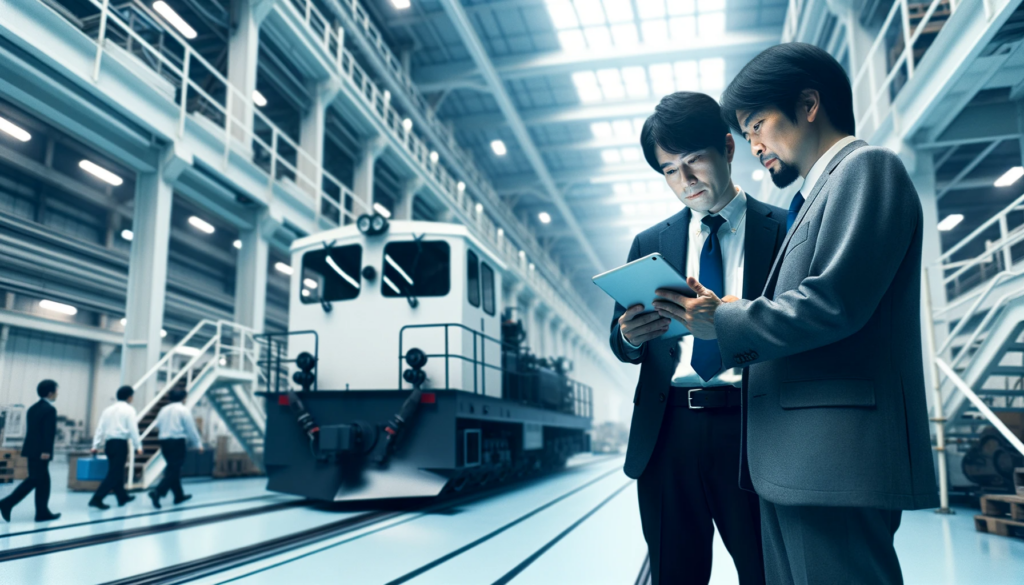
責任者の次はシステム活用です。DXである以上、システム活用は必須です。システム選定のポイント3点と、システム導入のポイントを解説します。
システム選定のポイント① 現場が使いやすいこと
現場では、人やモノが動いているため、その現場にフィットしたシステムや端末が必要です。具体に確認すべきポイントとしては、以下のようなケースが挙げられます。
- 画面表示:現場のレイアウト変更の可能性を考えると、設置場所を移動しやすいタブレットやスマホが適しているケースが多いでしょう。よって、タブレットやスマホに表示が最適化されている必要があります。もちろんPCを利用するケースであっても、画面の使いやすさは重要になります。
- 入力方法:軍手など文字入力が難しい現場では、タッチペンを使い、プルダウン、チェックボックス、ボタンなど、直感的に操作できる入力方法があるかどうかも重要です。バーコード入力、ORコード、音声入力などがあるかどうかも確認しましょう。
- その他固有の事情:入力方法だけでなく、水濡れ、粉塵、油、火花など、現場によって端末に求められる特性も異なります。設置場所の工夫や専用ケースの利用などで端末の故障を防ぐこともできますが、防塵・防水・耐熱・耐衝撃といった端末性能も検討すると良いでしょう。
システム選定のポイント② 小さく検証できること
製造業でよくあるDX失敗事例は、風呂敷を広げすぎて、数千万円や数億円かけて巨大なオンプレミスのシステムを導入してしまうケースです。問題は大きく2つあり、1つ目は、これだけの金額規模になると、要件定義から、データセンタを借りてサーバ構築、開発して導入と、年単位で時間を要し、システムが稼働した際にはすでにそのシステムが陳腐化してしまっているケース。2つ目は、巨大なシステムを入れてしまったため、現場への周知や教育が行き届かず、稼働開始と同時に現場が混乱するケースです。
その点SaaSだと、トライアル(お試し利用)を設けている製品が多く、まずはトライアルで自社の現場にフィットするかどうか検証できます。本導入に際しても、いきなり会社全体や工場全体に広げずに可能な限り最小単位で、具体的には、1つのライン、1つの工程、1つの現場、というような形でスタートすることができます。
他にもSaaSなどのクラウドシステムがスモールスタートに適している理由としては以下のようなものが挙げられます。
- クラウドなのでデータセンタやサーバの準備が不要
- ノーコードで導入しやすい、また、自社の特性に合わせて柔軟に設定が可能
- 使用量に応じた課金体型になっているため、最低限の有償契約で安価に検証することが可能
- 関係者も最小限になるので、外部コストだけでなく、検証にかかる社内工数も最小限で済ませることが可能
- 製造業の生産性改善では、デジタルツインを活用してライン組み替えをするケースがあるが、SaaSの活用で、ライン組み替えの蓋然性をより高めることが可能
- 日々機能がアップデートされ進化していくので、機能が足りない場合は開発元に要望を伝えることで、より自社に適した運用が可能
当社の顧客においても実際に、過去に一度大きく失敗した経験があるためスモールスタートできることを必須条件としていた顧客がおりました。
システム選定のポイント③ 外部システムと連携できること
製造業のシステムは、①計画層、②実行層、③制御層に分けられ、3つの層すべてを網羅するシステムは存在せず、各層で独立したシステムが存在しています。製造業に詳しくない方にとっては不思議かもしれませんが、それだけ製造業は複雑であり、DXが難しいことに他なりません。各層で個別のシステムが存在する以上、それぞれのシステムの連携をいかに無駄なく行えるかが生産性を大きく左右します。
外部システム連携の勘所3点を以下に紹介します。
1. ①計画層 → ②実行層 → ③制御層 というデータの流れにおける連携
システム連携によって、本社(計画層)から下りてきたものを、現場(実行層)で受け取って、装置(制御層)を動かす、といった流れになります。
この流れを人の手を介さずにシステム連携によって実現することで、生産管理からの変更指示など急な案件であっても、現場が混乱することなく柔軟な対応が可能になります。
2. ③制御層 → ②実行層 → ①計画層 というデータの流れにおける連携
昨今では、IoT(Internet of Things: モノのインターネット)の進化により、制御層からデータ収集ができる製品が増えてきています。例えば、PLC(Programmable Logic Controller: プログラマブル・ロジック・コントローラの略称)で、日本語に直訳すると「プログラム可能な論理回路の制御装置なども専用のデバイスやゲートウェイで接続して、設備から直接実行層(MES)にデータを送ることができます。
テクノロジーの進化により、制御層から実行層を通じて計画層まで人の手を介さずにデータを送ることで、データの一元管理を実現するだけでなく、実績をリアルタイムにモニタリングできるなどより高精度な予実管理やデータ分析が可能になります。
3. システム連携方法
システム連携においては、当たり前ですが、できる限りシステムの数を少なくすることが望ましいでしょう。工場においては、レイアウト変更や製品の仕様変更などは常に発生するため、システム数が増えるとその分設定変更に時間が取られます。
各システム間の連携方法としては、計画層と実行層はAPI(Application Programming Interface)を介して、実行層と制御層はPLCを介して連携することが望ましいでしょう。
連携の方法として良くあるパターンが、システムからExcelをダウンロードし、そのデータを別システムへアップロードするといった半自動連携です。検証時であればこちらで構いませんが、本格運用するにあたっては、リアルタイム性に劣ることや、作業ミスが発生する可能性があることなどから、半自動は極力避け、人の手を介さずに連携できることが望ましいでしょう。
<各層の代表的なシステムを紹介>
各層の代表的なシステムを以下に紹介します。検討開始段階の場合は参考にしていただければ幸いです。
①計画層
計画層のシステムとしてはERP(Enterprise Resource Planning: 企業資源計画)が代表的で、業種や企業規模などによって多様な製品が提供されています。
- 大企業向け: SAP, Oracle, etc.
- 製造業特化: EXPLANNER/Z(NEC), GLOVIA smart PRONES(富士通), etc.
②実行層
実行層のシステムとしてはMES(Manufacturing Execution System: 製造実行システム)が代表的で、ERP同様に業種や企業規模によって多様な製品が提供されています。
- 外資系メーカー: ロックウェル, シーメンス, ダッソー・システムズ, etc.
- 日本メーカー: 日立, 横河電機, 三菱電機エンジニアリング, NEC, etc.
余談にはなりますが、実行層のシステムにはクラウド製品が少なく、製造現場DXをスモールスタートしづらい理由の一つとなっています。
③制御層
制御層のシステムでは、ロボットメーカーやPLCメーカーが主体となっています。
- ロボット: ファナック, 安川電機, etc.
- PLC: キーエンス, 三菱電機, オムロン, etc.
- IoTデバイス: たけびし, 金沢エンジニアリング, etc.
システムの選定は、製造現場DXにおいては最も重要な要素の1つです。拙速な意思決定を避け、しっかりと情報収集した上で、慎重に決断していただければと思います。
関連記事:
MES(製造実行システム)とは?必要性や機能、導入メリット、ERPとの違い
システムの導入
システムを選定したら、次はシステムの導入になります。システム導入においては以下の3点がポイントになります。
1. 信頼できる専門家をプロジェクトチームに入れる
ここで言う専門家とは、単なるシステムの専門家ではなく、(1)現場を理解している、(2)システムに精通している、人物になります。ベンダーはシステムには詳しいですが、製造業に精通しているわけではありません。また、ビジネスですから、要求した以上のことはせず、必要最低限のことしかしないことも考えられます。
もし社内にそういった人物がいない場合は外部に頼ることになりますが、経歴を確認するなどし、信頼できるかどうかをしっかり見極めましょう。
2. 無理のない導入計画を立て、都度見直す
最初からギリギリのスケジュールになっているケースは非常に危険で、考慮漏れやミスが発生しやすいです。システム導入においては、大抵の場合において予期できなかった課題が出てくるものです。ある程度バッファを持った計画を立て、必要に応じて計画変更を行いましょう。
3. 稼働開始後のトラブルを想定しておく、リカバリープランを作っておく
システム稼働開始のタイミングでは、100%完璧にうまく行くケースは稀ではないかと思います。入念に準備したとしても、考慮漏れなどヒューマンエラーもあれば、システムのバグ(不具合)や、大量アクセスや大量データ投入によるシステムダウンなど、想定外のトラブルが発生するものです。
しかし、システムがうまく稼働しないからといって、製造を止めるわけにはいきません。少し大げさかもしれませんが、失敗する前提で設計ておきましょう。代表的な進め方としては、一定期間(1-3ヶ月程度)は既存の運用と並行稼働する方法です。現場の負荷は多少高まりますが、現場を止めることなくシステム導入を進めることができます。
ステップ④ データを正しく取得する
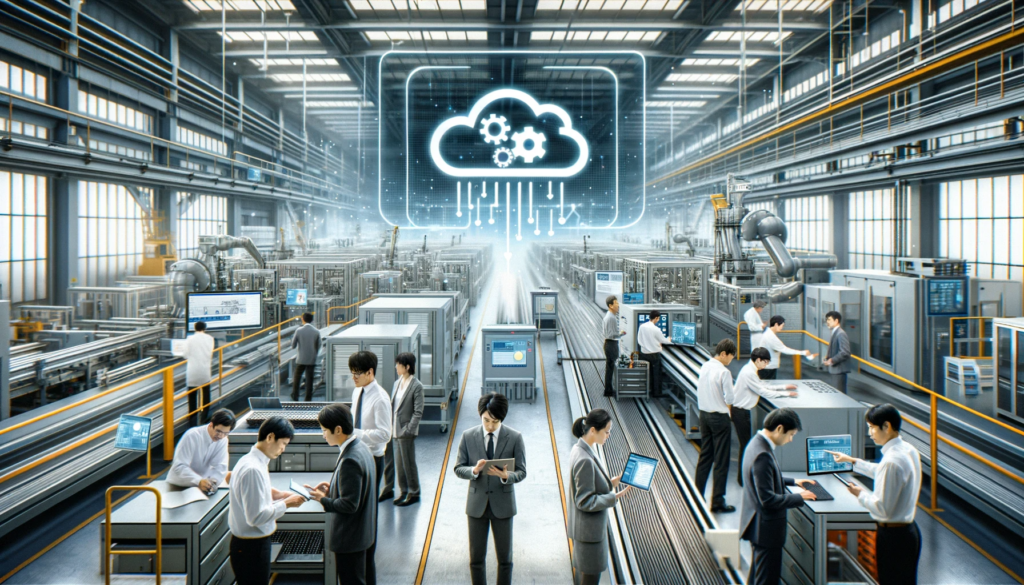
どのようなデータを取得するかについては、システム選定や導入の際にも議論されていることと思いますが、実際にデータ取得する際のポイントとしては、(1)データ取得の粒度(単位)、(2)データ取得の軸、というデータ取得そのものに関する箇所が2点、そしてそれらを容易に実現できる「専用のシステム」の3点になります。
データ取得の単位
例えば1つの作業工程に費やす時間を分析したい場合、時間よりも分単位で、分単位よりも秒単位で取得したほうが後で詳細に分析できるので、細かい単位でデータ取得したほうが良いのは明らかです。ただし、細かく取りすぎることで作業効率が落ちてしまっては元も子もありません。後からデータを取ることはできないのでできるだけ詳細なデータを取るようにしつつも、本当にそのデータ粒度が必要かどうかをしっかり設計しなければなりません。
データ取得の軸
あとでデータ分析する際に、どういった軸で分析したいかを設計します。例えば、作業担当者ごとの作業効率を分析したい場合には、担当者ごとにデータを取得する必要があります。不良の分析であれば、不良理由や不良個数などのデータを取得する必要があります。もし取得していない場合はせっかくのデータが無駄になってしまうので、データ取得にあたっては、どのような軸で集計・分析したいのかを明確にしておく必要があります。
データ取得は専用のシステムを利用する
ここで言う「専用のシステム」とは、製造業DXを目的として作られているシステムを指します。
現在においても、紙ベースの日報を多く目にします。紙への記入は一見楽かもしれませんが、Excel転記が必要で二度手間になります。専用のシステムであれば、現場で入力するだけで済みます。紙からの以降は抵抗感もあるかもしれませんが、専用のシステムですので、いままでには無かった以下のようなメリットも得られます。
- 使いやすい:入力しやすいUI(ユーザインタフェース)やUX(ユーザエクスペリエンス)になっている
- 多角的なデータの取得:いままで取得できていなかった粒度や軸でのデータ取得が可能
- リアルタイム性:データがリアルタイムで集計され、生産性や遅れが可視化される
データの取得においても、システムの活用がポイントになってきます。
ステップ⑤ データを正しく分析する
取得したデータを分析することで、定量的に課題を発見することができます。しかし、データ分析といっても簡単なことではなく、それなりのノウハウが必要になります。データ分析のポイントとして、(1)データ分析の軸、(2)データ分析ツール、の2点を解説していきます。
データ分析の軸
考えられるデータ分析の軸としては以下のような軸があり、これらを多角的に見ていくことで、何が課題なのかが見えてきます。
- 品目
- 工程
- 作業者
- 時間
- 設備
- 作業区
一方で、データアナリストというデータ分析の専門領域もあるように、経験がないとデータ分析は難しいものです。現場を熟知している人であればある程度の見当はつけられるので、まずは本やインターネットの情報を頼りに分析を進めてみましょう。それでも難しい場合は、データ分析の専門家に相談することも一つの方法です。
勘や経験に頼るのではなく、定量的に明示することで、関係者全員に納得感が生まれます。
データ分析ツール
データ分析ツールとしては主に以下の3つが挙げられます。
1. Excel
Excelでグラフを作成、分析する方法です。追加コストが不要なので一見良さそうに感じますが、Excelで多角的な分析を行おうとすると、新たな軸での分析の都度グラフを作成する手間が発生します。
また、分析結果のExcelファイルの共有が面倒であったり、Excelファイルを複数名で編集することで誤操作が発生するデメリットもあります。数回のみの分析であればExcelでも問題はありませんが、定常的に分析するようであれば、Excelの利用は避けたほうが無難でしょう。
2. BI(Business Intelligence)ツール
BIツールを使えば、Excelと違って瞬時に多角的な分析が可能になります。BIツールは非常にパワフルなツールです。
しかし、BIツールはあくまで分析目的のツールであるため、データの取得は別途ツールが必要になりますし、取得したデータを手作業もしくはAPI連携でBIツールに流し込む必要もあります。
API連携していればリアルタイム分析が可能になりますので、非常に強力な分析ができるでしょう。デメリットとしては、データ取得システムとBIツールの2つのコストが発生することと、どちらかの仕様変更の際にはAPI作り直しというメンテナンス作業(もしくはコスト)が発生する点です。
3. 専用のシステム
専用のシステムでは、製造業に適した分析環境が整っているため、データを入力した瞬間にすぐに分析結果が見れるようになります。具体的には、あらかじめダッシュボード内にサンプルがある、分析軸を選択肢から選ぶだけ、等、より短時間でデータ分析ができ、課題を明らかにすることが可能になります。
また、データ取得にも専用のシステムを利用することで、データ取得からデータ分析まで一気通貫で完結するため、専用のシステムの利用がベターであると言えます。
ステップ⑥ 改善策を検討し、改善活動を実施する
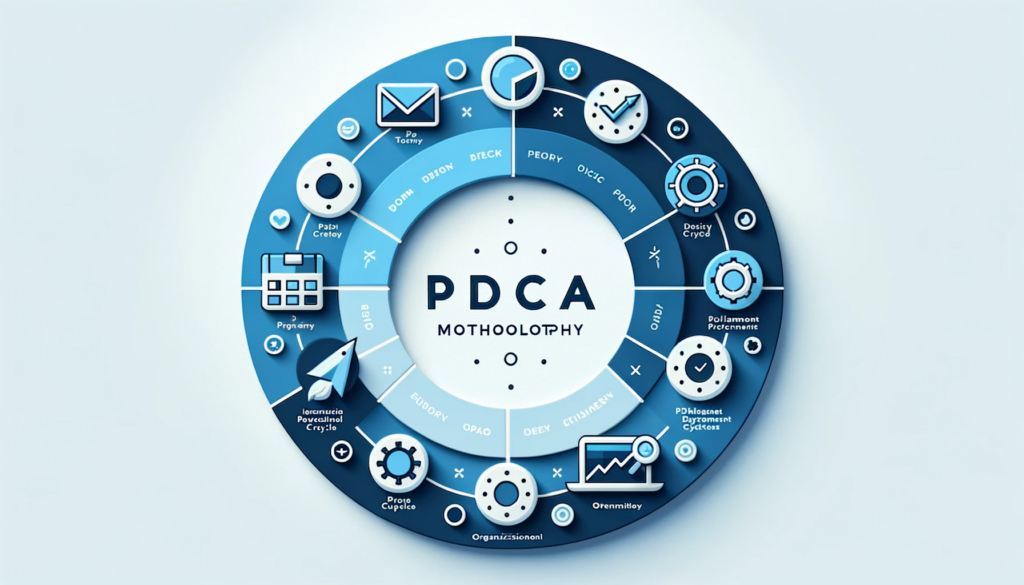
データ分析の結果、課題が明らかになってきました。ここからどのように改善を進めていくか、2つの方法を紹介します。
外部の専門家を頼る
改善策をひねり出すのは、簡単なことではありません。豊富な現場経験など製造現場に知見があること、他社事例を熟知していること、などが成功確率の高い改善策を出す要素になってきます。
製造業においては改善活動を専門にするコンサルタントも多く、時間をお金で買うという観点では、外部の専門家を頼ることは非常に有益でしょう。
注意点として、外部の専門家に依頼する場合は任せきりにせず、専門家が持つ知識や経験をできる限り吸収し、自社にノウハウを蓄積していくことで、次に活かせるようにすることが大事です。
現場を巻き込み、現場力を高める
改善活動で大切なのは、経営層や管理職だけで推進するのではなく、現場も一体となって改善していくことです。以下のような取り組みをしていくことになります。
1. 分析結果をオープンにし、現場に気づきを与える
いつでも分析結果にアクセスできるようにします。情報をオープンにすることで、経営層や管理職にやらされている感はなくなり、現場社員自らが考えるきっかけを作ることができます。課題発見や改善案創出はそれほど簡単ではありませんので焦りは禁物ですが、時間の経過とともに、徐々に改善案が出てくるようになります。
2. 改善に向けた意見を現場から引き出す、またそのような場を作る
現場メンバーが改善策を思いついたとして、それを発信できる環境が必要です。例えば改善案を投稿できるフォームを設けることで発信のハードルは下がるでしょうし、表彰制度を設けることで発信のモチベーションを上げることも考えられます。大企業だと改善専門の組織を設けるケースもあります。これによって改善案発信の重要性を社内に認知させることができます。
3. 現場社員が自ら行動を起こすきっかけをつくる
改善策が出ただけではまだ改善はされていませんので、改善策を実行に移す必要があります。
ここで経営層や管理職が一方的に指示を出してしまっては、現場力は高まりません。現場を信じ、一定の権限を付与し、改善策の実行を任せる。現場の成功体験を作ることで現場力が高まり、さらなる生産性向上につながるのです。
最後に ~覚悟を決める~
ここまで製造業のDXについて方法論やツール類について紹介してきましたが、最後に1つ、重要な要素があります。それは、覚悟です。
DX失敗の事例は山ほどありますが、よくある失敗の原因としては、ツール類や方法論が整っていたとしても、本気度の欠如や責任のなすりつけ合い、といったケースです。
一方成功しているケースでは、ツール類や方法論以上に、経営層やDX担当責任者のモチベーションが明らかに違います。「DXが失敗したら辞めます」とまで経営層に掛け合っている顧客責任者もいます。そこまでの覚悟があるからこそ、経営層も現場もその覚悟を受け止め、DXの取り組みが推進できるのだと思います。
覚悟を持つというのはとても勇気のいることですが、一方で、覚悟にはお金も時間もかかりませんので、勇気を持って最初の一歩を踏み出してみてはいかがでしょうか。
本記事がみなさまのDXの一助となれば幸いです。
Smart Craftで製造現場のDXを
始めよう!
「Smart Craft」は、これひとつで工場内のすべての業務プロセスをデジタル化できます。
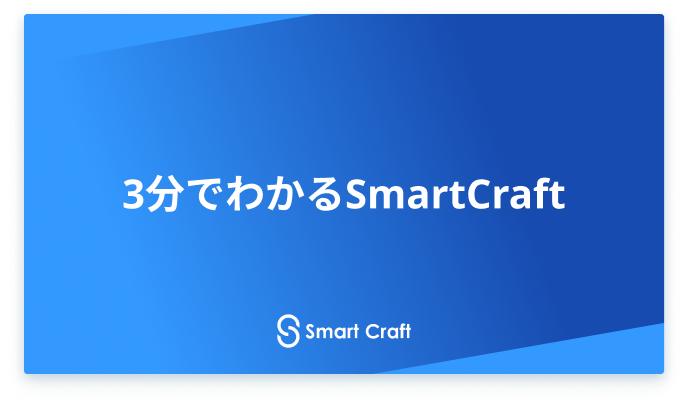
- Smart Craft でできること
- 導入企業の活用事例
- ご利用料金
- 導入の流れ