QC7つ道具を現場で活かす!品質改善のための実践的使い方
製造業にとって、高品質の製品を安定的に生産することは、顧客満足度の向上や企業の競争力強化に直結する重要な課題です。しかし、品質管理は言葉で言うほど簡単ではありません。原材料の品質のばらつきや、製造工程における様々な変動要因が、製品の品質に影響を及ぼすためです。
こうした品質のばらつきや不良品の発生を防ぐためには、製造現場で発生している問題を早期に発見し、その原因を究明して適切な対策を打つことが不可欠です。そのためのデータ分析や問題解決の手法として、古くから製造業で活用されているのが「QC7つ道具」です。
このQC7つ道具を使いこなすことで、品質に関するデータを「集める」「整理する」「可視化する」「解析する」というサイクルを回し、問題の真因を特定して品質改善に役立てることができます。
この記事では、QC7つ道具の概要や活用場面、各手法の具体的な使い方、活用事例などを解説し、製造現場の品質管理担当者はもちろん、品質改善に関わる全ての方に役立つ情報をお届けします。
また、弊社ではQC7つ道具をはじめとした品質管理手法をデジタル化し、データ活用を促進するクラウドサービス「Smart Craft」を提供しています。詳しくは資料で紹介しています。⇒資料のダウンロードはこちら
目次
QC7つ道具の概要
QC7つ道具とは何か
QC7つ道具とは、品質管理(Quality Control)において、データに基づく問題解決を行うための7種類の手法・ツールの総称です。QCサークル活動などの小集団改善活動で使われることが多いですが、問題解決の基本的な手法であるため、現場の作業者も含めた誰もが活用できるのが特徴です。
QC7つ道具を活用するメリットには、以下のようなものがあります。
- 問題の原因を客観的事実(データ)に基づいて確認・追究できる
- 複雑な問題をビジュアル化して整理できる
- 全員が納得できる形で問題点を共有できる
- 改善施策の効果をデータで確認できる
つまり、QC7つ道具は、製造現場の品質改善を感覚や経験則だけに頼るのではなく、データと論理に基づいて進めるためのものだと言えます。
QC7つ道具の目的と活用場面
QC7つ道具は、品質管理の様々な場面で活用されますが、主に以下のような目的で用いられます。
(1)問題の可視化と原因の追究
品質トラブルの発生状況や傾向をデータの形で可視化し、真の原因を掘り下げて追究する。
(2)工程の安定性の評価と改善
製造工程がどの程度安定しているかを定量的に評価し、ばらつきの原因を取り除く。
(3)検査データの解析と活用
全数検査や抜取検査で得られたデータを解析して、品質の改善や検査方式の最適化に役立てる。
このように、QC7つ道具は、製造現場で日常的に発生する品質問題の解決に役立つツールですが、最近では製造業に限らず、サービス業やソフトウェア開発の分野でも品質改善のために活用されるようになってきています。
QC7つ道具を活用する際のポイント
QC7つ道具を活用して品質改善を進める際は、以下のようなポイントを押さえておくことが重要です。
(1)目的を明確にする
漠然とデータを集めるのではなく、「何のために、どんな問題を解決するのか」という目的を明確にしてからQC7つ道具を選ぶ。
(2)現場の知恵を活かす
改善提案は現場の作業者から出てくることが多いため、現場の声に耳を傾け、QC7つ道具を使った分析のプロセスにも巻き込む。
(3)適切なツールを使い分ける
QC7つ道具にはそれぞれ得意な分析や状況があるため、目的に合わせて適切なツールを選択し、組み合わせて使う。
(4)継続的に改善サイクルを回す
1回限りの分析で終わらせず、QC7つ道具を使った問題解決のサイクルを継続的に回し、組織の問題解決力を高めていく。
以上のように、QC7つ道具はデータに基づく品質改善のために有効なツールです。形骸化させることなく、現場に根付かせながら活用していくことが重要となります。
また、弊社ではQC7つ道具をはじめとした品質管理手法をデジタル化し、データ活用を促進するクラウドサービス「Smart Craft」を提供しています。詳しくは資料からご確認ください。⇒資料のダウンロードはこちら
Smart Craftで製造現場のDXを
始めよう!
「Smart Craft」は、これひとつで工場内のすべての業務プロセスをデジタル化できます。
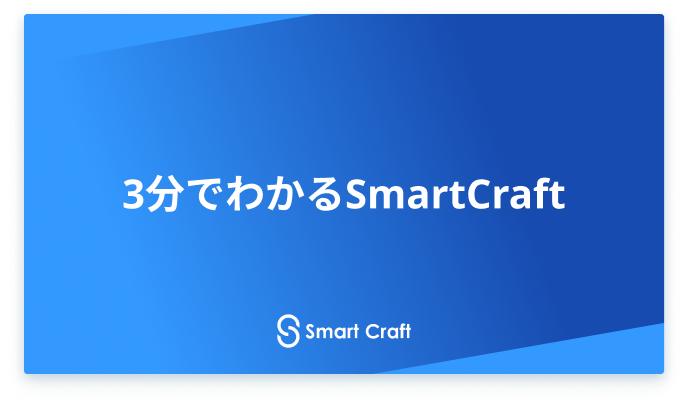
- Smart Craft でできること
- 導入企業の活用事例
- ご利用料金
- 導入の流れ
QC7つ道具の種類と使い方
QC7つ道具とは、1960年代、日本科学技術連盟を中心に、米国から導入された統計学的手法から品質管理に役立つ7つの代表的なものがまとめられ、その後、石川馨博士らによって体系化された品質管理手法です。次の7つのツールから構成されています。
以下では、QC7つ道具の種類と使い方について具体的に解説します。
パレート図 – 重点改善項目の可視化と絞り込み
パレート図は、品質不良の発生件数や不良率など、複数の問題項目について、その発生頻度や影響度を棒グラフと折れ線グラフで表した図です。問題項目を発生頻度の多い順に並べることで、重点的に改善すべき項目を可視化し、改善の優先順位を決める際に役立ちます。
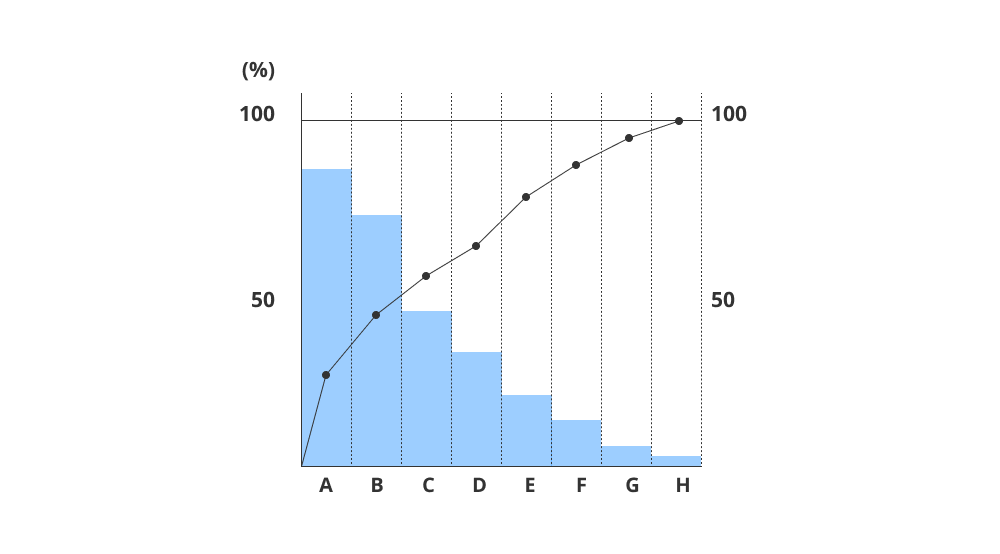
パレート図の特徴は、「バイタルフューと多数のトリビアルフュー」の法則を視覚的に表現できる点にあります。つまり、発生頻度全体の大半(80%程度)を占める少数(20%程度)の重要項目(バイタルフュー)と、残りの多数の些細な項目(トリビアルフュー)を見分けられます。
パレート図の具体的な作成手順は以下の通りです。
(1)改善したい問題(品質不良など)に関する項目とその発生度数をデータ化する
(2)項目を発生度数の多い順に並べ替え、棒グラフを作成する
(3)各項目の累積構成比を算出し、折れ線グラフで表す
(4)累積構成比が80%程度となる項目数を目安に、重点改善項目を絞り込む
パレート図を用いることで、「どの不良項目を重点的に改善するのが効果的か?」といった問題解決の方向性を導き出せます。ただし、パレート図はあくまで現象面の特徴を可視化したものであり、その原因を掘り下げるためには、次に説明する特性要因図などの手法を組み合わせる必要があります。
特性要因図 – 問題の要因を系統的に整理・分析
特性要因図は、品質問題の原因を系統的に整理し、真因を追究するためのツールです。QC7つ道具の中で最も使用頻度が高いと言われています。
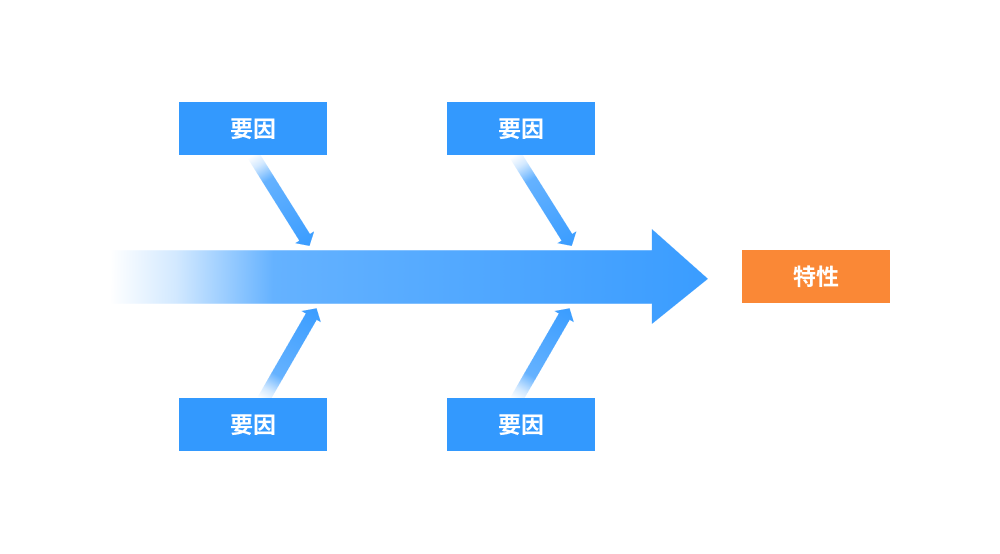
特性要因図では、解決したい問題(特性)を図の頭部(右端)に書き、問題の原因と考えられる要因を魚の骨のように左側に派生させていきます。主要因は大骨(大きな骨)に、それをさらに細分化した要因は中骨、小骨に書き込んでいくことで、問題の全体像を俯瞰しながら、真因に迫っていきます。
主な用途としては、以下のような場面が挙げられます。
- 品質トラブルの原因を洗い出したい場合
- 工程能力の改善要因を抽出したい場合
- 設計品質を向上させるための着眼点を整理したい場合
特性要因図の主要因(大骨)は、製造業であれば「4M」と呼ばれる、人(Man)、機械(Machine)、材料(Material)、方法(Method)で分類するのが一般的です。
特性要因図の作成手順は以下の通りです。
(1)問題点(特性)を明確にし、図の頭部(右端)に記入する
(2)特性に対する主要因を大骨として書き出す(4Mなど)
(3)各主要因に対する具体的な要因を中骨、小骨に展開していく
(4)各要因の関連づけを行い、重要な要因に印をつける
特性要因図を作る際のコツは、メンバー全員で自由に要因を出し合うこと(ブレインストーミング)、思いつく限り細かな要因まで書き出すこと、因果関係を意識して要因を整理することなどが挙げられます。
また、特性要因図で抽出された主要因をもとに、さらにデータ解析を行って真因を特定していくこともよく行われます。特性要因図とその他のQC7つ道具を有機的に組み合わせることで、品質問題の本質により迫りやすくなります。
グラフ – データの傾向や比率を視覚的に把握
グラフは、データの傾向や比率を視覚的に表現するための基本的なツールです。QC7つ道具の中でも、最も幅広く活用されています。代表的なグラフとしては、以下のようなものがあります。
- 折れ線グラフ:時間経過に伴うデータの変化を表現するのに適している
- 棒グラフ:項目間の量的な比較を表現するのに適している
- 円グラフ:全体に対する各項目の構成比を表現するのに適している
- レーダーチャート:複数の評価項目のバランスを表現するのに適している
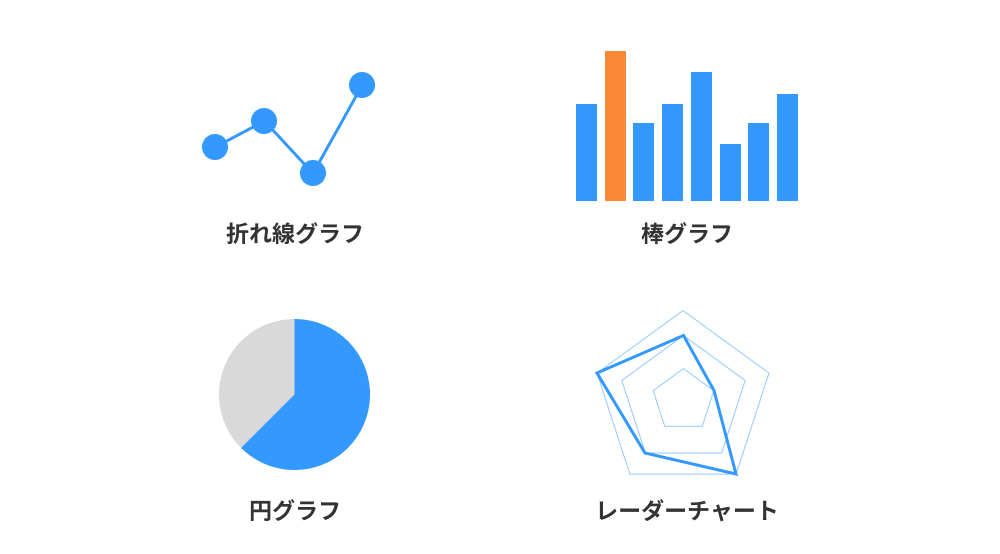
品質管理の場面では、例えば以下のようなデータをグラフ化することで、問題点や改善の手がかりを見出すことができます。
- 日別・週別・月別の不良率の推移(折れ線グラフ)
- 工程別の不良発生件数の比較(棒グラフ)
- 不良原因の内訳(円グラフ)
- 製品の性能評価結果(レーダーチャート)
グラフを作成する際は、目的に応じて適切な種類のグラフを選択することが重要です。また、グラフのタイトルや軸ラベルを明確にし、必要に応じて補助線を引くなど、わかりやすくなるよう工夫しましょう。
グラフから問題点や改善のヒントを読み取るためには、以下のような点に着目すると良いでしょう。
- 全体的な傾向(増加、減少、一定など)
- 特異点(突出して高い、低い値)
- 周期性(繁忙期、閑散期など)
- 相関性(2つの項目の連動性)
ただし、グラフはあくまでデータを可視化したものであり、それ自体が問題解決につながるわけではありません。グラフから読み取った特徴をもとに、他のQC7つ道具も活用しながら、さらなる分析を進めていくことが大切です。
ヒストグラム – データの分布状態やばらつきを把握
ヒストグラムは、測定値などの連続したデータを、いくつかの区間に分けて度数分布を表した図です。縦軸に度数(各区間に入るデータの個数)、横軸にデータの範囲をとり、各区間の度数に対応した高さの長方形(度数棒)を並べて作成します。
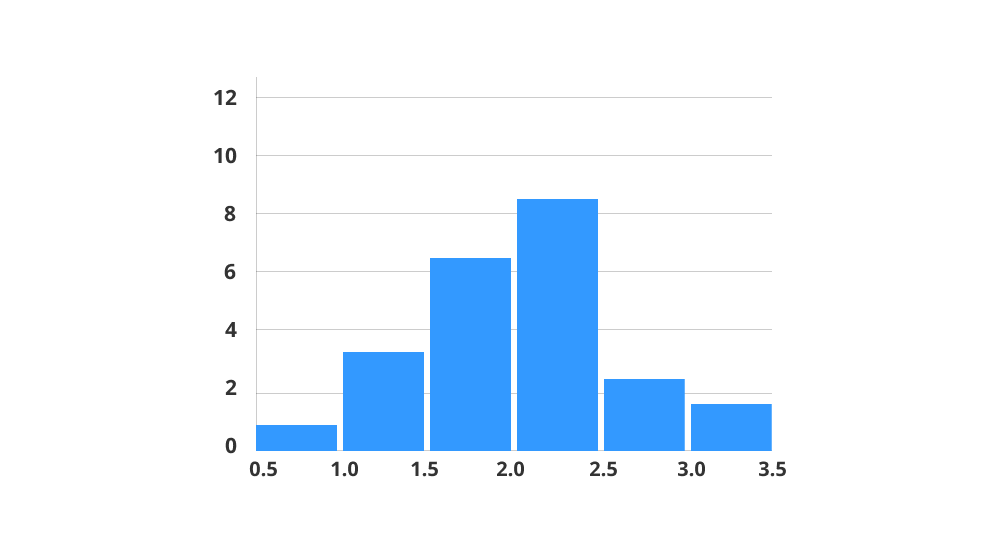
ヒストグラムを用いることで、以下のようなデータの特徴を視覚的に把握できます。
- データのばらつきの程度(分布の幅)
- データの集中している範囲(山の位置)
- 規格からの外れ値の有無
品質管理では、例えば以下のような場面でヒストグラムが活用されます。
- 製品の寸法や重量のばらつきの確認
- 工程能力指数(Cp、Cpk)の算出
- 検査データの分布状態の把握
ヒストグラムから読み取れる分布の特徴としては、以下のようなパターンがあります。
- 左右対称の山型(正規分布型)
- 左右どちらかに裾野が長い(歪んだ分布)
- 山が2つ以上ある(複数の分布が混在)
- 山が平坦で幅広い(ばらつきが大きい)
これらの特徴は、製造工程の状態を反映していることが多いため、ヒストグラムを詳しく分析することで、品質のばらつきの原因を追究する手がかりが得られます。
例えば、歪んだ分布になっている場合は、特定の要因が影響している可能性があります。複数の山がある場合は、複数の母集団(材料、機械、作業者など)が混在している可能性があります。
ヒストグラムを作成・分析する際の注意点としては、以下のような点が挙げられます。
- 区間の幅を適切に設定する(目安は10~20区間)
- 区間の幅を変えてみて、分布の特徴が変わらないことを確認する
- 必要に応じて、階級値(各区間の中央値)を用いて分析する
- 規格範囲や目標値を明示して、現状とのギャップを確認する
ヒストグラムは、他のQC7つ道具と組み合わせることで、さらに有効な分析ができます。例えば、層別した項目ごとにヒストグラムを作成し比較することで、品質特性に影響を及ぼす要因を特定することができます。
散布図 – 2つの変数の相関関係を分析
散布図は、2つの数値データの組み合わせを平面上の点で表現したグラフです。横軸と縦軸にそれぞれの変数をとり、対応する値の組を座標とする点をプロットすることで、2つの変数の間に関連性があるかどうかを視覚的に判断できます。
品質管理の場面では、例えば以下のような変数の組み合わせで散布図が用いられます。
- 原材料の特性値と製品の品質特性
- 製造条件(温度、圧力など)と不良率
- 作業者の習熟度と作業時間
散布図上の点の分布パターンを見ることで、以下のような関係性を読み取ることができます。
- 正の相関:右上がりの直線状に点が分布する(例:原材料の硬度が高いほど、製品の強度が高い)
- 負の相関:右下がりの直線状に点が分布する(例:温度が高いほど、不良率が低い)
- 相関なし:点が散らばっていて、特定の傾向が見られない
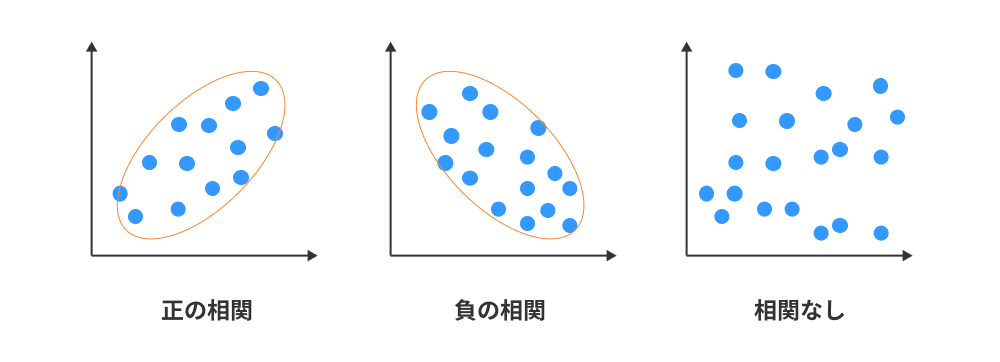
ただし、散布図で相関が見られたからといって、必ずしも因果関係があるとは限りません。見かけ上の相関の背後に、他の要因が潜んでいる可能性もあります。そのため、散布図で相関が見られた場合は、他の要因も考慮に入れて、慎重に解釈する必要があります。
散布図を作成する際の注意点としては、以下のような点が挙げられます。
- 両軸のスケールを適切に設定し、点が見やすいようにする
- 点が重なっている場合は、少しずらしてプロットする
- 外れ値(他の点から大きく離れた値)の存在に注意する
- 必要に応じて、回帰直線(点の分布に最も近い直線)を引く
散布図は、他のQC7つ道具と組み合わせることで、より深い洞察を得ることができます。例えば、特性要因図で抽出した複数の要因について、それぞれ散布図を作成し、品質特性との関連性を比較することで、真の原因により近づくことができるでしょう。
管理図 – 工程の安定性をモニタリング
管理図は、製造工程などの品質特性値を時系列的にプロットしたグラフで、工程の安定性を監視し、異常の兆候を検知するために用いられます。
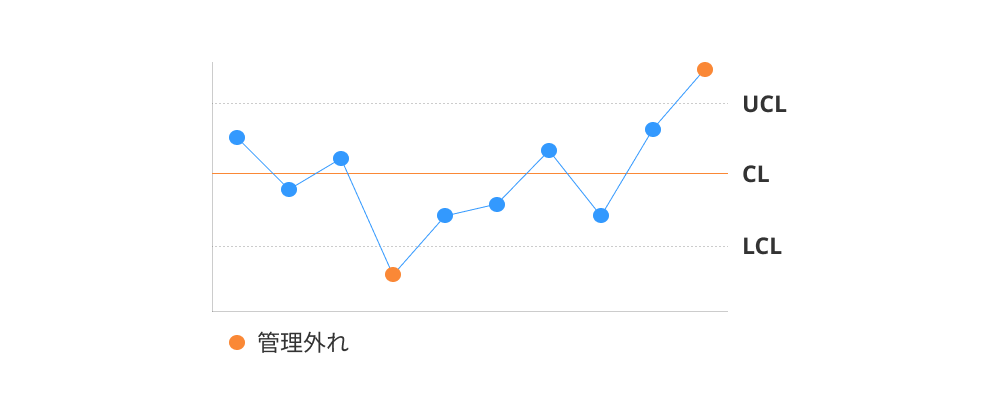
管理図の縦軸は品質特性の測定値(例:寸法、強度など)、横軸は時間経過(例:製造順、ロット番号など)を表します。中央線(CL)は品質特性の平均値を、上方管理限界線(UCL)と下方管理限界線(LCL)は、それぞれ平均値から上下3σ(標準偏差の3倍)離れた位置に引かれます。
管理図には、品質特性の種類や用途に応じて、以下のような種類があります。
- x-R管理図:連続データを扱う場合に用いる基本的な管理図
- x-s管理図:サンプルサイズが大きい場合に用いる管理図
- p管理図:不良率など、割合データを扱う場合に用いる管理図
- c管理図:欠点数など、計数値データを扱う場合に用いる管理図
管理図を運用する際は、定期的(例:1時間ごと、1日1回など)にサンプルを抜き取り、品質特性値を測定・プロットします。そして、以下のような異常パターンがないかチェックします。
- 管理限界線を超えている点がある
- 連続して7点以上、平均値の片側に偏っている
- 上昇・下降などの特定の傾向が見られる
- 周期的な波動が見られる
これらの異常パターンが見つかった場合は、工程に何らかの特別な原因(設備の故障、材料の変更など)が発生している可能性が高いため、速やかに原因を究明し、対策を講じる必要があります。
一方、管理限界線内で推移している状態(管理状態)は、工程が安定していることを意味します。この状態を維持・改善していくことが、品質管理における目標となります。
管理図の活用のポイントは、以下のようなことが挙げられます。
- 管理限界線の設定は、過去のデータをもとに適切に行う
- 異常点が出たらすぐに現場に行き、原因を調査する
- 管理図をチームで共有し、問題意識を持って見守る
- 工程改善の効果を管理図で確認する
管理図は、品質のばらつきを定量的に捉え、異常の兆候を早期に発見するための有効なツールです。他のQC7つ道具と組み合わせながら活用することで、製造工程の安定化と継続的改善に大きく寄与するでしょう。
チェックシート – データ収集や点検漏れ防止に活用
チェックシートは、データ収集や点検の際に用いる、項目をリスト化したシートのことです。手書きの場合もありますが、最近はスマートフォンやタブレット端末などを用いて電子的に作成・運用されることも多くなっています。
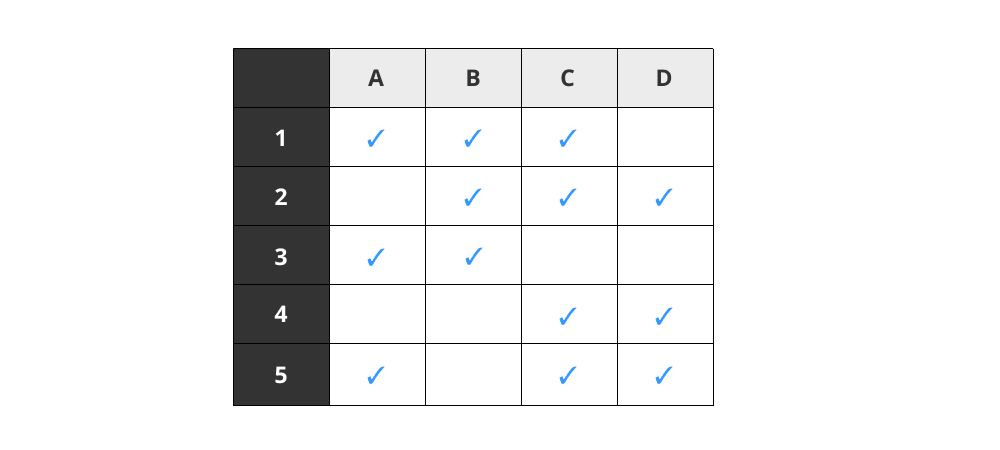
チェックシートの主な用途は、以下の2つに大別できます。
(1)データ収集用
品質管理に必要なデータ(不良数、欠陥数、測定値など)を、もれなく効率的に収集するために用います。データ収集用のチェックシートを作成する際は、以下のような点に留意します。
- 収集するデータの種類や単位を明確にする
- データの取りやすさを考慮してレイアウトを工夫する
- 必要に応じて層別の項目(日付、ロットなど)を入れる
- 集計や入力がしやすいようにコード化する
(2)点検用
製造工程や製品の品質を維持するために、定期的に行う点検の際に用います。点検用のチェックシートを作成する際は、以下のような点に留意します。
- 点検項目を網羅的かつ具体的に記述する
- 点検基準(良否の判定基準)を明確にする
- 点検結果を記入しやすいようにレイアウトを工夫する
- 点検の手順や注意点を記載する
チェックシートを運用する際は、以下のようなことに気をつけると良いでしょう。
- 記入漏れ、記入ミスがないようにする
- データの信頼性を高めるために、複数人で確認する
- 定期的にチェックシートの内容を見直し、改善する
- チェックシートで収集したデータを、他のQC7つ道具で分析する
チェックシートは、一見地味で単純なツールですが、QC7つ道具の中でも特に基本的かつ重要な役割を果たしています。正確で豊富なデータがなければ、他のQC7つ道具も有効に機能しないからです。
品質管理の現場では、チェックシートをベースにPDCAサイクルを回すことが日常的に行われています。例えば、以下のようなサイクルです。
- Plan(計画):チェックシートの設計、運用方法の設定
- Do(実行):チェックシートを用いたデータ収集、点検の実施
- Check(評価):チェックシートのデータを分析、問題点の把握
- Act(改善):問題点をもとに、チェックシートの改善、工程の改善
このように、チェックシートは品質管理活動の土台となるツールであり、QC7つ道具の中核をなすと言えるでしょう。
QC7つ道具の活用事例 – 製造業での不良品削減の取り組み事例
A社は、電子部品の製造を行っている会社です。ある製品の不良率が高いという問題が発生したため、QC7つ道具を活用して不良削減に取り組むことにしました。
まず、不良の内容別の発生件数を、チェックシートとパレート図で整理しました。その結果、「基板の部品実装不良」が全体の約6割を占めていることがわかりました。そこで、この不良に焦点を絞って、特性要因図を作成し、原因を掘り下げました。
特性要因図では、「人」「機械」「材料」「方法」の4つの視点から、部品実装不良の原因を挙げていきました。チームのメンバーで議論を重ねた結果、「はんだ付け温度の設定が適切でない」「部品の位置ずれが発生している」という2つの有力な原因に絞り込まれました。
次に、この2つの原因について、ヒストグラムと散布図を用いて定量的な分析を行いました。その結果、以下のようなことがわかりました。
- はんだ付け温度は、設定範囲内におおむね収まっているが、ばらつきが大きい
- 部品の位置ずれは、特定の実装機で多発している
- はんだ付け温度と部品の位置ずれの間には、明確な相関は見られない
これらの分析結果から、はんだ付け温度のばらつきを抑えること、部品の位置ずれが発生しやすい実装機を調整することが、不良削減のポイントであると判断しました。
そこで、以下のような対策を実施しました。
- はんだ付け温度の管理基準を見直し、管理図を用いて日常的にモニタリングする
- 部品の位置ずれが多発している実装機について、センサーの位置や압力を調整する
- 作業者に対して、部品実装の手順や注意点を再教育する
これらの対策の効果を確認するために、チェックシートとパレート図で不良の発生状況を継続的に監視しました。その結果、「基板の部品実装不良」の割合が大幅に減少し、製品全体の不良率も目標値以下に低減することができました。
この事例から分かるQC7つ道具の活用のポイントは、次の通りです。
- QC7つ道具を状況に応じて使い分け、組み合わせることが重要
- 特性要因図で抽出した原因を、他のツールで定量的に検証することが有効
- 対策の効果は、必ず定量的なデータで確認し、フォローアップすることが大切
このように、QC7つ道具を活用することで、品質問題の原因を論理的に追究し、効果的な改善を進めることができるのです。
QC7つ道具を活用する4つのメリット
QC7つ道具を活用することには、多くのメリットがあります。以下に主な4つのメリットについてまとめました。
メリット1:問題解決のスピードアップ
QC7つ道具を活用することで、品質問題の解決を素早く進めることができます。その理由は以下の3つです。
(1)問題の全体像を俯瞰できる
QC7つ道具の多くは、データを可視化することで問題の全体像を明らかにします。例えば、パレート図で問題の優先順位が明確になったり、特性要因図で問題の構造が見えてきたりします。これにより、どこから手をつけるべきかが明らかになり、問題解決のための的確なアクションをとれるようになります。
(2)議論が活性化する
QC7つ道具を用いることで、メンバー間の議論が活性化しやすくなります。グラフや図を見ながら議論することで、人によって異なる意見や考えを平等に扱うことができ、建設的な議論が行われやすくなります。また、QC7つ道具のルールに則ってデータを可視化することで、メンバー間の認識のズレを防ぐこともできます。
(3)PDCAサイクルが回しやすくなる
QC7つ道具は、Plan(計画)、Do(実行)、Check(評価)、Act(改善)のPDCAサイクルと親和性が高いツールです。例えば、特性要因図で立てた対策案を実行し、その効果をヒストグラムや管理図で確認するといったように、QC7つ道具を用いることでPDCAサイクルをスムーズに回すことができます。
メリット2:データに基づく意思決定
QC7つ道具を活用することで、データに基づいた客観的な意思決定が可能になります。
品質管理の現場では、経験や勘に頼った属人的な判断が行われることがありますが、それには限界があります。品質問題の原因は複雑で多岐にわたるため、個人の経験だけでは見落としが生じる可能性が高いからです。
一方、QC7つ道具を用いれば、データを多面的に分析し、客観的な事実に基づいて判断することができます。例えば、散布図で2つの変数の関係性を定量的に把握したり、管理図で工程の異常を統計的に判断したりすることができます。
データに基づく意思決定は、以下のようなメリットがあります。
- 根拠が明確なため、説得力がある
- 人による判断のブレを防ぐことができる
- 問題の本質に迫ることができる
- 改善効果を定量的に評価できる
ただし、データを盲信するのは危険です。データの質や収集方法に問題がないか、データの解釈に恣意性がないかなどについても、常に注意を払う必要があります。その意味で、QC7つ道具を使いこなすには、科学的な思考力とデータへの謙虚さの両方が求められると言えるでしょう。
メリット3:改善活動の質の向上
QC7つ道具を活用することで、品質改善活動の質を高めることができます。
品質改善というと、日々の地道な活動の積み重ねをイメージする人も多いかもしれません。もちろん、そういった泥臭い努力は重要ですが、それだけでは大きな成果は望めません。品質改善活動を、より戦略的で効果的なものにするためには、科学的な手法やツールが必要不可欠です。
QC7つ道具は、まさにそのための切り札と言えます。現場の状況をデータで把握し、問題点を可視化し、改善の方向性を具体化する。そして、対策の効果を客観的に評価し、さらなる改善につなげる。こういった一連のプロセスを、QC7つ道具を用いて実践することで、品質改善活動の質を高めることができます。
例えば、ある自動車部品メーカーでは、QC7つ道具を活用した改善活動の結果、以下のような成果を上げたそうです。
- 不良率が3分の1に減少
- 工程の生産性が20%向上
- 品質コストが半減
- 現場の改善提案件数が倍増
このような成果は、QC7つ道具なしでは決して得られなかったでしょう。品質改善活動をより高いレベルに引き上げるために、QC7つ道具の活用は欠かせません。
メリット4:社員の問題解決力の向上
QC7つ道具を活用することで、社員の問題解決力を高めることができます。
前述の通り、QC7つ道具は、品質管理の専門家だけでなく、現場の担当者も使いこなすことができるツールです。現場の社員が、自分たちの手でデータを集め、分析し、改善策を立案する。そのような自律的な問題解決のプロセスを通じて、社員の問題解決力は確実に向上していきます。
QC7つ道具を使いこなすには、以下のような能力が必要とされます。
- データを正確に収集・記録する力
- データを多面的に分析・解釈する力
- 問題の原因を論理的に推察する力
- 改善策を創造的に発想する力
- 関係者を巻き込み、改善を推進する力
これらの能力は、品質管理に限らず、あらゆる仕事で求められる汎用的なスキルです。QC7つ道具を学ぶことで、社員はこれらのスキルを身につけ、品質改善だけでなく、日常の問題解決においても力を発揮できるようになります。
また、QC7つ道具の活用は、社員のモチベーションアップにもつながります。自分たちで問題解決できた経験は、大きな自信と達成感を与えてくれます。それが、品質改善へのさらなる意欲につながっていくのです。
品質改善は、一部の専門家だけの仕事ではありません。現場の社員一人ひとりが問題解決力を高め、主体的に改善活動に取り組むことで初めて、真の意味での品質経営が実現します。その意味で、QC7つ道具は品質改善の原動力である社員の育成に欠かせないツールだと言えるでしょう。
QC7つ道具を補完する手法 – 新QC7つ道具の紹介
新QC7つ道具とは
QC7つ道具は、主に数値データを扱う手法ですが、言語データを扱う手法も重要です。言語で表現された情報を整理・分析する手法として開発されたのが、「新QC7つ道具」(または「N7」)と呼ばれるツール群です。
新QC7つ道具は、1970年代後半に日本科学技術連盟(JUSE)により提唱されました。その目的は、QC7つ道具では対応しきれない、以下のような問題に対処することです。
- 顧客ニーズや社会動向など、数値化しにくい情報を扱う必要がある
- 問題が複雑で、原因と結果の関係が明確でない
- 改善のアイデアを出すために、発想を広げる必要がある
このような背景から生まれた新QC7つ道具は、以下の7つの手法で構成されています。
これらの手法は、いずれも言語データを図解化することで、情報を整理し、問題解決のためのアイデアを引き出すことを目的としています。以下、それぞれの手法について簡単に説明します。
親和図法、連関図法などの新QC7つ道具の概要
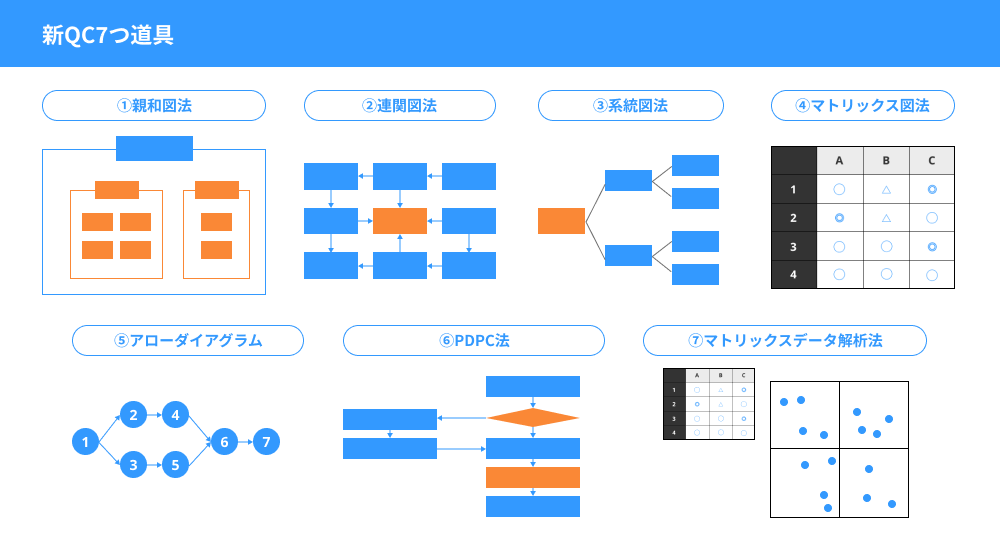
(1)親和図法
親和図法は、ブレインストーミングなどで出された多数のアイデアや意見を、その親和性(類似性)に従ってグループ化し、問題の構造を明らかにする手法です。複雑な問題を整理し、体系的に理解するのに役立ちます。
(2)連関図法
連関図法は、問題の原因と結果、目的と手段など、物事の相互関係を図解する手法です。矢印を用いて因果関係を表現することで、問題の全体像を俯瞰することができます。
(3)系統図法
系統図法は、目的を達成するための手段を、ツリー状の図で表現する手法です。大きな目的から、より具体的な手段へと段階的に展開していくことで、問題解決のためのアクションプランを立てることができます。
(4)マトリックス図法
マトリックス図法は、2つの要素を縦軸と横軸に配置し、その関係性を表現する手法です。例えば、要求品質と製品機能の関係を表すことで、設計の優先順位を決めるのに役立ちます。
(5)アローダイアグラム
アローダイアグラムは、プロジェクトなどの工程計画を、矢印を用いたネットワーク図で表現する手法です。各タスクの所要時間や先行関係を明確にすることで、スケジュール管理に役立ちます。
(6)PDPC法
PDPC法は、目標達成までのプロセスを、予想される問題と対策を織り込んで表現する手法です。起こり得る障害を事前に想定し、対策を立てておくことで、トラブルへの対応力を高めることができます。
(7)マトリックスデータ解析法
マトリックスデータ解析法は、新QC7つ道具の中で唯一、数値データを扱う手法です。多変量のデータを、行列の形で分析することで、データの背後にある構造を明らかにすることができます。
QC7つ道具と新QC7つ道具の使い分け
QC7つ道具と新QC7つ道具は、対象とするデータの種類が異なります。QC7つ道具が数値データを主に扱うのに対し、新QC7つ道具は言語データを主に扱います。そのため、問題の性質に応じて、2つのツール群を使い分ける必要があります。
一般的には、以下のような場合に、新QC7つ道具が有効だと考えられます。
- 顧客の声など、定性的なデータから課題を抽出する必要がある場合
- 問題の原因と結果の関係が複雑で、定量的な分析が難しい場合
- 改善のアイデアを出すために、発想を広げる必要がある場合
ただし、QC7つ道具と新QC7つ道具は、相互に補完的な関係にあります。例えば、特性要因図で抽出した問題の原因を、連関図法でより詳細に分析するといったように、両者を組み合わせることで、より効果的な問題解決が可能になります。
大切なのは、問題の性質や目的に応じて、適切なツールを選択し、柔軟に活用していくことです。QC7つ道具と新QC7つ道具のどちらか一方に偏るのではなく、両者の特徴を理解し、バランスよく使いこなすことが求められます。
さらに、これらの手法をデジタルツールを活用することで、より効率的かつ継続的な改善が可能になります。QC7つ道具をはじめとした品質管理手法をデジタル化し、データ活用を促進するクラウドサービス「Smart Craft」(スマートクラフト)の詳細についてはこちらの資料で紹介しています。⇒資料のダウンロードはこちら
Smart Craftで製造現場のDXを
始めよう!
「Smart Craft」は、これひとつで工場内のすべての業務プロセスをデジタル化できます。
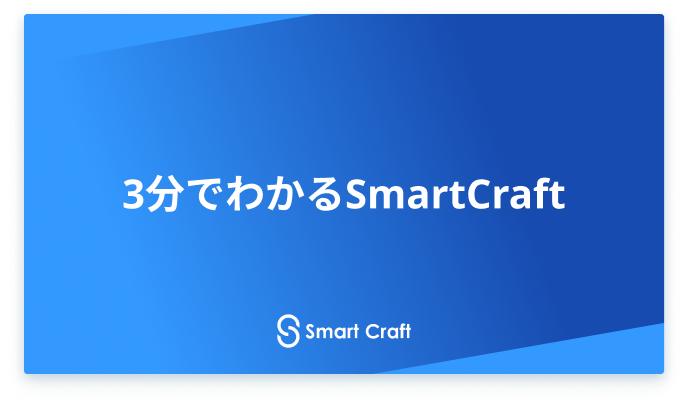
- Smart Craft でできること
- 導入企業の活用事例
- ご利用料金
- 導入の流れ
QC7つ道具を学ぶための方法
書籍やオンライン教材の活用
QC7つ道具を学ぶための方法の1つが、書籍やオンライン教材を活用することです。QC7つ道具に関する書籍は数多く出版されており、初心者向けのものから、より実践的な内容のものまで、レベルに応じた選択が可能です。
書籍のメリットは、体系的な知識が得られることです。QC7つ道具の基本的な考え方や、各手法の使い方を、順を追って学ぶことができます。また、事例を交えた説明も多いので、実際の活用イメージを持ちやすいというメリットもあります。
一方、オンライン教材は、動画や双方向型のコンテンツが豊富なため、より理解が深まりやすいというメリットがあります。また、時間や場所を選ばずに学習できるのも大きな利点です。
ただし、書籍やオンライン教材で学ぶだけでは、実践力は十分に身につかないかもしれません。知識を実際の問題解決に活かすためには、研修や実践の機会が必要です。
社内研修の実施
QC7つ道具の実践力を高めるためには、社内研修を実施することが効果的です。社内研修では、QC7つ道具の基礎知識を学ぶだけでなく、社内の実際の問題にQC7つ道具を適用・演習することで、より深い学びを得ることができます。
研修の進め方としては、以下のようなステップが考えられます。
(1)QC7つ道具の基礎知識を学ぶ
各手法の目的や使い方、事例などを、講義形式で学びます。この際、現場での活用イメージを持てるよう、自社の事例を交えて説明することが大切です。
(2)QC7つ道具を使った演習を行う
実際の問題や課題に対して、QC7つ道具を適用する演習を行います。グループワーク形式で行うことで、多様な視点から問題を分析し、解決策を導き出す経験ができます。
(3)演習の結果を発表し、振り返る
演習の結果を発表し合い、QC7つ道具の活用について振り返ります。うまくいった点、改善すべき点などを共有し、今後の実践に活かします。
社内研修を実施する際は、以下の点に留意することが大切です。
- 参加者の業務や関心に合わせて、研修内容をカスタマイズする
- 演習のテーマは、実際の業務に即したものを選ぶ
- 研修後のフォローアップを行い、学びを実践につなげる
改善活動を通じたOJT
QC7つ道具の実践力を高める最も効果的な方法は、実際の改善活動の中で、OJT(On the Job Training)として学ぶことです。
例えば、QCサークル活動などの小集団改善活動の中で、QC7つ道具を活用することができます。メンバー同士で知識を共有し、アドバイスし合いながら、QC7つ道具を用いて問題解決を進めていくのです。
その際、以下のようなステップで進めることが大切です。
(1)テーマの選定
改善すべき問題や課題を明確にし、QC7つ道具を使うことでどのような成果が期待できるかを議論します。この段階で、QC7つ道具の適用可能性を見極めることが重要です。
(2)データの収集と分析
現状を正しく把握するために、データを収集します。収集したデータをQC7つ道具で分析し、問題の原因や改善の方向性を明らかにします。この過程で、QC7つ道具の使い方を実践的に学ぶことができます。
(3)改善策の立案と実行
分析結果をもとに、改善策を立案します。改善策の有効性をQC7つ道具で検証しながら、実行可能な計画を立てます。計画を実行に移し、その効果をモニタリングします。
(4)効果の確認と標準化
改善活動の効果をQC7つ道具で確認します。効果があった施策については、標準化して、他の工程や製品にも横展開します。この段階で、QC7つ道具を使いこなす力が身についていることを実感できるはずです。
以上のように、実際の改善活動の中でQC7つ道具を使うことで、その有効性と限界を肌で感じながら、実践的なスキルを身につけることができます。
もちろん、OJTだけでは体系的な知識を得るのは難しいかもしれません。そのため、書籍やオンライン教材、社内研修とOJTを組み合わせることが、QC7つ道具を本当の意味で使いこなすために必要だと言えるでしょう。
まとめ:QC7つ道具を使いこなして品質向上を目指す
この記事では、製造業の品質管理に欠かせないQC7つ道具について、その概要から具体的な活用方法、さらには新QC7つ道具との関係まで、幅広く解説してきました。
品質管理の要は、現場で起きている問題を正しくとらえ、データに基づいて解決策を導き出し、実行することです。そのために、QC7つ道具は非常に有効なアプローチを提供してくれます。
ただし、QC7つ道具はあくまでツールであり、それを使いこなすのは人です。大切なのは、品質改善への強い意志と、データを丁寧に扱う姿勢、現場の知恵を尊重する謙虚さだと言えるでしょう。
Smart Craftは、QC7つ道具をはじめとした品質管理手法を現場に浸透させ、データ活用を促進するクラウドサービスを提供しています。製造現場のデータを収集・蓄積し、それらを分析、可視化するツールを通じて、品質改善活動をサポートしています。
製造業のDXを推進する上で、品質管理のデジタル化は欠かせません。Smart Craftのようなソリューションを活用することで、QC7つ道具をより効果的に現場に浸透させ、データドリブンな品質改善活動を加速することができます。設備や品質のデータを収集し、リアルタイムに可視化・分析できる環境を整えることが、これからの品質改善の鍵を握るでしょう。まずは資料請求からSmart Craftの導入を検討してみてください。
Smart Craftで製造現場のDXを
始めよう!
「Smart Craft」は、これひとつで工場内のすべての業務プロセスをデジタル化できます。
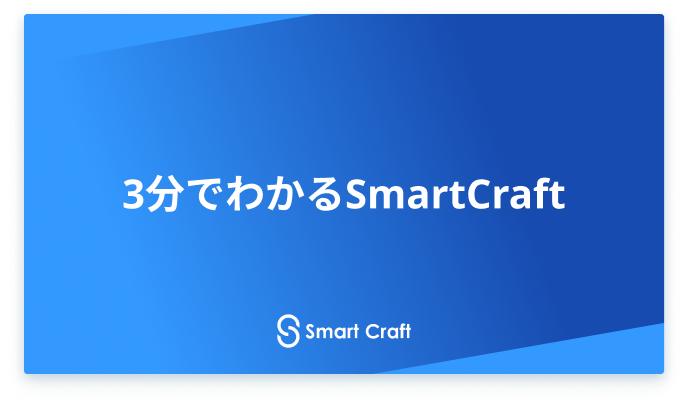
- Smart Craft でできること
- 導入企業の活用事例
- ご利用料金
- 導入の流れ