製造業における品質向上とは?具体的手法や成功事例を紹介
製造業を取り巻く環境は急速に変化しています。競争の激化、顧客ニーズの多様化、そして技術革新のスピードアップ。このような状況下で、高品質な製品を安定的に供給し続けることは、製造業にとって生命線とも言える重要な課題です。
しかし、品質向上の取り組みは一朝一夕で成果を出せるものではありません。現場の地道な努力の積み重ね、トップのリーダーシップ、そしてデジタル技術の活用が不可欠です。
この記事では、「製造業の品質向上」をテーマに、具体的な手法や成功事例、克服すべき課題について幅広く解説します。品質改善の取り組みを進めている方や、これから始めようとしている方は、ぜひ参考にしてください。
また、弊社では製造現場の業務効率化と品質向上を支援するクラウドサービス「Smart Craft」を提供しています。詳しくは資料で紹介しています。⇒資料のダウンロードはこちら
目次
製造業における品質向上の重要性
なぜ品質向上に取り組むべきか
激しい競争の中で市場優位性を確立するためには、品質向上への積極的な取り組みが不可欠です。情報通信技術の発達により、世界中の情報がつながり、顧客の製品に対する知識や要求水準は大きく高まっています。このような環境下で、顧客のニーズに迅速に対応し、高品質な製品を安定的に供給することが企業の生命線と言えるでしょう。
また、品質不良は企業イメージに甚大な損害を与え、ブランド価値を損なうリスクがあります。テレビや新聞に加え、ソーシャルメディアの発達により、品質トラブルは瞬く間に世界中に広まります。一度失った信頼を取り戻すのは容易ではありません。品質の維持・向上は、企業の存続と発展に直結する重要な経営課題です。
品質向上がもたらすメリット
品質向上への取り組みにより得られるメリットは多岐にわたります。
まず、顧客満足度の向上です。高品質な製品は顧客のニーズや期待に応え、使用者に良好な体験を提供します。満足度の高い顧客はリピート購入や口コミの広がりにつながります。顧客との長期的な信頼関係を構築する上で、品質は最も重要な要素の一つです。
次に、コストの削減です。品質の悪い製品は廃棄ロスやクレーム対応、リコールなど多大なコストを生みます。また、手直しや検査の工数増加が生産効率を低下させる要因にもなります。品質を高めて不良品を出さないことは、コスト構造の改善につながるのです。
さらに、従業員のモチベーション向上です。高品質な製品を生み出すことは、現場の従業員にとって大きな誇りとやりがいにつながります。品質向上への挑戦は問題解決力や改善意識を高め、個人と組織の成長を促す原動力となります。
そして、品質は企業の信頼と評判を左右する重要な要素です。高品質な製品を安定的に提供し続けることはブランドイメージの向上につながり、新規顧客の獲得や新市場の開拓にも寄与します。長期的に見ても、品質を軸とした経営は企業の持続的な発展を支える基盤となるでしょう。
品質向上の基本概念
品質向上に取り組む前に、いくつかの基本的な概念を理解しておく必要があります。ここでは、品質管理と品質保証の違い、QCDと品質の関係、工程管理と品質の関係について説明します。
品質管理と品質保証の違い
まず、「品質管理」と「品質保証」の違いを明確にしておきましょう。品質管理とは、製品やサービスの品質を一定の水準に保ち、顧客満足を向上させるための活動の総称です。具体的には、品質目標の設定、品質データの収集・分析、工程の監視と改善などが含まれます。
一方、品質保証とは、顧客に提供する製品やサービスの品質を保証するための活動を指します。そのためには、設計段階からの品質作り込み、サプライチェーンの管理、品質監査の実施など、品質に関わる全ての活動をマネジメントする必要があります。
つまり、品質管理が品質の維持・改善に直接的に取り組む活動であるのに対し、品質保証はその活動を含めた品質マネジメントシステム全体をカバーする概念と言えるでしょう。
関連記事:
品質保証と品質管理の違いとは?仕事内容、連携のポイント
QCDと品質の関係
製造業では、QCD(Quality:品質、Cost:コスト、Delivery:納期)のバランスを取ることが重要だと言われます。この3つはすべて顧客満足に直結する重要な要素です。品質を上げようとすれば、コストや納期に影響が出る可能性があります。逆に、コストを下げようとすれば、品質が犠牲になりがちです。
しかし、見方を変えれば、品質の高さこそがコストダウンと短納期を実現する鍵と言えます。不良品の発生を抑え、手戻りを減らすことは、無駄なコストの削減につながります。また、安定した品質の製品を効率的に生産できれば、リードタイムの短縮が可能になります。
品質の追求はQCDの達成を可能にする基盤です。品質を軸にコストと納期のバランスを取ることが重要です。
工程管理と品質の関係
品質は工程で作り込まれます。原材料の段階から加工、組立、検査、出荷に至るまでの一連のプロセスにおいて、製品の品質が決定されます。
そのため、品質向上には製造プロセス全体を適切に管理する「工程管理」の視点が欠かせません。工程管理の目的は、ムダやムラを排除し、一定の品質を確保しながら生産性を最大化することにあります。
具体的には、作業手順の標準化、工程能力の把握と改善、異常の早期発見と是正などが重要な活動となります。最終製品の品質を高めるためには、各工程の管理レベルを向上させ、品質の作り込みを徹底することが求められます。
▼関連記事
工程管理とは?製造業における重要性やメリット、効率化方法を紹介
以上のように、品質向上には品質管理と品質保証の両輪が必要であり、QCDのバランスと工程管理の視点が重要です。こうした基本的な考え方を踏まえ、具体的な改善に取り組んでいく必要があります。
品質向上のための具体的手法
品質向上を実現するためには、現場の状況を正確に把握し、問題点を特定し、効果的な改善を行うことが重要です。ここでは、品質向上のための具体的な手法として、現場の見える化、5S活動の徹底、4Mアプローチによる課題解決、標準化と属人化の排除について説明します。
現場の見える化
品質向上の第一歩は、現場の状況を「見える化」することです。製造プロセスにおけるさまざまな活動を可視化し、リアルタイムで把握することで、問題点や改善機会を特定しやすくなります。
IoTやAIを活用したデータ収集と分析は、見える化を強力に支援します。センサーやカメラなどで収集したデータをリアルタイムで処理・可視化することで、設備の稼働状況や製品の品質状態を常時モニタリングできます。異常があれば、その兆候を早期に検知し、迅速に対処することが可能になるでしょう。
見える化は単に情報を可視化するだけでなく、現場の従業員が自律的に問題解決や改善に取り組むための基盤にもなります。品質に関する情報を共有し、全員が同じ目標に向かって活動できる環境を作ることが重要です。
▼関連記事
工場の見える化とは?メリットや具体的な進め方を事例交え解説
現場の見える化は、品質改善の取り組みを支える重要な取り組みです。弊社ではこうしたニーズに応えるべく、製造現場の業務効率化と品質向上を支援するクラウドサービス「Smart Craft」を提供しています。
Smart Craftは、計画から実績収集、進捗管理、品質管理まで、製造現場のあらゆる情報をデジタルで一元管理。リアルタイムな見える化とデータ活用により、品質改善を強力に支援します。詳しくは資料で紹介していますので、ぜひご覧ください。
5S活動の徹底
品質向上には、現場の基本的な条件を整えることが欠かせません。その代表的な手法が「5S活動」です。5Sとは、整理・整頓・清掃・清潔・躾を指します。
- 整理:不要なものを取り除き、必要なものを適切に配置する
- 整頓:必要なものを使いやすく、わかりやすく配置する
- 清掃:設備や環境を清潔に保ち、異常を発見しやすくする
- 清潔:整理・整頓・清掃を維持し、職場の衛生を保つ
- 躾:決められたルールを守り、美しい職場を作る習慣をつける
5S活動を徹底することで、ムダやムラを排除し、品質ロスを削減できます。また、異常や不具合を発見しやすい環境を整えることで、問題の早期発見と是正につながります。5Sは、品質改善の土台となる活動と言えるでしょう。
4Mアプローチによる課題解決
品質問題の原因を突き止め、再発を防止するためには、体系的なアプローチが有効です。代表的な手法が「4Mアプローチ」です。4Mとは、Man(人)、Machine(機械)、Material(材料)、Method(方法)を指します。
品質問題が発生した際、この4つの視点から原因を追究します。作業者の技量や意識に問題はないか(Man)、設備の条件や性能に問題はないか(Machine)、原材料の品質や特性に問題はないか(Material)、作業手順や条件に問題はないか(Method)といった具合です。
4Mを切り口に、品質に関わるあらゆる要因を検証することで、問題の原因を特定しやすくなります。さらに、特定した原因に対する対策を立案・実行することで、その効果が得られやすくなります。この一連のプロセスを確実に回すことが、品質問題の真の解決と再発防止につながります。
標準化と属人化の排除
品質のバラつきを抑え、安定的に高品質な製品を生み出すためには、「標準化」が重要なカギとなります。手順やプロセスを標準化することで、作業のバラつきを抑え、ミスや不良の発生を防ぐことができます。
特に、熟練者の技能をマニュアル化し、後進に伝承することは品質の維持・向上に欠かせません。暗黙知を形式知化し、「属人化」を排除することで、組織としての品質管理力を高めることができます。
また、多能工化を進めることも重要です。特定の作業者しかできない仕事をなくし、柔軟な人員配置を可能にすることで、品質と生産性の両立を図ることができるでしょう。
以上のように、現場の見える化、5S活動、4Mアプローチ、標準化は、品質向上のための強力な手法となります。ただし、これらの手法を形骸化させることなく、確実に成果につなげるためには、いくつかのポイントを押さえておく必要があります。
品質向上の取り組みを成功に導くポイント
品質向上の手法を導入しても、実際に成果を出すには困難が伴うこともあります。ここでは、品質向上の取り組みを成功に導くためのポイントとして、トップのリーダーシップと現場の巻き込み、PDCAサイクルによる継続的改善、エンジニアリングチェーンとサプライチェーンの連携強化、品質データの一元管理とトレーサビリティ向上について説明します。
トップのリーダーシップと現場の巻き込み
品質向上の取り組みを成功させるためには、トップのリーダーシップが不可欠です。経営層が品質の重要性を認識し、強いコミットメントを示すことで、組織全体の意識を高めることができます。
また、品質向上は現場の従業員一人ひとりの意識と行動なくしては実現できません。現場の巻き込みを図り、改善活動への主体的な参画を促すことが重要です。ボトムアップ型の小集団活動などを通じて、現場の知恵を引き出し、改善意欲を高めていくことが求められます。
トップダウンとボトムアップのバランスの取れたアプローチが、品質向上の推進力になるのです。
PDCAサイクルによる継続的改善
品質向上は一時的な取り組みでは実現できません。継続的な改善活動が欠かせません。そのためには、PDCA(Plan-Do-Check-Act)サイクルを回すことが重要です。
まず、改善計画を立て(Plan)、次にその計画を実行し(Do)、その結果を評価し(Check)、最後に更なる改善に反映させます(Act)。このサイクルを繰り返すことで、品質のレベルを段階的に引き上げていくことができます。
問題の発見と解決、改善の積み重ねには終わりがありません。PDCAを回し続けることが、品質向上の原動力となるのです。
エンジニアリングチェーンとサプライチェーンの連携強化
製品の品質は、開発・設計から製造、調達に至るプロセス全体で作り込まれます。それぞれのプロセスを担うエンジニアリングチェーンとサプライチェーンが密接に連携することが重要です。
設計段階での品質作り込みを徹底し、製造や調達での品質トラブルを未然に防ぐことが求められます。また、サプライヤーと協働し、原材料や部品の品質向上を図ることも欠かせません。
各プロセスが断絶することなく、一気通貫で品質を作り込むためには、部門間・企業間の垣根を越えた連携が鍵を握っているのです。
品質データの一元管理とトレーサビリティ向上
品質改善を効果的に進めるためには、品質に関するデータを一元的に管理し、活用することが重要です。
製造プロセスや製品の品質に関するさまざまなデータを統合的に管理することで、問題の早期発見や原因追究がしやすくなります。また、それらのデータを分析し、ボトルネックの特定や改善施策の立案にも役立てることができます。
さらに、原材料から最終製品までのトレーサビリティを確保することも重要です。問題が発生した際に迅速に原因を特定し、適切な対応を取ることができます。リコールなどの事後対応のスピードと精度を高めることにもつながります。
品質データの一元管理とトレーサビリティの向上は、品質マネジメントシステムの強化に欠かせない要素です。
▼関連記事
トレーサビリティとは?意味や管理方法、主要技術について解説
以上、品質向上の取り組みを成功に導く4つのポイントについて説明してきました。これらをおさえつつ、自社の状況に合わせた改善活動を進めていくことが求められます。
品質向上の課題と克服策
品質向上への取り組みは、一朝一夕には成果が出ません。さまざまな障害や困難に直面することもあるでしょう。ここでは、品質向上を進める上での代表的な課題と、その克服策について説明します。
人手不足と属人化への対策
少子高齢化が進む中、製造業の現場では人手不足が深刻化しています。ベテラン従業員の退職により、技能の伝承が困難になっているケースも少なくありません。属人化した業務は、品質のバラつきを生みやすく、改善活動の障害にもなります。
この課題への対策としては、暗黙知の形式知化とITの活用が有効です。熟練者の技能をマニュアル化し、動画などを活用して後進に伝承することで、属人化リスクを低減できます。
また、IoTやAIを活用して自動化・省人化を進めることも重要です。人の手に頼る工程を減らし、品質の安定化とともに、人手不足の緩和にもつながるでしょう。
品質コストのジレンマ
品質向上には投資が必要です。検査の強化、設備の更新、教育・訓練の充実など、さまざまなコストがかかります。しかし、短期的な利益を追求して品質への投資を惜しむことは、長期的な競争力の低下を招きかねません。
品質コストのジレンマを克服するためには、品質の重要性を全社的に認識し、長期的な視点で経営判断を行うことが肝要です。品質への投資が、クレームの減少やブランドイメージの向上、ひいては売上や利益の拡大につながることを理解する必要があります。
また、品質コストを「予防コスト」「評価コスト」「失敗コスト」に分類して管理することも有効です。不良品の発生を防ぐための予防コストを適切にかけることで、失敗コストを削減します。このように、品質コストのバランスを取ることが重要です。
サプライヤー品質の改善
自社の品質はサプライヤーの品質に大きく影響を受けます。部品や原材料の品質不良は、最終製品の品質トラブルに直結します。サプライチェーン全体で品質を作り込むことが欠かせません。
サプライヤーの品質改善には、コミュニケーションと協働が不可欠です。サプライヤーと品質要求事項を共有し、改善に向けた取り組みを共に進めていくためには、信頼関係の構築が前提となります。
また、サプライヤーの品質管理体制を定期的に監査し、改善を促すことも重要です。自社の品質基準に適合した部品・原材料の安定調達を実現するには、サプライヤーの品質マネジメントシステムの向上が欠かせません。
デジタル化の遅れと対応
品質管理の分野では、データ活用の重要性が高まっています。しかし、多くの製造業では、まだアナログな管理体制が残っているのが実情です。紙の帳票や手作業での入力など、非効率な業務が品質改善の足かせになっているケースが少なくありません。
この課題への対応には、品質管理業務のデジタル化が欠かせません。現場の品質データをデジタルで収集・蓄積し、リアルタイムで可視化・分析するためのITインフラの整備と、それを活用する人材の育成が急務です。
品質管理のDX(デジタルトランスフォーメーション)を進め、データドリブンな品質改善を実現することが、競争力強化の鍵を握るでしょう。
製造現場のDXを進め、データドリブンな品質改善を実現するには、使いやすく導入しやすいシステムが不可欠です。弊社の「Smart Craft」は、現場の帳票をデジタル化し、スマートデバイスを活用した情報収集を可能にします。クラウドサービスとして提供されるため、初期費用を抑えてスモールスタートできるのも大きな特長です。Smart Craftを活用することで、どの企業でもスピーディーに品質管理のデジタル化を進められます。詳しくは資料で紹介しています。
以上、品質向上を進める上での代表的な課題と対策について見てきました。これらの課題を一つひとつ克服しながら、着実に品質改善を進めていくことが求められます。
品質向上の成功事例
品質改善への取り組みは、製造業の多くの企業で実践されています。ここでは、品質向上の成功事例として、自動車メーカーと電子部品メーカーの事例を紹介します。
自動車メーカーD社の不良率半減の取り組み
D社は世界的な自動車メーカーです。同社では、品質向上を経営の最重要課題の一つに位置づけ、全社を挙げた改善活動を展開しています。
同社が注力しているのが不良率の削減です。製造工程における不良発生状況を可視化し、問題の早期発見と是正を図っています。また、IoTを活用した設備の予知保全により、品質トラブルの未然防止にも取り組んでいます。
これらの活動の結果、D社では製造工程における不良率が3年間で50%削減されました。このような品質向上の取り組みが顧客満足度の向上やブランドイメージの強化につながっているようです。
電子部品メーカーE社の検査自動化
E社はスマートフォンなどに使われる電子部品を製造するメーカーです。同社の製品には非常に高い品質が要求されます。
E社では製品の検査工程の自動化に取り組み、大きな成果を上げています。従来は目視検査に頼っていた工程にAIを活用した自動検査システムを導入。高精度かつ高速な検査を実現し、検査工数を大幅に削減しました。
検査の自動化により、検査精度の向上と属人化の排除を同時に実現。品質の安定化とコスト削減を両立させることに成功しています。
以上、品質改善に取り組む企業の事例を紹介しました。業種や企業規模は異なりますが、いずれも品質向上を経営の重要課題と位置づけ、現場の改善活動を地道に積み重ねることで成果を上げています。
まとめ – 高品質な製品を生み出すための鍵
この記事では、製造業における品質向上について、その重要性から具体的な手法、成功事例まで幅広く解説してきました。
品質は製造業の競争力の源泉です。高品質な製品を安定的に供給することは、顧客満足の向上、ブランドイメージの強化、ひいては企業の持続的成長につながります。グローバルな競争が激化する中、品質の追求は製造業の生命線といっても過言ではありません。
品質向上への取り組みは容易ではありません。しかし、デジタル技術を効果的に活用することで、課題を克服し、着実に成果を上げることができます。当社では、製造業の品質改善をサポートするクラウドサービス「Smart Craft」を提供しています。
Smart Craftは、現場の見える化から品質管理、データ分析まで、品質向上に必要な機能を網羅しています。導入実績に基づくノウハウを活かし、お客様の品質改善の取り組みを強力に支援します。品質向上によって競争力を高めたいとお考えの製造業の皆様は、まずは資料請求からSmart Craftの導入を検討してみてください。
Smart Craftで製造現場のDXを
始めよう!
「Smart Craft」は、これひとつで工場内のすべての業務プロセスをデジタル化できます。
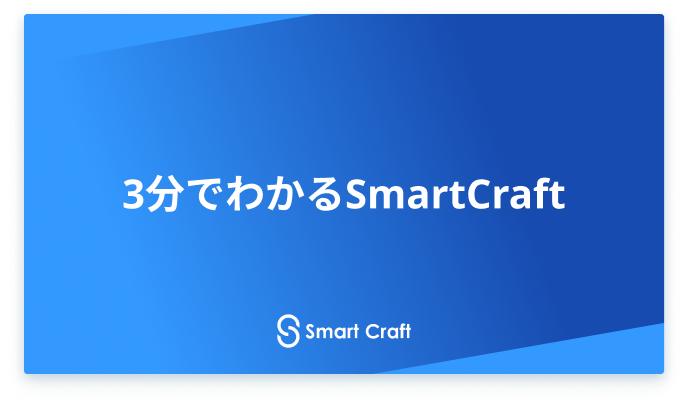
- Smart Craft でできること
- 導入企業の活用事例
- ご利用料金
- 導入の流れ